Nikon 提供的 X 射线计算机断层扫描 (CT) 技术让光学元件生产巨头 Tochigi Nikon 发现了颠覆性的解决方案,从而使精密塑料注塑成型流程发生变革。
总部位于日本的 Tochigi Nikon 面临着一个全行业性问题:在制造相机镜头等圆柱形塑料部件时会非常困难,因为这些产品在生产过程中需要尽可能接近高精度的正圆型。为实现这一目标,必须修改模具形状,在此期间需要投入大量的人力和时间,并且通常还需要熟练的技术人员参与并执行多个校正周期。
如今,Tochigi Nikon 利用 Nikon 的 CT 技术简化了模具校正流程,整个过程只需极短时间完成,可以大幅节省成本并提高效率;Tochigi Nikon 工程师仅用三个月就熟悉了这种新模式。
Tochigi Nikon 成立于 1961 年,是 Nikon 的全资子公司,负责为全球的 Nikon 集团企业生产光学元件和模块。凭借先进的精密镜头加工技术,Tochigi Nikon 开发出了应用于全球各行各业的丰富光学镜头。
在 Tochigi Nikon 内部,第一生产工程部专注于无反光镜相机的替换用镜头,工程部门则负责批量生产树脂注塑件(包括用于无反光镜相机中的零件)。
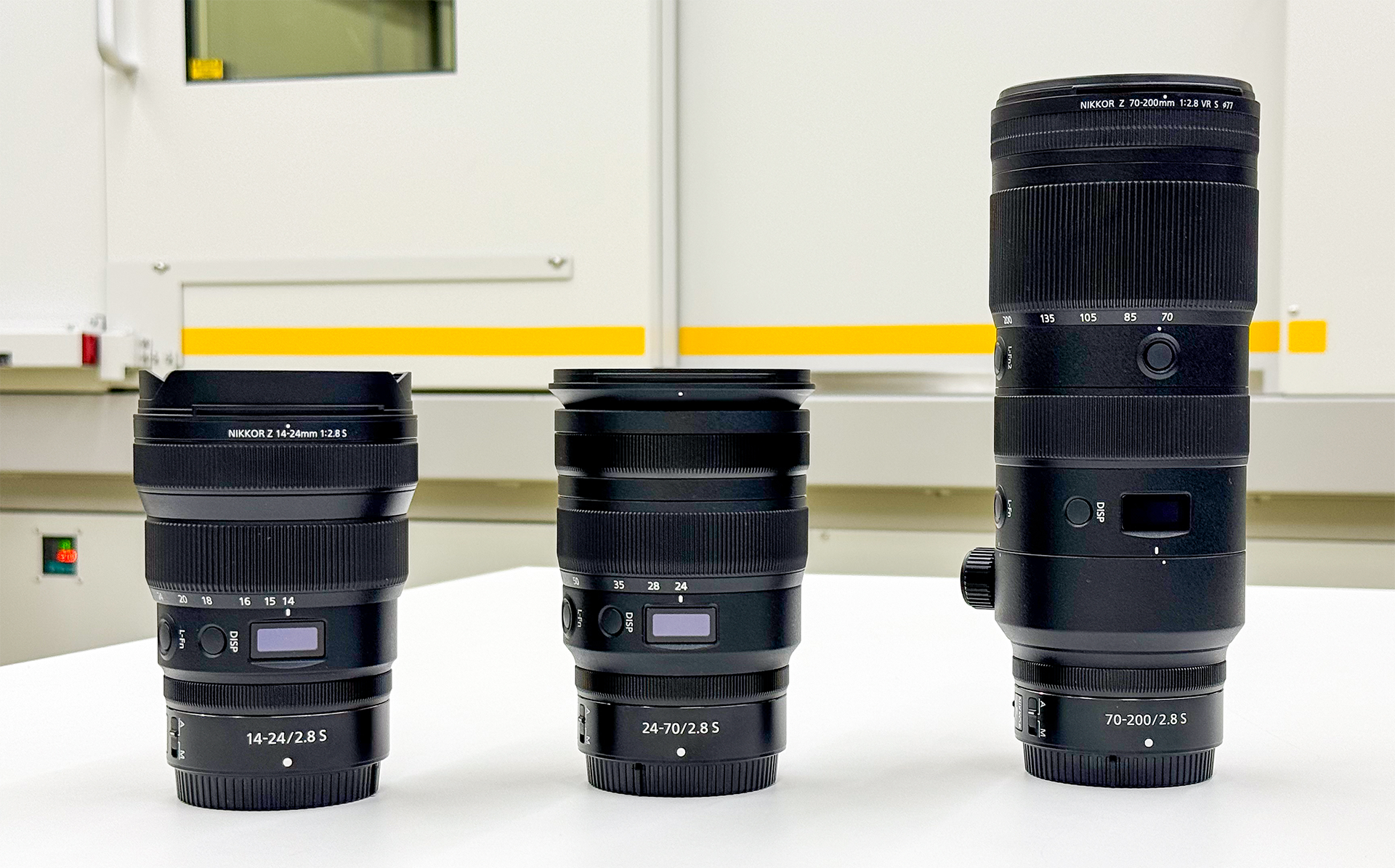
