LiB.Overhang Analysis from Nikon Industrial Metrology performs high-speed analysis with 3D data, powered by AI for automated inspection of lithium batteries. A breakthrough in lithium-ion cell inspection.
Combining cutting-edge AI, in-house reconstruction algorithms and advanced X-ray source technology, lithium-ion cell manufacturers can now automatically measure anode overhang with 3D CT scans, faster and more precisely than before. Significantly increased operation speeds allow closed-loop production line feedback. And with industry-standard integration, LiB.Overhang Analysis enables adjustment of production parameters in real time to maximise yield and minimise scrap.
Manufacturers can implement LiB.Overhang Analysis on a wide range of lithium-ion battery cells, including pouch, prismatic and cylindrical cells.
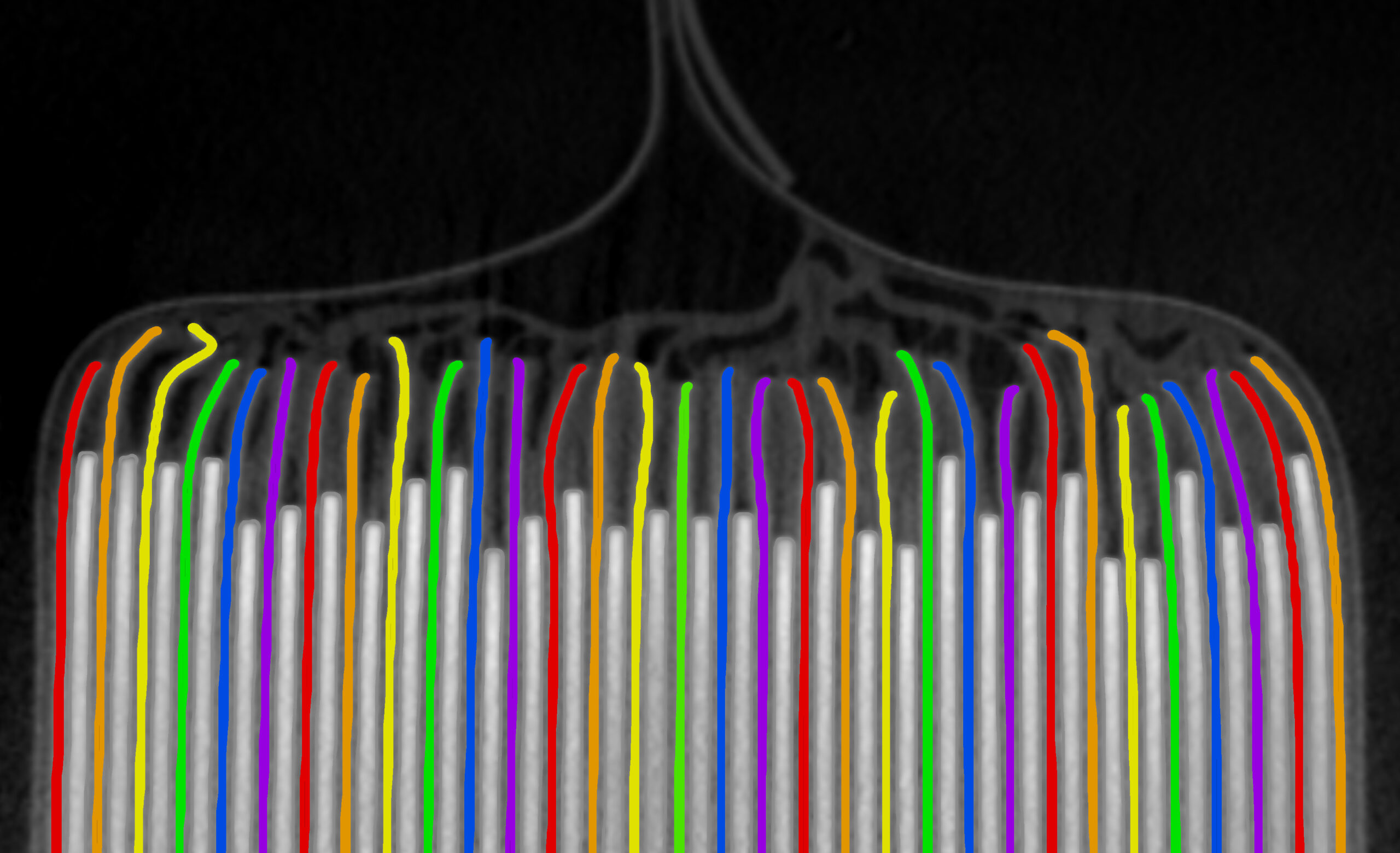
The complex process of battery manufacturing
The structure of a lithium-ion battery cell is similar in all types. Layers of cathodes, typically aluminium sheets with a lithium-based coating, alternate with anode sheets, typically copper with a carbon-based coating. Ions exchange between the cathodes and anodes, which are approximately 200 µm thick, while thin separators prevent short circuits, minimising the risk of failure.
