La technologie de tomographie numérique aux rayons X (CT) de Nikon a permis à Tamron, le poids lourd des objectifs d’appareils photo numériques, d’obtenir des informations sans précédent sur les subtilités de ses composants de pointe.
Basée au Japon, Tamron était confrontée à des défis en matière d’analyse précise de la déformation des composants de lentilles moulés en plastique. L’appareil MCT225 de Nikon a résolu ce problème en permettant à l’entreprise de créer des modèles 3D à partir de numérisations CT, qui peuvent être directement comparés à des modèles CAO et à des résultats d’analyse à l’aide du logiciel VGSTUDIO MAX.
Cela a apporté une foule d’avantages, éliminant la nécessité d’aligner plusieurs points de mesure et permettant l’observation de l’orientation des fibres dans les plastiques renforcés de Tamron : un développement crucial qui a amélioré la précision de l’analyse.
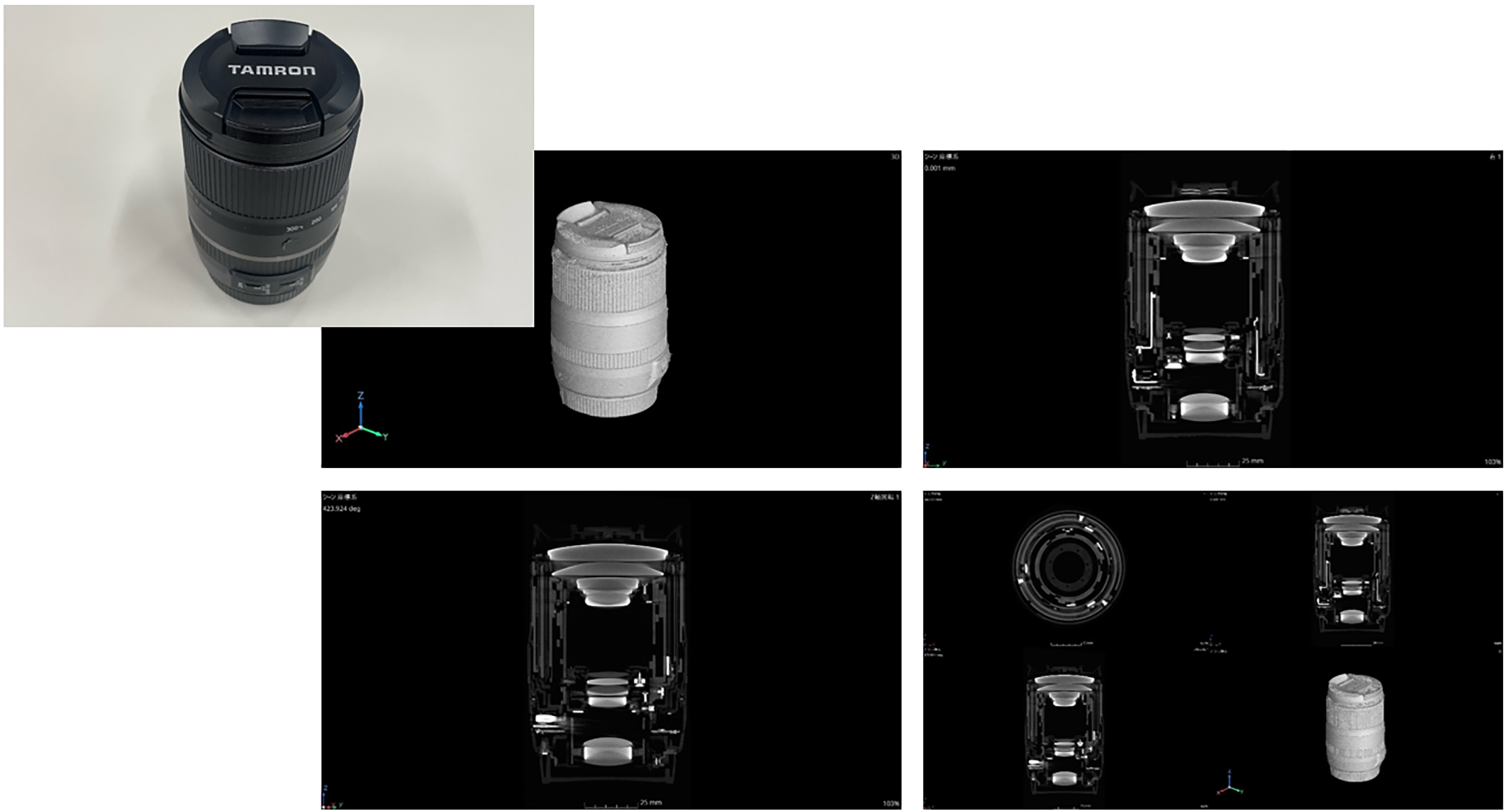
Tamron, dont le siège social est situé à Saitama City, n’a cessé de rechercher une technologie optique avancée, combinant créativité et force technique pour développer et fournir des produits de haute qualité auxquels les utilisateurs du monde entier font confiance.
L’histoire de Tamron s’étend sur plus de sept décennies. Fondée en 1950 sous le nom Taisei Optical Equipment Manufacturing, l’entreprise a d’abord fourni une technologie pour le polissage des lentilles d’appareils photo et de jumelles.
Au fur et à mesure que son expertise s’est développée, elle s’est lancée dans la fabrication d’objectifs interchangeables pour les appareils photo reflex. En 1958, elle a déposé sa marque et, en 1970, l’entreprise a officiellement changé son nom en Tamron.
