Nikon’s X-ray CT Inspection Services enables plastic cap and closure manufacturers, especially smaller companies, to access advanced nondestructive testing technology for R&D and troubleshooting. The service offers detailed insights into internal structures, ensuring quality standards are met and preventing leaks or contamination.
In the world of plastic caps and closures, ensuring product quality and preventing leaks or contamination is of crucial importance. Manufacturers of all sizes often face challenges accessing the right technology to inspect their products thoroughly.
Nikon provides X-ray and CT inspection services for manufacturers of all plastic caps and closures. These services are intended to assist in the R&D of new products for the food and beverage, personal care, hygiene, and other sectors and provide detailed feedback when troubleshooting problems that arise during injection moulding or other production processes.
Nikon’s X-ray CT Inspection Service employs its own X-ray CT equipment in centres worldwide, allowing manufacturers to access powerful insights into the internal structure of closures that the nondestructive inspection technique delivers.
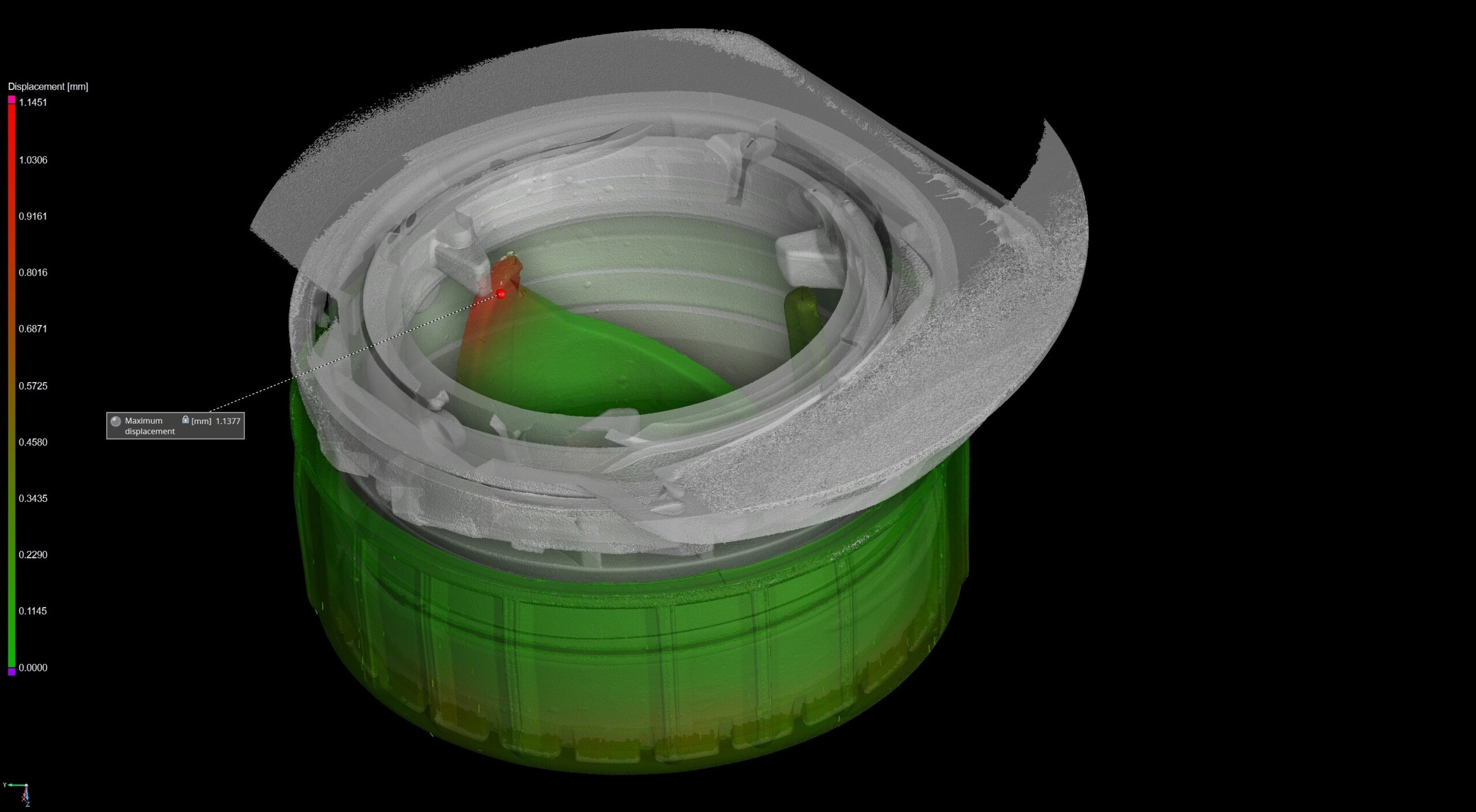
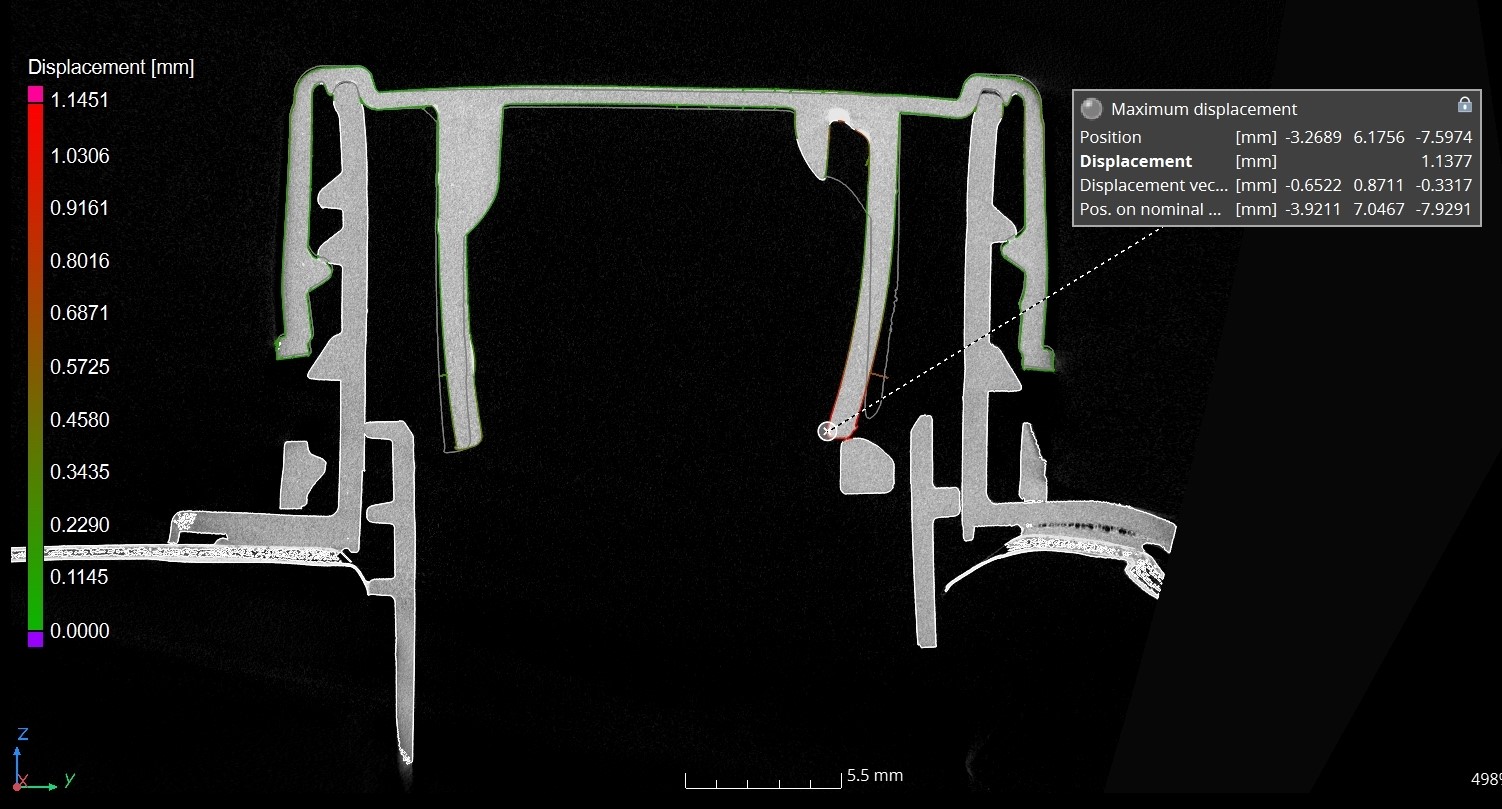
Larger manufacturing groups such as United Caps have bought their own Nikon X-ray CT machine for in-house use. However, smaller firms may need help justifying the cost and choose to continue using conventional metrology equipment instead. That is despite the moderately powerful 225 kV equipment, which can look inside relatively light plastic materials, being at the lower end of the price range.
To meet this challenge, Nikon has introduced its service to provide niche closure producers with technology that allows easier compliance with the HS Code, BRCGS, HACCP, ISO, and other relevant quality standards.
Particularly striking is the enormous variety of plastic closures made for sealing, mainly plastic bottles, tubes, jars, and glass containers. Some simple twist caps are relatively rigid, while others must deform on closure, especially