用于替换镜头的树脂注塑件形状必须是尽可能接近正圆的圆形。然而,由于行业的限制,这些部件在成型时并不具有正圆形,因此需要进一步处理。
为了解决该问题,需要修改模具,使其更接近正圆形。这个“模具校正”过程通常要重复两到三次,从而逐渐提高精度。
利用 Nikon 的 CT 成像技术增强模具校正流程
但这并非唯一挑战。近年来,由于树脂注塑件体积更小、重量减轻且功能增强,其形状变得愈加复杂。
即使使用传统 CMM 和影像测量仪器测量这些部件也并非易事,因为需要测量程序和创建模具修改指令,这会增加整体工作量,使过程更加耗时且昂贵。
Tochigi Nikon 一直在寻求解决这些难题;在了解 Nikon 的 MCT225 后,立即意识到该产品可以帮助简化模具校正流程,从而节约成本并提高效率。
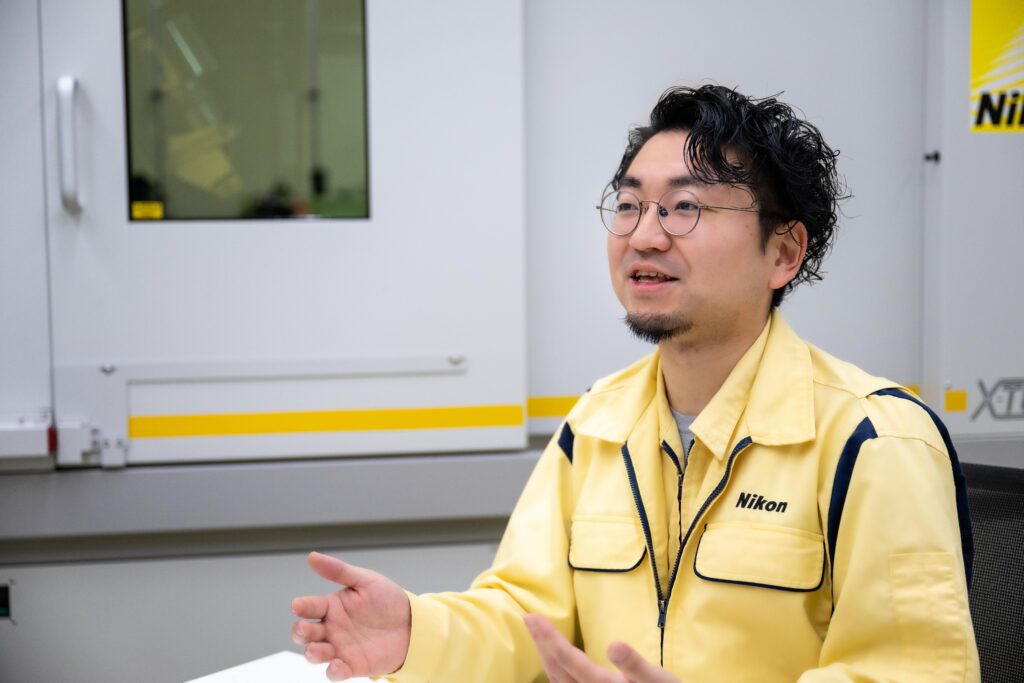
Tochigi Nikon 工程师 Shota Miyamoto 解释道:“我们选择 Nikon 工业 X 射线 CT 技术的原因之一是,Nikon 在微焦点 X 射线源这一全球最大市场中占有最高份额。”
Nikon 的测量计算机断层扫描 (MCT) 是 Nikon 开发和制造的高功率微焦点 X 射线源,具有图像质量高、运行寿命长的特性。Nikon 的 MCT225 充分利用这些特性,具有高精度测量能力,在测量单个粗糙材料样品时精度可达 9+L/50μm。