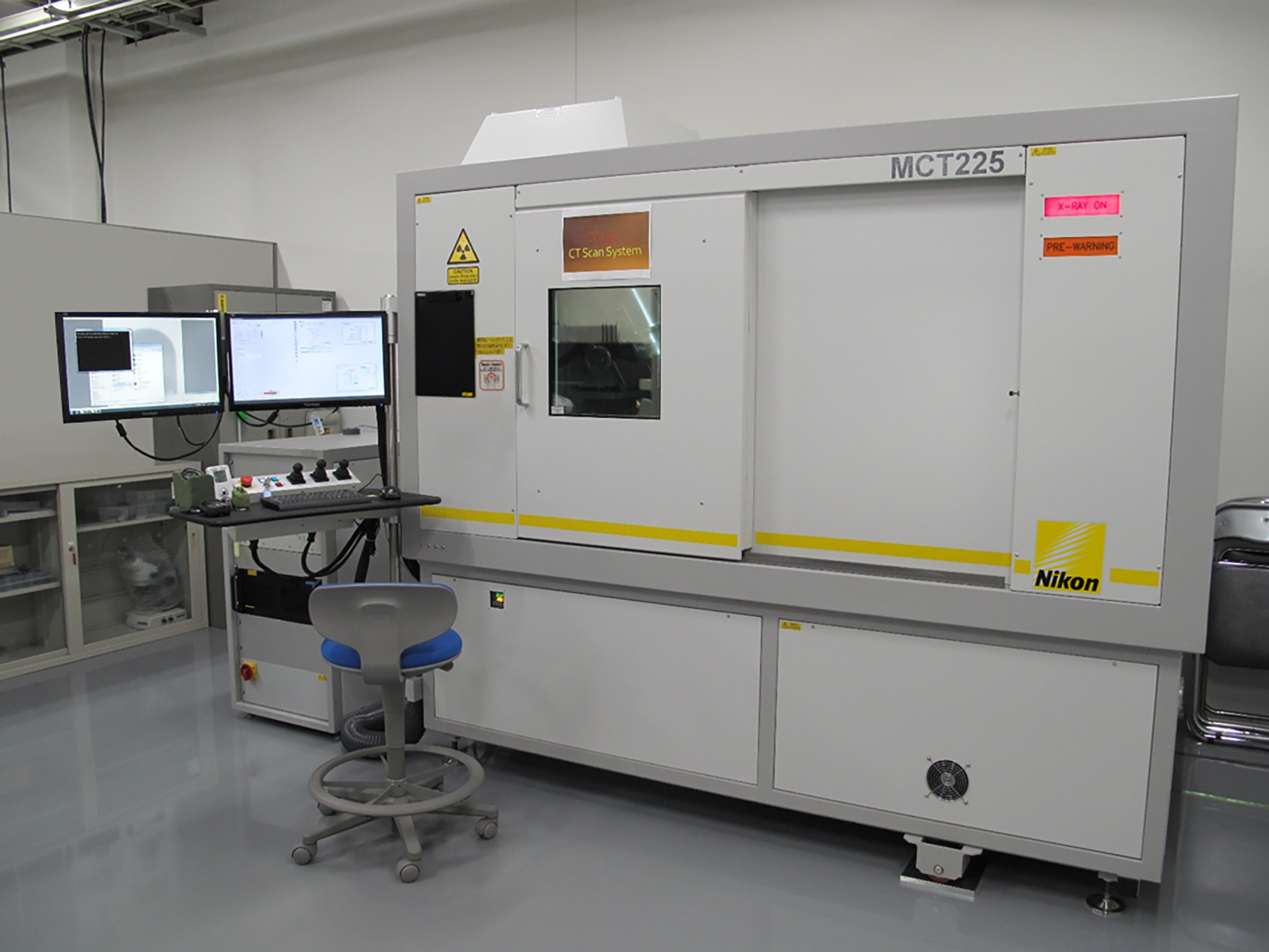
Au fil des années, Tamron est devenue un fabricant d’équipements optiques complet, exploitant une structure commerciale intégrée à l’échelle mondiale englobant la recherche et le développement, la planification, la conception, la production, les ventes et l’assistance. Son portefeuille de produits s’est élargi pour inclure des objectifs interchangeables de marque pour les appareils photo reflex numériques destinés au grand public, des produits OEM et des composants optiques destinés à divers secteurs industriels.
Le MCT225 fournit des informations sur la qualité du produit fini
En avril 2014, Tamron a adopté le système de métrologie de CT par rayons X de Nikon MCT225, ainsi que deux ordinateurs reconditionnés. Cette installation initiale a permis à Tamron de capturer des images et d’évaluer la qualité des pièces moulées en plastique et des composants mécaniques critiques de ses unités de lentilles. Tamron a pu évaluer la qualité du produit fini en comparant les spécifications de conception avec les mesures réelles obtenues par imagerie CT à l’aide du logiciel VGSTUDIO MAX.