those where a circular cap must be squeezed for safety reasons to become oval before access is allowed to the contents, such as bleach. As another example, other closures must contain shampoo while inverted yet dispense the product when the bottle is pressed.
What is common to all is that they must not leak or allow air ingress or contaminants. Instances of spoilage, health and safety breaches and personal injury that frequently result from such faults can irreparably damage a brand’s reputation. Looking at a closure in its as-manufactured state, while necessary, is therefore not as critical as inspecting it when screwed or pressed onto the neck of its container. Doing this by sectioning the assembly is problematic because plastic deforms when cut, so it is almost only possible to check it precisely with nondestructive X-ray techniques.
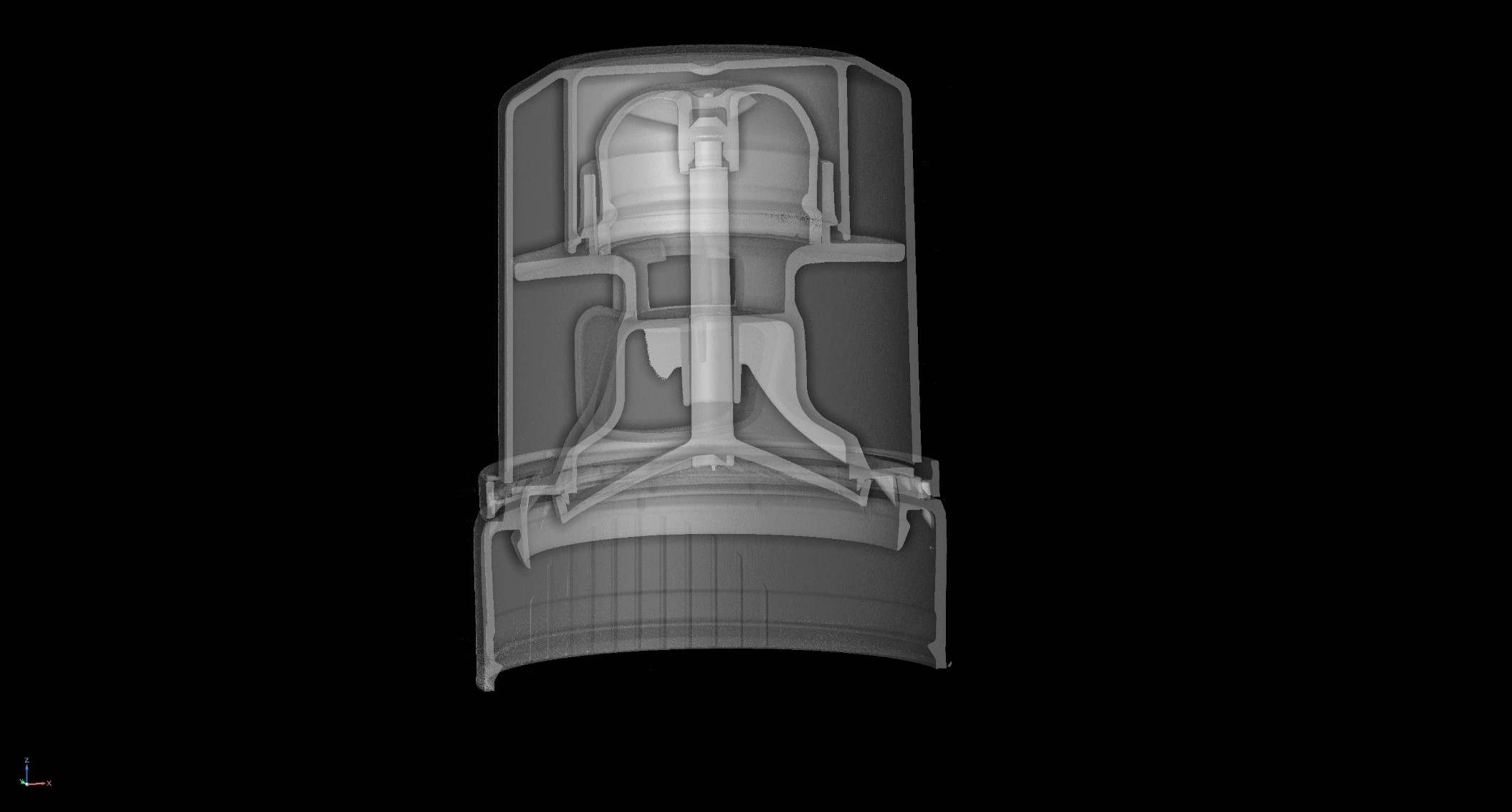
Nikon’s centre in Tring, UK, which is where all of the group’s sources for its industrial X-ray and CT systems are manufactured, is one of the global group’s centres for subcontract inspection. To help closure manufacturers understand the quality control options that are possible with X-ray CT in terms of visual inspection, as well as measurement, including GD&T (geometric dimensioning & tolerancing), resident application engineer Xinyang Hao has prepared a series of slides highlighting CT slices and reconstructed 3D voxel volumes showing the interior of plastic caps. While these images are restricted to the closures themselves, it is notable that metrology and inspection of the plastic injection moulds in which they are produced are also accessible with the penetrating power of X-rays.
Rated from 225 kV to 450 kV, Nikon’s array of modern X-ray CT equipment, including the latest VOXLS systems, can undertake a wide variety of inspection and measurement tasks, including real-time quality control at production line speeds with the assistance of automated load / unload configurations. In this application, the lower power systems are applicable only for R&D and troubleshooting production problems.
