Leading forensic engineering firm S-E-A has integrated Nikon’s cutting-edge X-ray CT technology into its testing arsenal, enabling non-destructive investigation of product failures and pre-market safety validations.
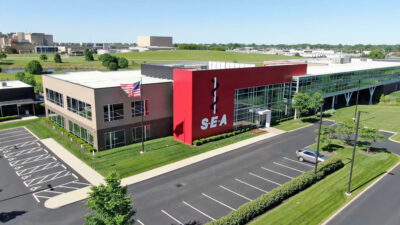
When products fail, from electric vehicles to household appliances, S-E-A steps in to uncover the truth. For over half a century, this forensic engineering powerhouse has been the go-to authority for solving complex product failures and preventing future catastrophes.
From their sprawling 110,000-square-foot facility in Columbus, Ohio, S-E-A’s team of 330+ experts operates like high-tech detectives, investigating everything from devastating fires to battery malfunctions. But their work isn’t just about solving mysteries after the fact. Their pre-market testing services help manufacturers spot potential failures before they become headlines—protecting not just bottom lines, but human lives.
Operating across a 50-acre testing campus that rivals many research universities, S-E-A combines decades of forensic expertise with industry-leading technology. It’s this commitment to keeping ahead of the curve that led them to their latest investment: Nikon Metrology’s advanced X-ray CT scanning system, a tool that literally sees through surfaces to reveal hidden truths. Nikon’s XT H 225 ST 2x X-ray CT scanner was an optimal choice due to its versatility, flexibility, and ability to inspect samples non-destructively.
A look inside to unlock hidden truths
“Much of what we do revolves around forensics,” says Derek Starr, associate director for S-E-A’s Technical Services. “In situations where there’s been a loss of some kind, we’re brought in to figure out what caused that loss and who was responsible for it. Nikon’s CT scanner allows us to look inside these products that are suspected of causing the loss and figure out what’s going on. It’s also a great help that we can accomplish this without destroying the part or object we’re testing, because preserving it in its original condition is preferable.”
The wide range of parts or products that S-E-A can analyze using the XT H 225 ST 2x is what makes it such a valuable piece of equipment for their inspection lab. Features such as 225 kV Rotating.Target 2.0 and Half.Turn CT acquisition mode allow for higher resolution and faster data acquisition. That kind of adaptability is a key part of the value that S-E-A derives from this piece of equipment.
“We have projects involving just about any type of product that you can imagine,” says Benjamin Potter, operations manager of S-E-A’s office in Columbus, Ohio. “Many are battery related, but our testing needs may involve any type of failure mode that might occur with any product. The diversity of what might be imaged with Nikon’s X-ray CT is worth highlighting.”
“Let me give you an example,” adds Starr. “Say we have a water heater that fails. It can be very useful to look at the heating element inside the water heater or look at the pressure relief valve. You often don’t know the actual cause of failure ahead of time until you can get your eyes on it, and sometimes you can’t take it apart because of legal considerations. There might be other parties that want or need to be able to see that water heater. Nikon’s X-ray CT scanner provides a means to nondestructively examine the product and gets us more data than what we can acquire destructively.”
Backward and forward
The nature of S-E-A’s business is to discover why a failure occurred, for example, in an existing part or product. It is also to prevent the creation of such potential failures in parts or products that are yet to be brought to the market. Thus, it can be said that the company looks both backward and forward, depending on the project and/or the client.
“I can give you an example of a forward-looking scenario,” says Starr. “Let’s say a manufacturer wants to mold a plastic structural component. It can be very expensive to make those molds. So, before they spend all that money, they might ask us to help them analyze the strength of that component. One way to do that would be for us to use Nikon’s X-ray CT to scan a prototype of the component, transfer it to a computer model, and run what’s known as a finite element analysis of the product to see how it would hold up under simulated loads. Once the client has that assurance that it’s strong enough, they can go ahead and invest in the new molds.”
“You can certainly use Nikon’s X-ray CT scanner as a forward-looking tool,” adds Sanket Kadam, consulting lead for S-E-A’s Battery Systems and Energy Storage Practice Group. “It can be beneficial for product development, enhancing product safety, improving reliability, or increasing performance. For backward-focused scenarios, such as forensics or failure analysis, the CT scanner is also useful. Overall, depending on the ultimate goals and objectives of the project, the CT scanner can be a valuable asset.”
The case for installation
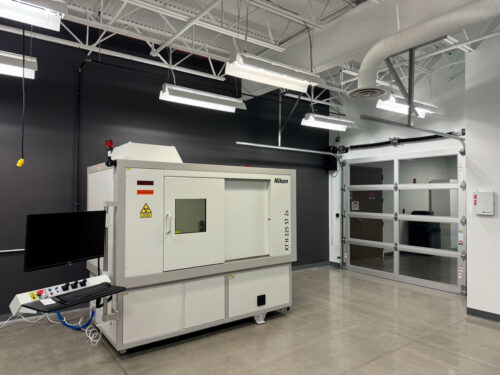
When S-E-A began exploring the use of Nikon’s XT H 225 ST 2x system, team leaders needed to weigh the benefits of X-ray CT as a service vs. installing the scanner directly into their Columbus, Ohio, facility. Ultimately, the decision was made to install it directly.
“The S-E-A team already had confidence in the technology,” recalls Bryan Richar, Nikon’s X-ray CT business development manager. “It made my job easier because they had already utilized other labs that have this equipment, so they had a good idea of what it could do.”
“From my perspective, one of the chief value propositions was our ability to conduct scans at substantially lower costs and substantially higher convenience than shipping the part or product somewhere,” says Starr. “Given the importance of some of these materials from an evidentiary perspective, there was a high potential liability in shipping something off to a remote location and then having it ship back.