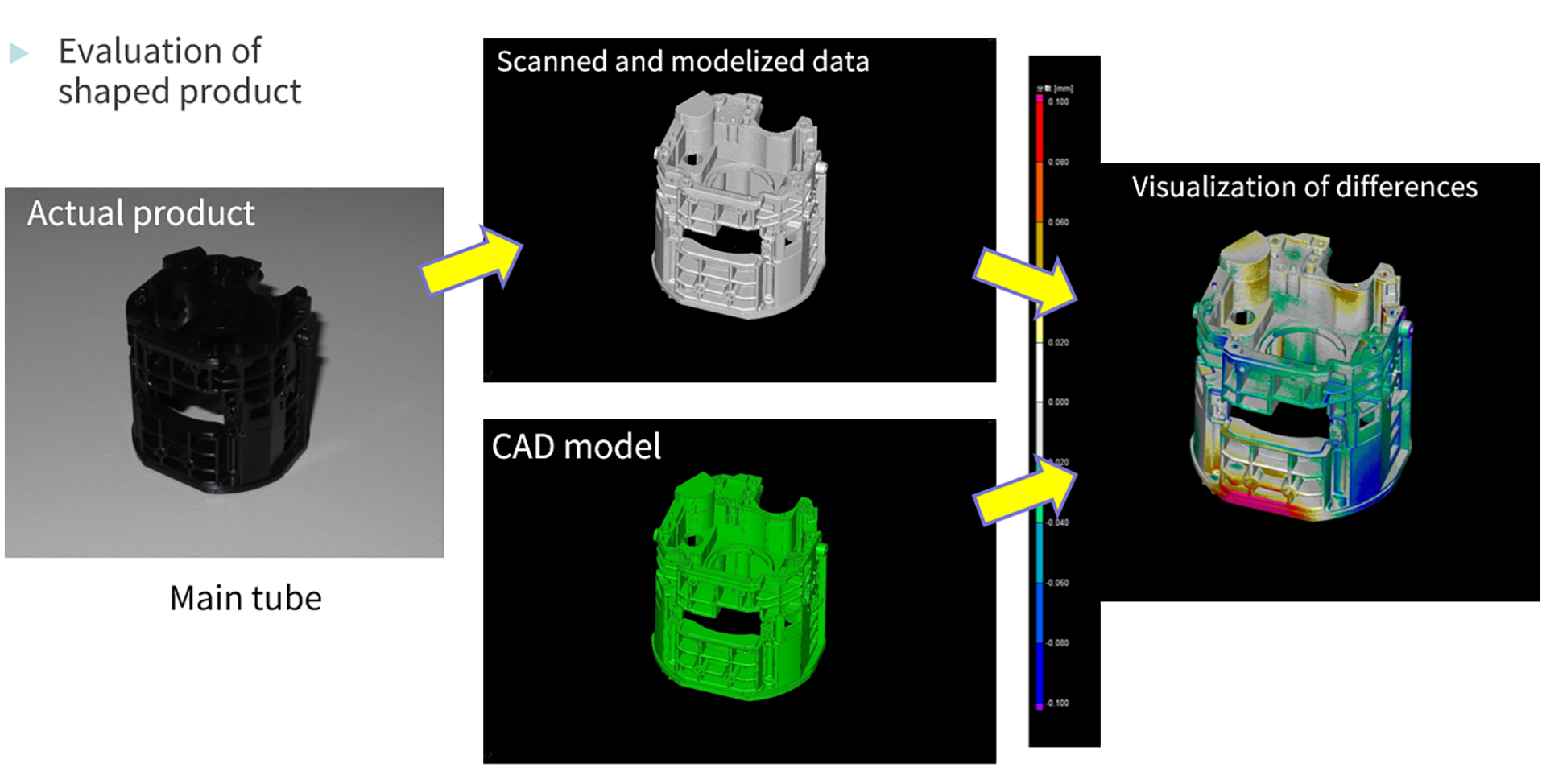
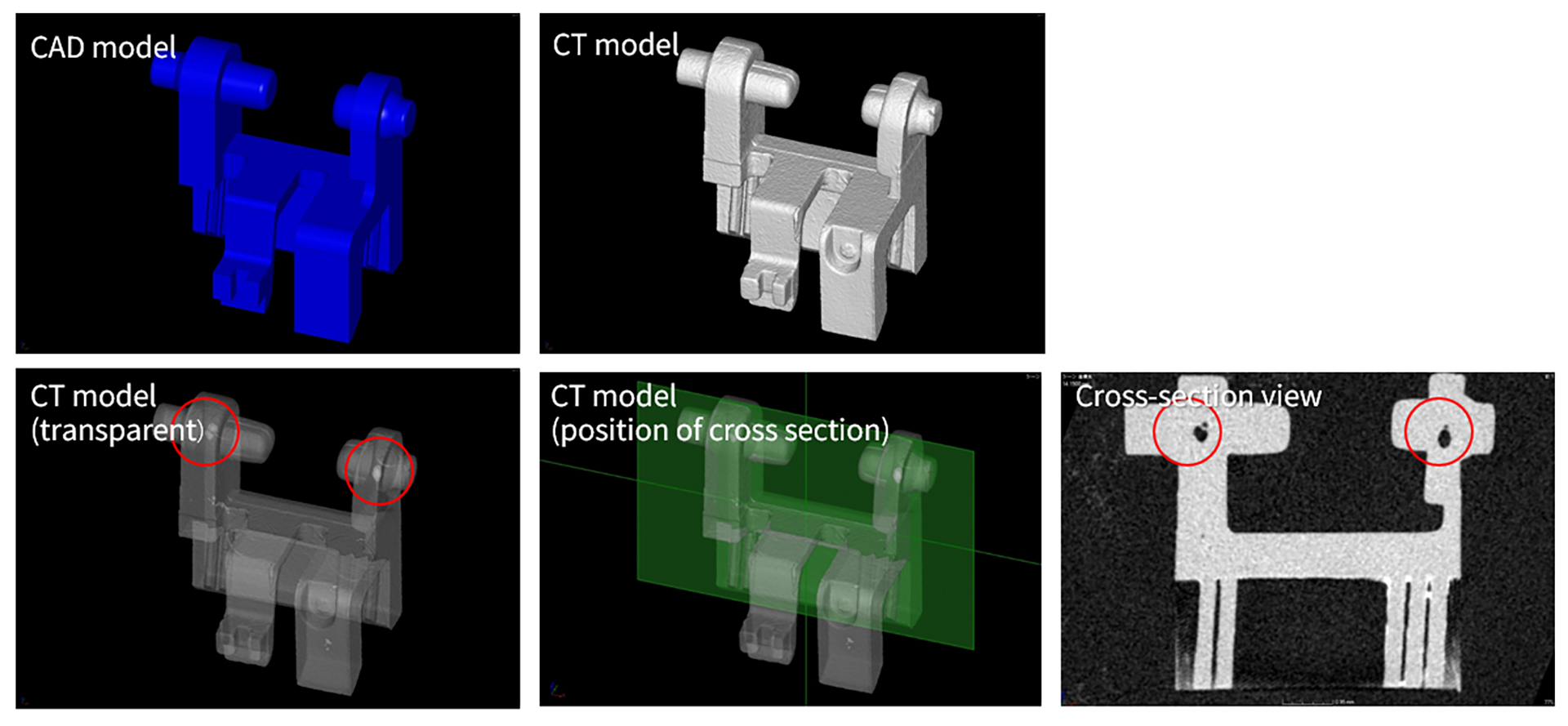
Au fil du temps, le MCT225 s’est avéré tellement précieux qu’en octobre 2023, Tamron a décidé d’élargir ses capacités en ajoutant une seconde unité MCT225 et un ordinateur reconditionné supplémentaire.
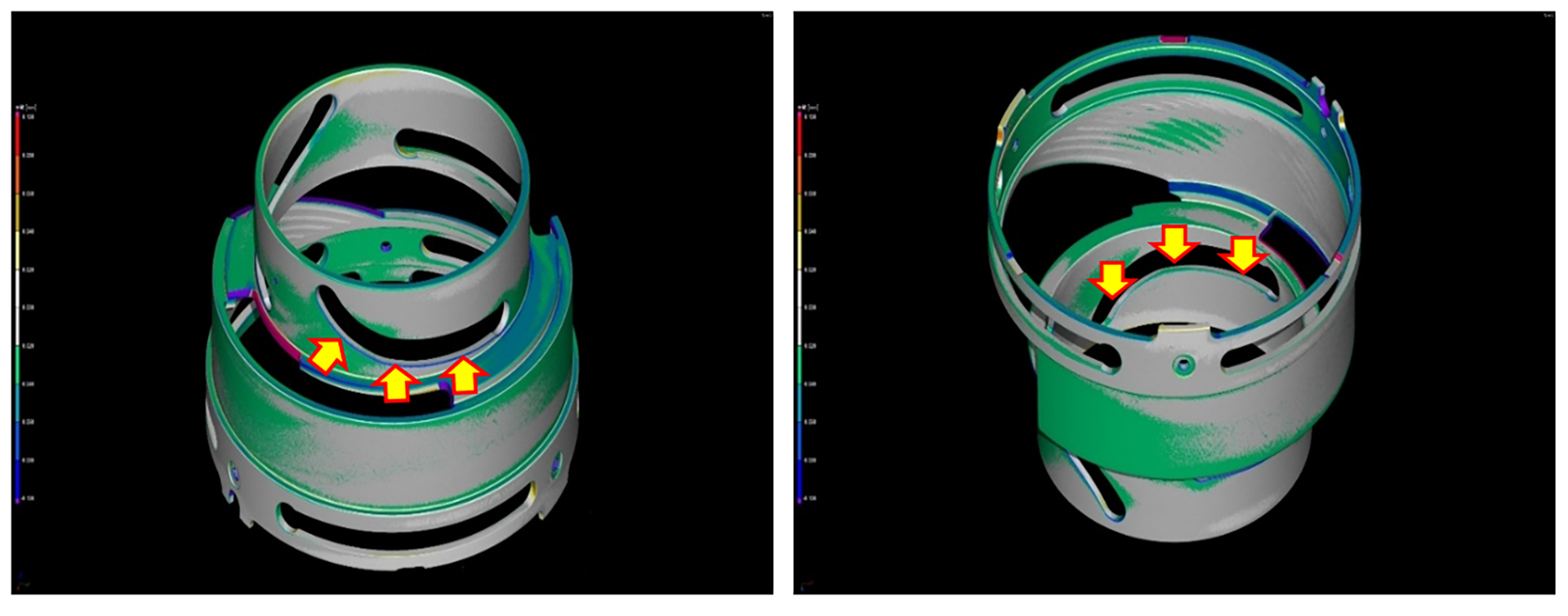
Les enseignements tirés de ces évaluations ont ensuite été intégrés aux résultats de l’analyse des flux, ce qui a permis à Tamron de continuer à améliorer la précision de ses processus d’analyse. Au-delà de l’évaluation de la qualité du produit fini, les systèmes MCT225 ont également facilité l’évaluation de la variabilité des produits moulés, la détection des vides et des fissures, l’observation de l’orientation des fibres dans les plastiques renforcés, l’examen des défauts dans les états d’assemblage et les substrats électroniques, et enfin, l’analyse des produits concurrents.