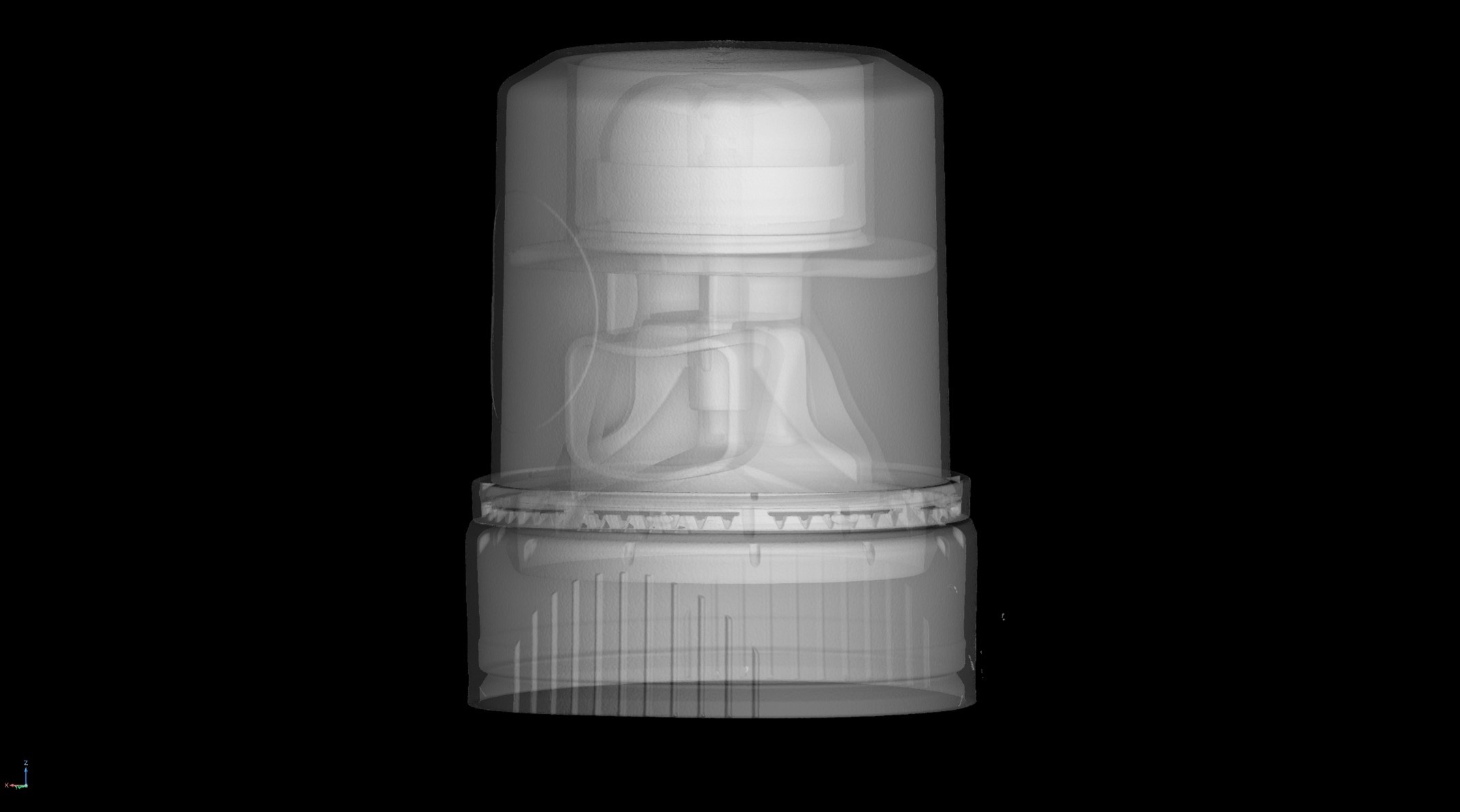
The quality remains despite the significant decrease in scan time of the same closure solution.
By partnering with Nikon, bottle, tube, and jar closure manufacturers gain access to a wide range of CT data acquisition and reconstruction algorithm options, enabling them to customise a system for virtually any inspection application. These options are designed to optimise scan speed and resolution, catering to various needs. The available techniques include conventional circular CT for standard inspections, X.Tend Helical CT for high-quality scans, Half.Turn CT for fast data acquisition, and Tilted CT for laminography.
There is even the possibility of including a fourth dimension, time, in reports by taking a succession of individual sequential CT scan and producing a time-lapse video. This enables a manufacturer to visualise, for example, how the neck of a bottle behaves as a cap is being attached.
