Toby French, Applications Engineering Manager within the X-ray Business Unit, has been working within Nikon Metrology for 8 years. Today we spoke to him about his responsibilities, his expertise and the new Offset.CT module launched a few weeks ago.
Hi Toby, could you please tell us what are your individual responsibilities within Nikon Metrology?
I am Applications Engineering Manager, responsible for the inspection services of the X-ray Business unit concerning the UK and European territories. Using the fleet of Nikon Metrology’s X-ray and CT systems that we have on-site at our demo facility, we assist companies by utilizing X-ray and CT techniques in order to provide non-destructive testing, primarily through fault-finding, and to visualize and analyze both external and internal geometries of customer samples. Visual inspection and in-depth CT data analysis such as porosity and inclusion analysis, CAD compare, and co-ordinate measurements are often all in a day’s work with the inspection service.
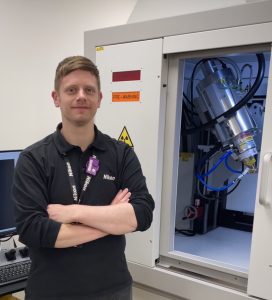
What are the best parts of your job?
I would say the best part of my job is helping customers overcome issues. I often joke with customers that “we like other people’s problems”, and whether it is a one-off inspection or a long-standing relationship with a particular customer where we can assist with refining their quality and production processes, it’s fantastic to play an integral role and provide them with a solution, as well as information and knowledge that they wouldn’t able to ascertain using other inspection techniques. Being able to demonstrate CT data to customers who have not yet seen how powerful a tool it is can also be very satisfying as it tends to have a real ‘wow-factor’. I would say it is very rare to demonstrate CT data in the first instance and not have the customer excited about its possibilities.
Any anecdote that you would like to share with our readers?
If you spend enough time with the inspection services you will likely scan almost anything and everything you can think of. From frozen birds of prey to items recovered from the Titanic and high-profile forensic work, you never really know what you could be inspecting in the days and weeks ahead. The wide variety of sample types and industries that we support with X-ray and CT make each day diverse and exciting, and we often get an insight into pioneering technologies and manufacturing processes before others.
You recently launched a new offset CT reconstruction algorithm, what benefits can customers expect from using it?
Offset.CT is now an invaluable tool to the inspection service and its customers. With the introduction of the Offset.CT module not only can we can scan items that are larger than the imaging panel but can also achieve higher resolution than ever before when scanning objects of smaller sizes. This allows us to maintain higher resolution with a wide array of samples and is already incredibly popular with our customer base.
What sectors & industries can benefit from using it?
We have now demonstrated the benefits of the Offset.CT module on samples concerning most industries, which to me confirms its value for any application. I would say that primarily we have been using it for the automotive industry, and being available on all Nikon Metrology CT systems with energies of 180kV – 450kV the offset possibilities are endless.
As a Nikon Metrology expert, what is your favourite system feature & why?
The 225kV rotating target has always been a favourite feature of mine – being able to treble the flux within a fixed acquisition time or significantly reduce the scan time without compromising scan quality is brilliant. With the Rotating.Target 2.0 being able to run at three times the power (W) of a static reflection target without affecting the microfocus spot size, denser samples can be penetrated which really broadens the scope of 225kV possibilities. Being used in conjunction with the Offset.CT module, the Rotating target 2.0 allows cycle times to be significantly reduced and together they make an incredibly powerful inspection tool.