Miyamoto 解释道,该产品的其中一项关键优势在于,能够在没有任何物理接触或限制条件的情况下有效测量产品的内外部尺寸。这种非接触式测量方法符合德国技师协会制定的 VDI/VDE2630 标准,确保可靠且精确地测量尺寸。
使用 Nikon 的 MCT225 自动测量模具
模具补偿旨在修改通过模具生产出来的零件的尺寸,使尺寸符合预期。过去,在制造试验产品后,除使用来自 CMM 和影像测量机的自动测量结果外,在模具校正流程中还使用数字千分尺、PIN 规和其他工具进行手动测量。
通过数次的测量和工具校正,对模具进行修正,逐步提高零件精度。

“借助 MCT225,在创建成型零件测量程序时,只需使用 CAD 数据即可完成测量程序的创建过程,”Miyamoto 解释道。“我觉得,除了不需要制备实物样品之外,最大化也解决了不需要使用精确夹具来放置零件。
此外,不再需要高技能地创建多个探针角度来生成测量程序,也不需要在检查测量状态时重新执行程序,工作量大幅减少。”
简化模具修正工作流程
MCT225 采集的数据通过批处理自动转换为 STL 格式。STL 数据和测量程序存储在服务器上。然后,工人只需简单读取记录条件并放置零件即可,这样就可以将 X 射线 CT 扫描所需的时间缩短到五分钟。