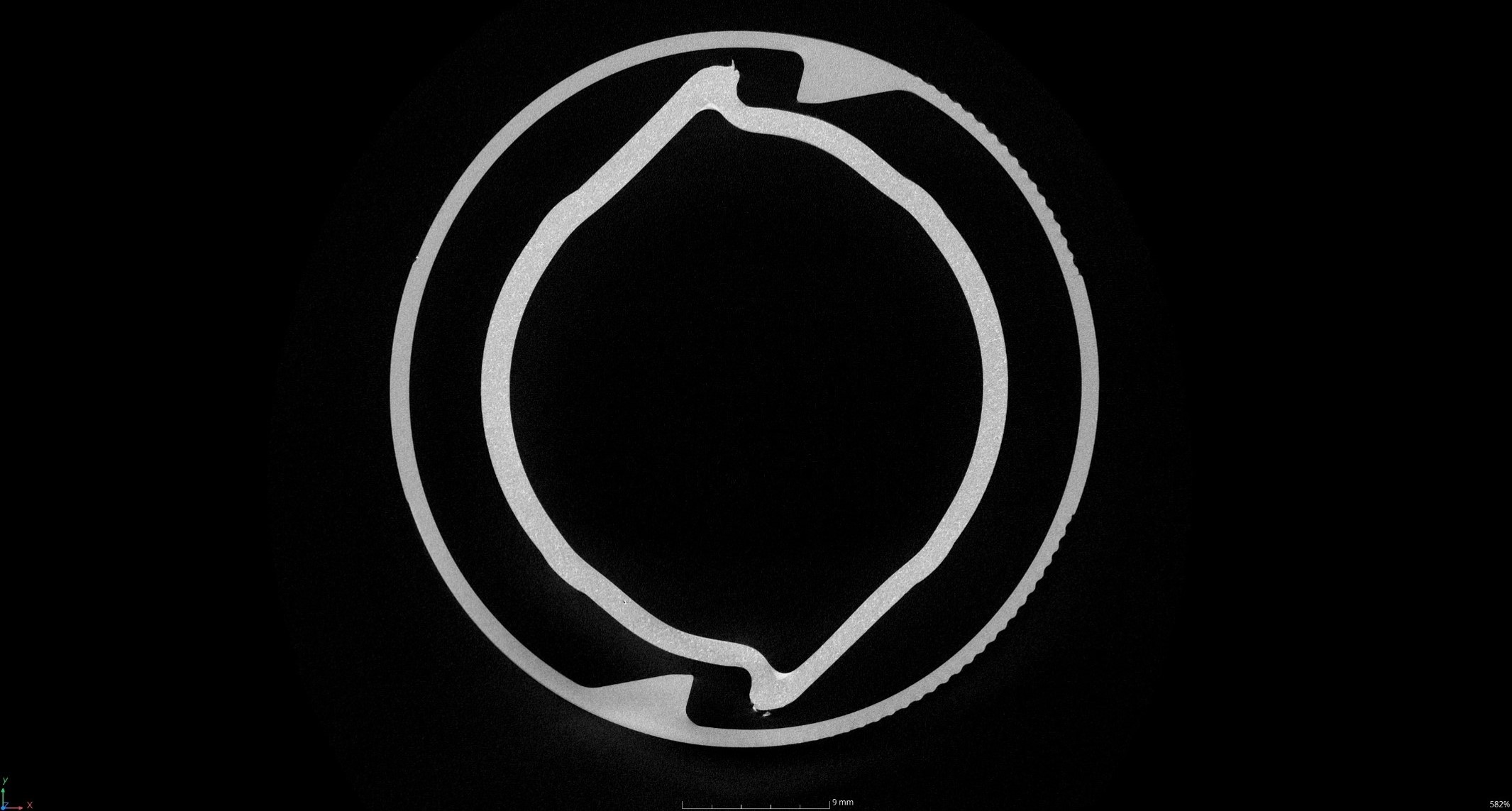