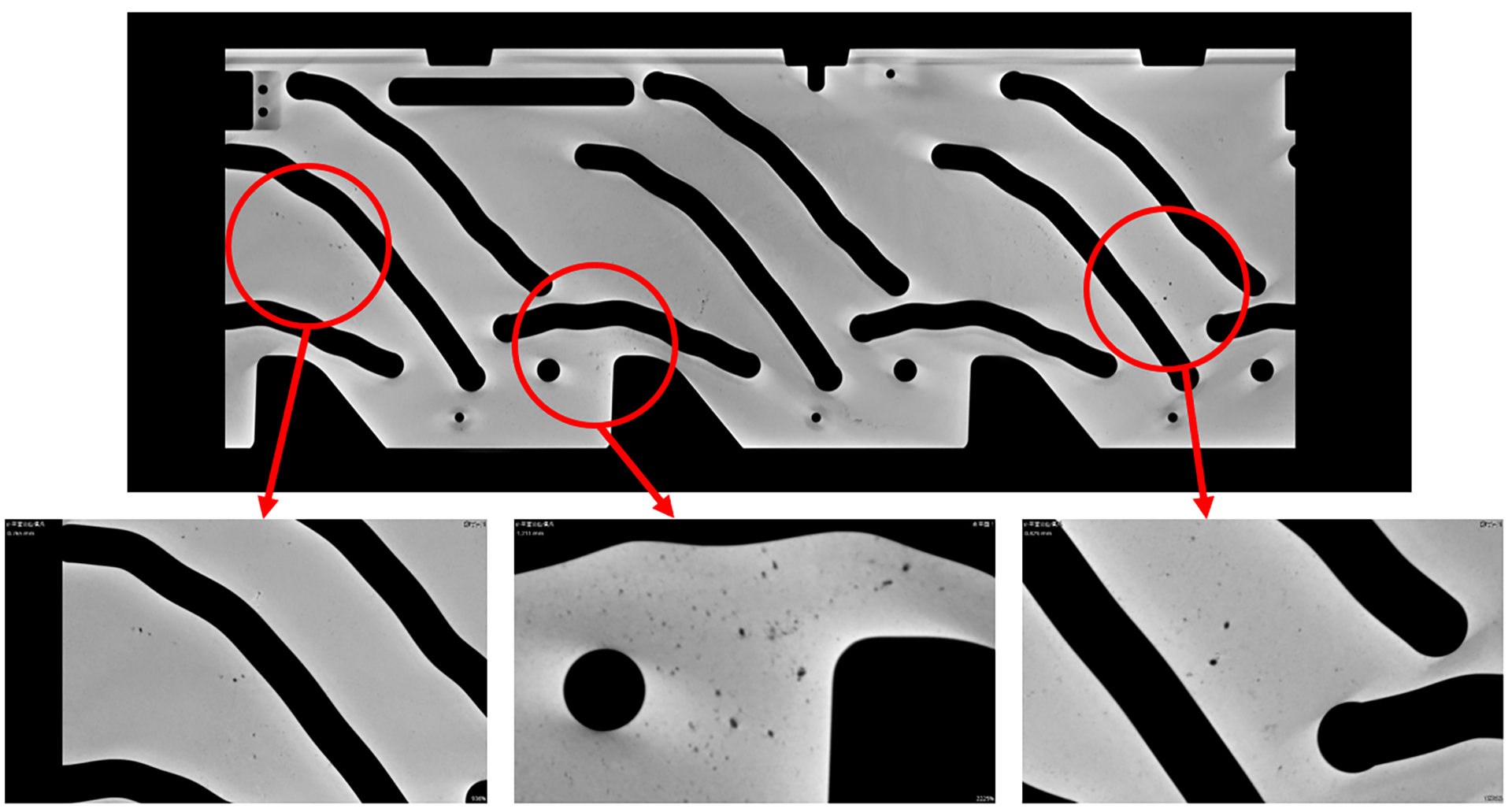
« Nous trouvons que l’appareil et le logiciel du MCT225 sont très conviviaux », indique le porte-parole de Tamron. « Nous avons toujours obtenu une réponse rapide à nos demandes d’entretien régulier ou de dépannage. Je suis également rassuré par la possibilité de louer une salle de mesure Nikon si l’appareil ne peut pas être utilisé pendant un certain temps, par exemple en cas de maintenance ou de problème urgent. »
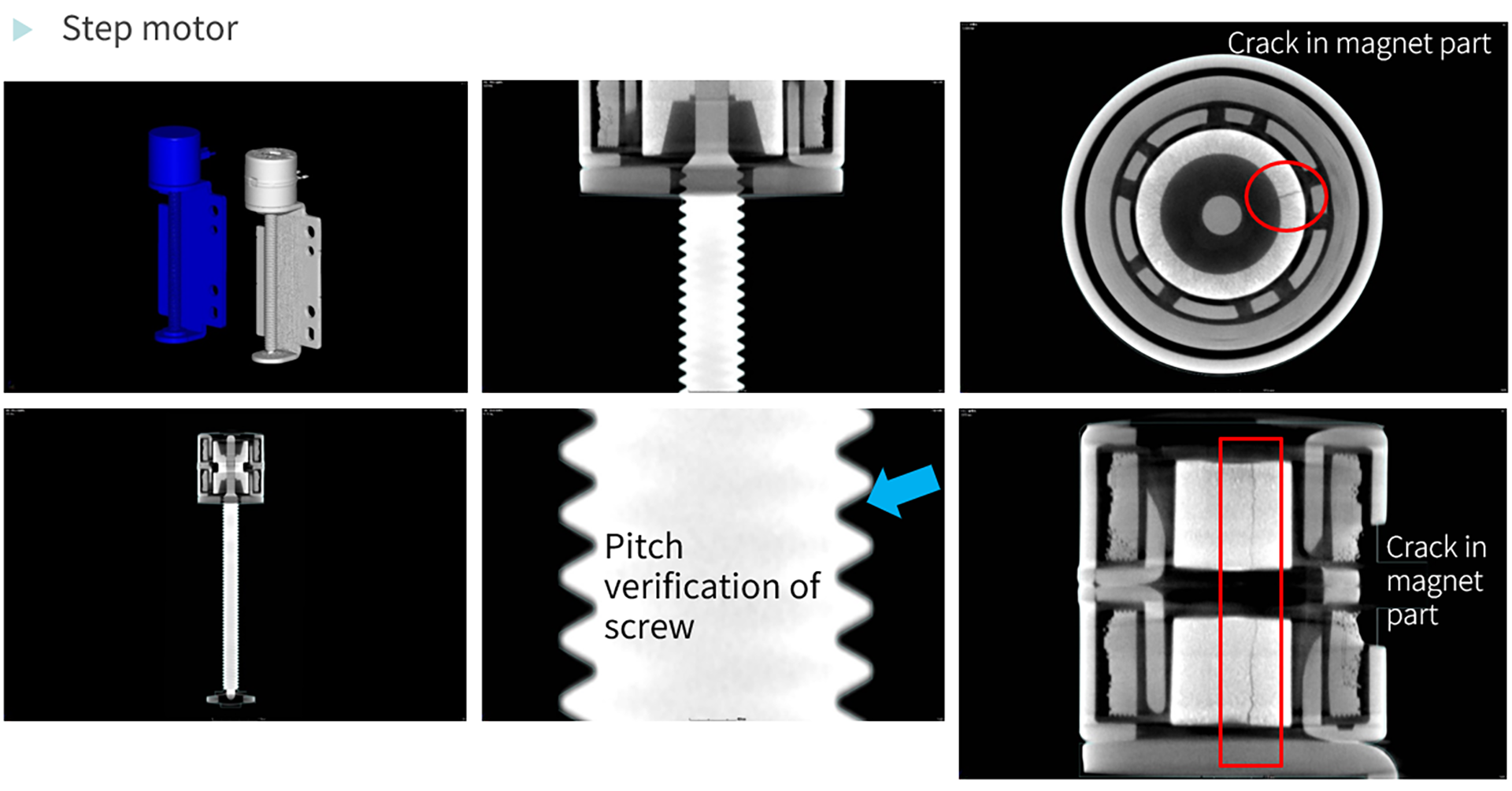
Le MCT225 marque l’étape d’une décennie
Vers 2021, la division Fabrication de Tamron a commencé à utiliser PolyWorks, un logiciel de mesure 3D, pour mesurer les produits moulés. L’année suivante, en 2022, elle a encore élargi ses capacités en exploitant la fonction de correction géométrique de VGSTUDIO MAX pour corriger les moules.
Ces outils et logiciels de pointe ont été largement utilisés dans de nombreuses divisions de l’entreprise. La division Recherche et développement, la division Conception des produits, la division de fabrication des moules et la division Assurance qualité ont toutes intégré ces technologies dans leurs processus de travail, témoignant de l’engagement de Tamron en faveur du développement technologique.
Une décennie s’est écoulée depuis que Tamron a acquis sont premier appareil MCT225, une étape qui a marqué le début d’un parcours de transformation. Cet appareil a joué un rôle essentiel dans le développement technologique de l’entreprise : Tamron l’a même intégré dans des visites guidées pour démontrer son approche innovante en matière de fabrication et de contrôle de la qualité.