“现在,我们可以从服务器读取 STL 数据和测量程序,在办公桌上进行测量;与以前的系统相比,大幅减少了操作员的工作量和时间,”Miyamoto 说道。“Tochigi Nikon 开发出专门用于测量圆柱的内部宏,与以前的方法相比,将零件测量程序的创建时间和修改时间减少达 50%。”
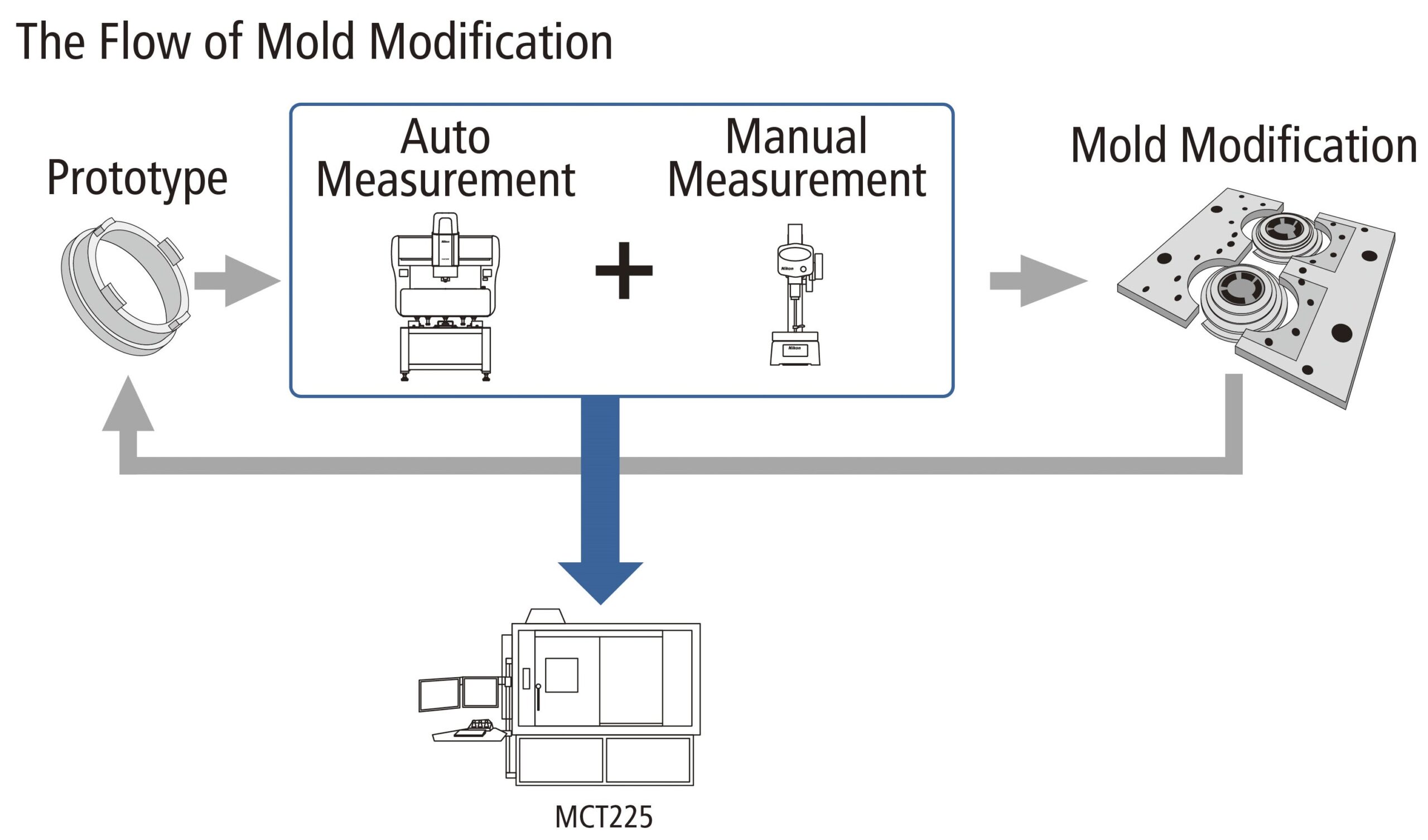
通过 MCT225 获得的 STL 数据可与 3D 测量软件 Polyworks Inspector 配合使用,以确定通过彩色图显示的 3D 数据中的模具补偿量,这大大简化了测量之后的分析流程。Miyamoto 表示,借助 MCT225,他的工程师团队只用三个月就能完成测量工作。
“此外,通过简化测量程序和创建模具修正的文件,我们将完成模具修正所需的时间减少了八周,即减少了 30%。”
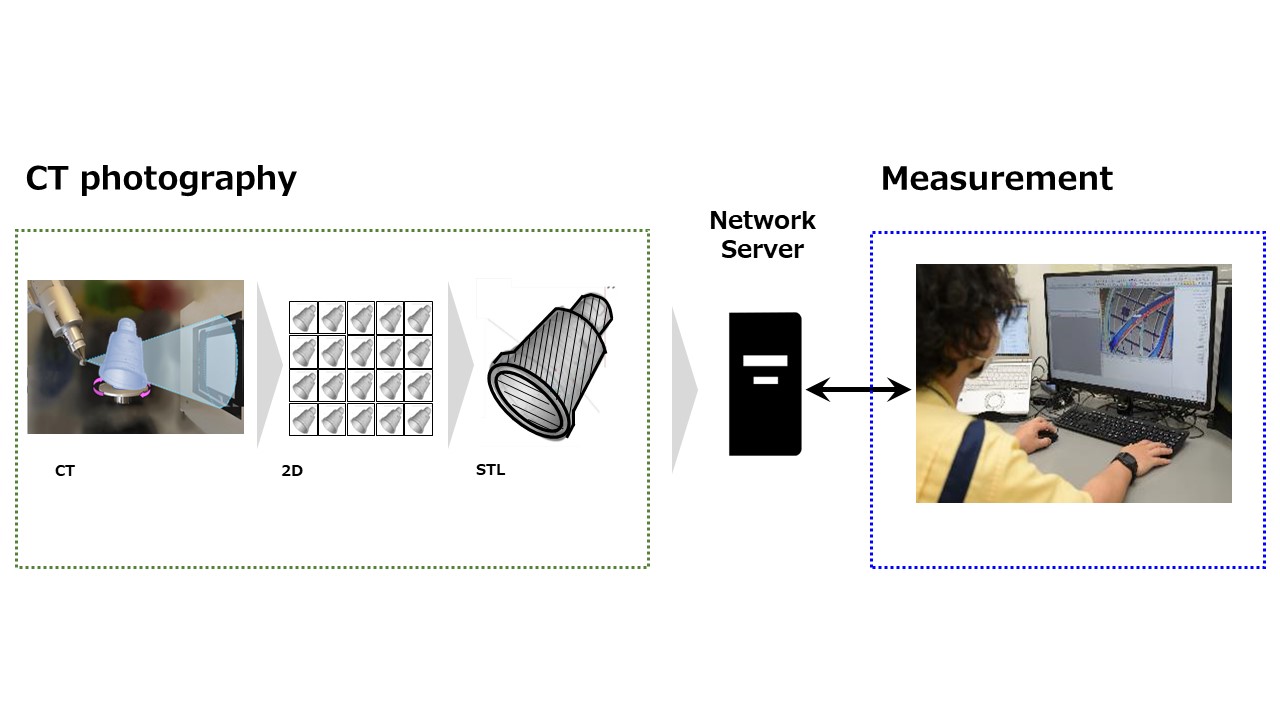
Nikon 的 MCT225 为测量流程带来创新
MCT225 能够测量任何形状的 3D 数据,即使在狭窄空间中也不会遗漏。这对于测量树脂注塑件非常有用。例如,如果某个对镜头功能至关重要的零件没有居中,就很难使用 CMM 进行测量。