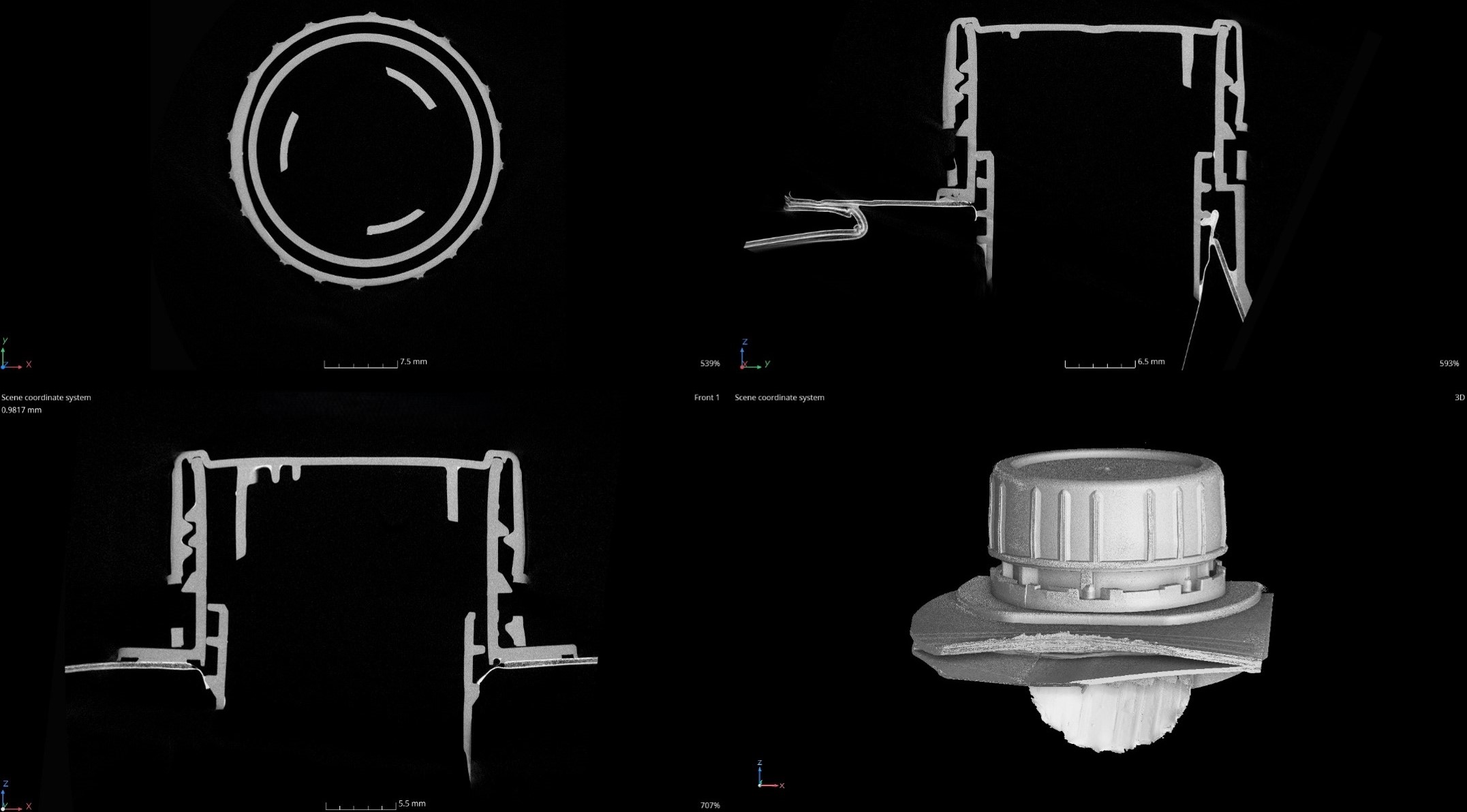