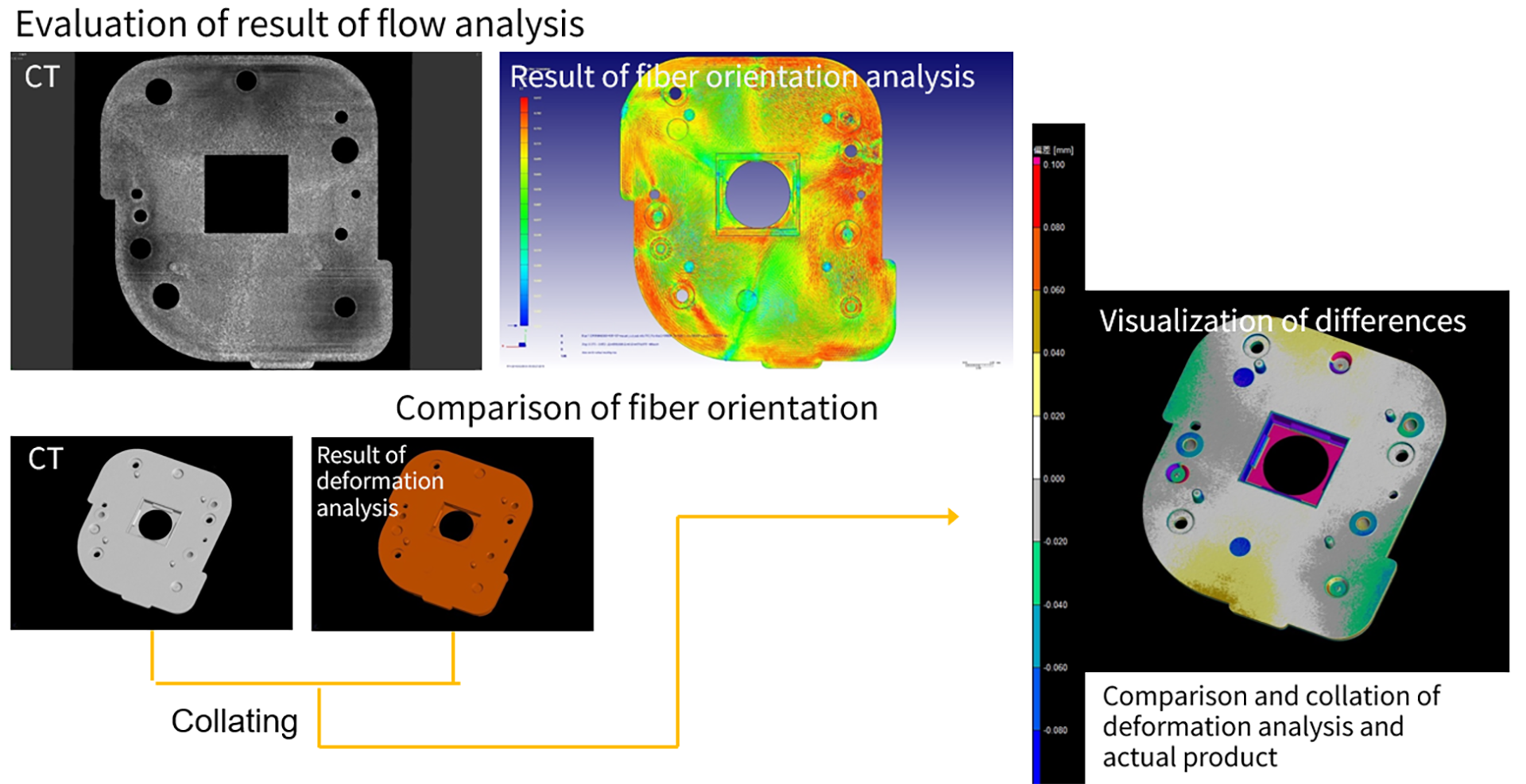
« Avant d’adopter le MCT225, nous cherchions un moyen d’évaluer en trois dimensions la déformation des pièces moulées en plastique, qui sont des composants mécaniques des unités des lentilles, d’une manière similaire à l’analyse des flux. », explique le porte-parole de Tamron. « Pour réduire le nombre de corrections à apporter aux moules, il était nécessaire d’améliorer la précision prédictive de l’analyse de l’écoulement, mais les résultats des mesures ponctuelles effectuées à l’aide d’appareils de mesure par contact et l’analyse tridimensionnelle n’étaient pas très compatibles. »
Afin d’évaluer avec précision la déformation des pièces moulées en plastique, Tamron a créé des modèles en 3D à partir des numérisations CT, puis a comparé ces modèles 3D aux résultats de la CAO et de l’analyse 3D à l’aide du logiciel VGSTUDIO MAX. Cette approche a permis d’éliminer la nécessité de mesurer plusieurs points et de les aligner avec des dispositifs de mesure par contact. Au contraire, la comparaison directe entre l’élément réel et l’analyse au niveau du modèle a considérablement augmenté l’efficacité de la vérification. De plus, comme Tamron utilise des plastiques renforcés par des fibres, l’observation de l’orientation des fibres par numérisation CT améliore la précision de l’analyse.
Tamron a aussi adopté des techniques visant à réduire les artefacts, un type de bruit en imagerie, en utilisant des filtres métalliques pendant l’acquisition.
Les technologies de Nikon s’avèrent populaires chez Tamron
« Au départ, nous avons utilisé l’équipement principalement pour le scan des unités de lentilles et des produits moulés utilisés dans la division Développement à des fins d’évaluation, mais nous avons rapidement commencé à recevoir des demandes d’autres divisions et l’utilisation au sein de l’entreprise s’est rapidement accrue », indique le porte-parole de Tamron.
En 2017, Tamron a ajouté une autre licence pour VGSTUDIO MAX ; en 2019, l’entreprise a introduit une unité PolyWorks en complément de la numérisation hélicoïdale pour être utilisée par la division Fabrication.
« En 2021, Nikon et Volume Graphics ont fourni conjointement des services de conseil pour un projet de réduction du temps de travail lié aux mesures dans la division Fabrication en utilisant la fonction macro du MCT225 et la correction de la géométrie du logiciel VGSTUDIO MAX, et pour la mise en œuvre de la CAO à l’aide des données d’imagerie de l’assemblage, en obtenant des résultats fiables dans chaque cas », explique le porte-parole de Tamron. « Cela a été un facteur décisif pour l’introduction de la seconde unité. »
La proposition de Nikon a permis à Tamron de surmonter les difficultés liées à l’évaluation des produits moulés afin d’améliorer la précision de l’analyse des flux.
Les ateliers utilisant le MCT225 forment plus de 100 employés de Tamron
Le système MCT225 est désormais largement utilisé par les divisions au sein de Tamron pour l’évaluation des assemblages et la détection des défauts dans les composants moulés. Depuis juin 2017, les ateliers utilisant le MCT225 ont formé plus de 100 employés pour en maîtriser le fonctionnement à travers les divisions.