“MCT225 可将整个图像转换为 3D 空间,在测量时不受形状的限制,可自由进行测量,不会缺失任何数据,”Miyamoto 表示。“可以在没有接触或限制条件的情况下拍摄图像,不需要专用夹具工具,拍摄程序本身也不要求操作人员具备专业技能。它可以与 Microsoft Excel 以及传统测量方法配合使用。我认为 MCT225 为测量流程带来了重大创新。”
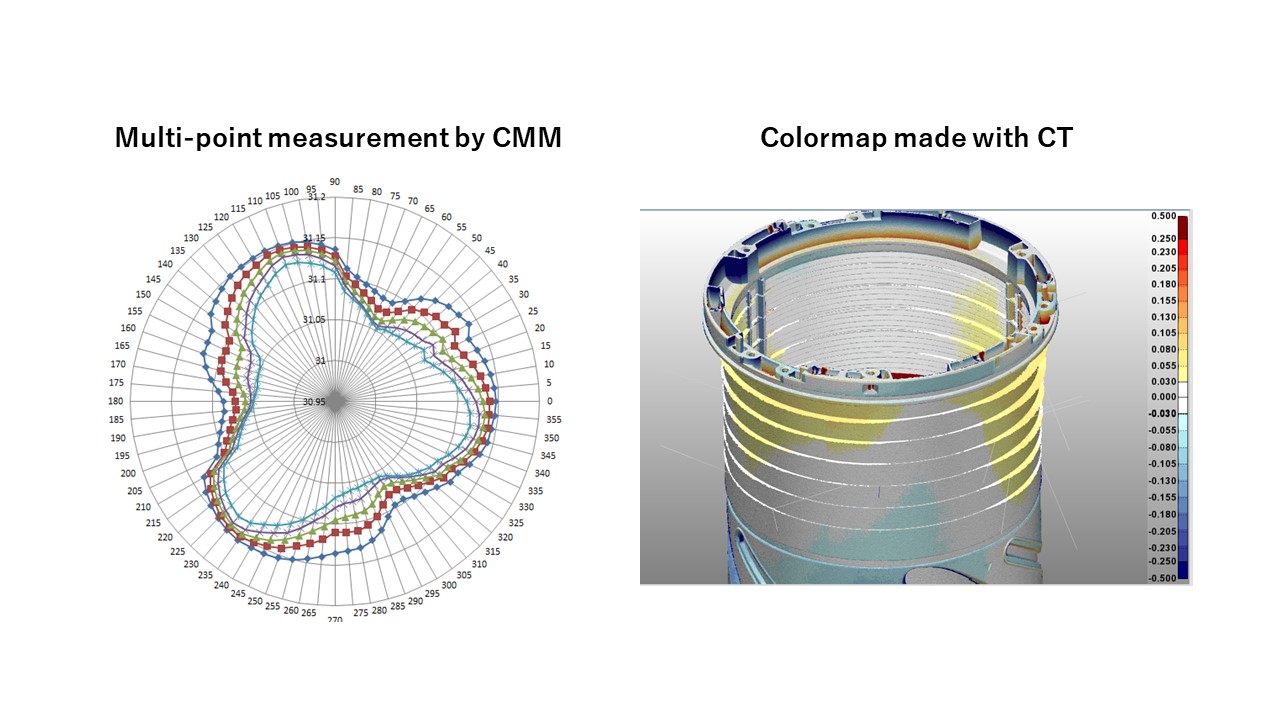
在 2020 年的财报中,Tochigi Nikon 实现了约 80% 的成本降低,这得益于多个方面,包括测量程序创建时间减少、校正周期缩短、多重技能员工以及分包成本的降低等。
“未来,我们希望通过 Volume Graphics 的几何校正功能来处理自由曲面,”Miyamoto 表示。“借助逆向工程 CT 测量、几何校正和模具加工,我们可以提高零件自由曲面的精度,并利用 3D 来提高效率。”
随着 X 射线 CT 技术从传统 CMM 和图像测量向更高更先进的转变,未来的注塑模具制造流程将发生重大变革。一些类似 Tochigi Nikon 的制造商采用这一变革性的方案,他们能够大幅提升生产率,从而在要求日益严苛的全球市场中提升竞争优势。