“In addition,” Starr continues, “having the CT scanner in-house demonstrates to our clients a greater level of sophistication and capability, as well as our commitment to the excellence of the S-E-A brand.”
“Nikon’s X-ray CT is now part of our ecosystem,” says Kadam. “It’s one of our most important nondestructive tools. We never know what kind of project might be coming through our door tomorrow; different clients have varying requirements, budgets, and timelines to resolve their problems. So, it’s helpful to keep everything within our own ecosystem rather than having to seek out solutions that could add time, cost, and risk.”
Software and other options
Nikon’s hardware systems are extremely well-respected across the industry, particularly for their world-renowned optics. Sometimes, however, clients can overlook the advantages that come from Nikon’s accompanying software systems.
“We’ve been pleasantly surprised by the utility of the software tools that are available with the XT H 225 ST 2x” says Starr. “We were already familiar with the capability of the hardware, but especially when it comes to batteries, the system offers a lot of software tools that automate the analysis steps and save us quite a bit of time. For example, it allows us to compare the ‘before’ and ‘after’ of the same cell or convert one of those physical samples into a model to analyze fluid dynamics or run a failure mode and effects analysis (FMEA). When dealing with battery cell manufacturing clients, being able to automate and dive deep into the characteristics within these cells is of great value and allows us to speak to them with more expertise.”
In addition, Nikon’s X-ray CT scanner includes hardware options that can really expand the benefits of inspection and analysis processes.
“Some of the most useful features of this system are the add-ons that increase the scanning footprint,” Starr continues. “A limiting factor for us has been the size of the part or product. We get samples of various sizes and some of the hardware options allow us to minimize those restrictions.”
Riding the edge of technology
The partnership between S-E-A and Nikon makes for a perfect fit because both organizations are committed to remaining at the leading edge of technology in the future.
“Like our clients, we are going to continue to evolve and innovate,” says Kadam. “Ultimately, this means that while some components may become simpler, the system overall might become much more complex. Having the support of Nikon and the XT H 225 ST 2x X-ray CT scanner gives us greater confidence as we work toward resolving the problems our clients present to us. It’s an important tool in our toolkit.”
“I would say it’s a big piece of the puzzle when it comes to providing greater depth of service to our clients,” says Starr. “If we want to stay in front of our industry, it’s critical to have the widest possible range of testing equipment. This is one of the key pieces of that kit, and we’ll continue to evolve and expand in the years to come.”
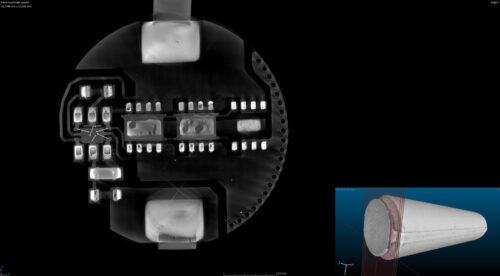
It’s important to note that the expectations of the industries that S-E-A serves will dictate the inspection requirements that the company will continue to invest in going forward. The far-ranging battery sector offers a good example.
“With batteries, scale is very important,” says Starr. “It’s especially important when it comes to what size of an issue can cause a problem. A few millimeters can mean the difference between a battery that works perfectly versus a battery that fails prematurely. So, increasing the resolution and technical ability of the inspection tool becomes critical if you want to be able to properly analyze the batteries.
“As batteries have evolved, and as that evolution continues, manufacturers will try to add more energy into a smaller area,” Starr continues. “Therefore, the scale is becoming smaller and smaller, and the tools needed to analyze that scale need to offer better and better resolution.”
“A battery cell often represents the technical limit or building block for more complex battery packs or systems,” says Kadam. “Specifically, at the chemical/material level, lithium-ion batteries primarily include electrodes, separators, electrolyte, and current collectors. X-ray CT can assist with the nondestructive three-dimensional visualization of battery systems at various length scales, from macroscopic features of battery packs to microscopic details of internal structures, including electrodes and current collectors. To further explore multiple length scales, scanning electron microscopy (SEM) is a powerful imaging technique that provides high-resolution images of surface topography and composition, typically down to the nanometer scale. S-E-A also has an SEM on-site at the Columbus, Ohio, location. Additionally, for lithium-ion batteries, atomic-level analysis is crucial for understanding phenomena such as electrode material properties, failure mechanisms, and material development. Therefore, employing suitable tools that provide insights into the inner workings of battery systems across multiple length scales is essential.”
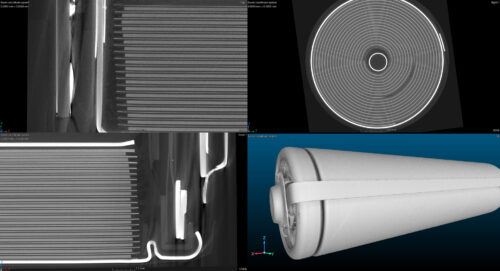
Ultimately, a company like S-E-A depends on the best inspection tools to do their work properly, and team leaders rely on the input of their engineers and technicians to tell them the equipment that will advance their efforts.
“For years, this has been a technology that our staff has been clamoring for,” says Starr. “There’s a lot of excitement now that we finally have Nikon’s XT H 225 ST 2x X-ray CT scanner in our hands. We’re looking forward to the chance to work with it and expand the quality of inspection services we can offer to our clients.”
To learn more about S-E-A Limited, visit: https://sealimited.com/
More information about the XT H 225 ST 2x is available here:
https://industry.nikon.com/en-us/products/x-ray-ct/xt-h-series/