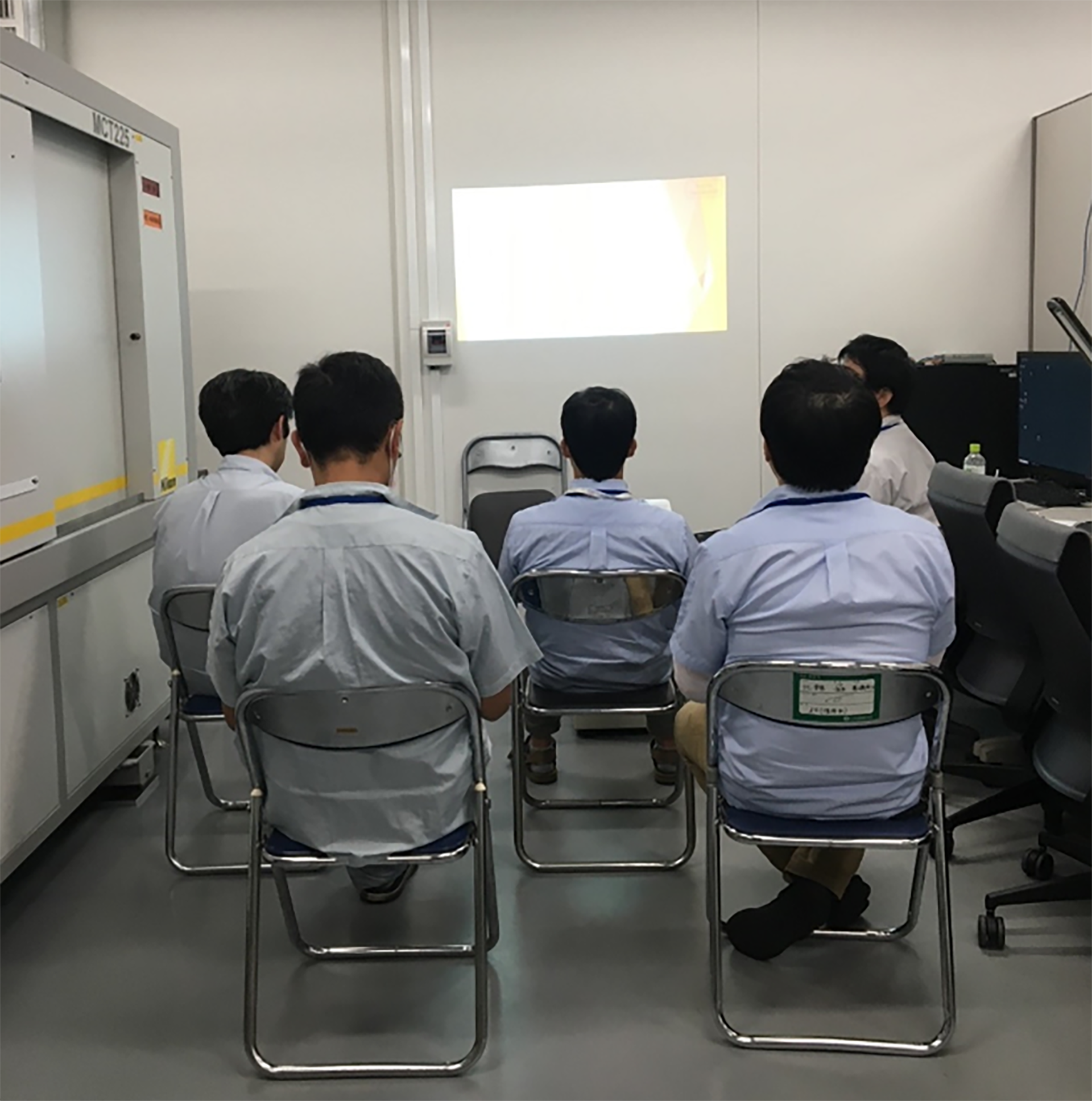
« Nos réalisations en matière d’amélioration de l’efficacité opérationnelle ont été reconnues et, en 2018, la division Recherche et développement s’est vu décerné le Prix du Président pour l’amélioration de l’efficacité opérationnelle par le développement de techniques d’utilisation de la numérisation CT. », dit le porte-parole de Tamron.
« En 2023, aussi grâce aux conseils de Nikon, nous avons obtenu une seconde fois le Prix du Président pour l’amélioration de la précision et la réduction du temps de travail grâce à l’utilisation de la numérisation CT et à la création d’un logiciel de correction automatique dans la division Fabrication. »
Si la technologie et les capacités avancées du MCT225 de Nikon ont sans aucun doute été des facteurs déterminants, la décision de Tamron d’adopter le système a également été influencée par des considérations d’ordre pratique et budgétaire.
« Par rapport à d’autres produits, le MCT225 était proposé à un prix très raisonnable pour ses performances », explique le porte-parole de Tamron. « De plus, la distance physique entre le site d’assistance et notre entreprise était proche, ce qui nous donnait également un sentiment de sécurité en termes d’organisation.
Non seulement le produit était attrayant, mais la personnalité du vendeur a également été un facteur décisif, comme l’a indiqué le chef de division de l’époque. En finalité, choisir Nikon nous a mené au succès. »
La décision de porter son choix sur le MCT225 de Nikon s’est avérée être un triomphe pour Tamron. Depuis sa mise en œuvre, le système a été largement adopté par les différentes divisions de l’entreprise et plus de 100 employés maîtrisent désormais son fonctionnement. Cette adoption généralisée souligne l’impact transformateur du MCT225 sur les flux de travail et les processus de Tamron.