Assembly methods
There are two principal methods of assembling these sheets. One, a traditional and well-understood manufacturing process, is to wind continuous cathode, separator and anode sheets into a cylindrical or flattened roll, commonly known as a “jellyroll”. However, this approach lowers the energy density and current capacity and the electrode structure can be prone to swelling.
The second and more recent method which battery manufacturers are adopting is to stack independent sheets on top of each other. This allows for a higher current capacity and energy density. This method is particularly beneficial for electric vehicles, where the balance of low weight and high capacity is critical for performance. However, the assembly method is more difficult because the individual layers must align precisely for effective performance and safety.
Whether wound into a roll or stacked, manufacturers must enclose the electrode sheets in packaging, such as a rigid case or a flexible pouch.
Different types of cell
Cylindrical cells comprise a roll in a round metal case and have been produced in various types for many years. Efficient production methods combined with high mechanical stability make them a safe choice for electric vehicles. But when arranged with other cells into a module or pack, the cylindrical cases do not efficiently use the space.
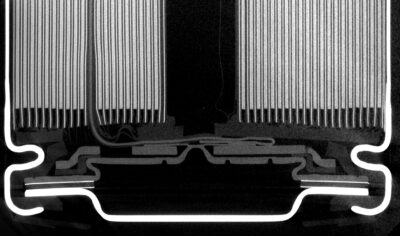
Prismatic cells enclose one or more stacked or wound cells in a rectangular case, which are tightly packed alongside other cells and retain mechanical stability.
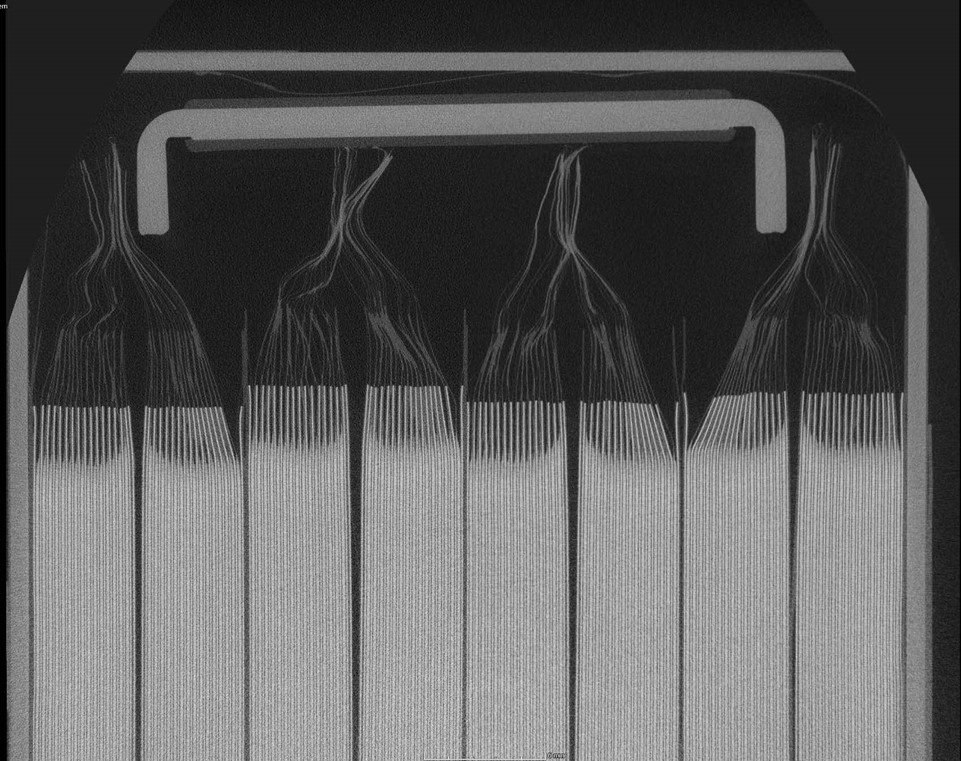
Pouch cells are most commonly associated with mobile phones but are rapidly becoming more common in electric vehicles. The thin, flexible packaging can accommodate wound or stacked electrodes and there is little wasted space when packed alongside each other. They are lighter and more economical because they do not have a solid case and therefore use less material.
Once production techniques mature and the process speeds up, pouch cells are likely to be the lowest cost manufacturing solution. However, they are the least mechanically stable, are prone to damage, and need an allowance for swelling during assembly.
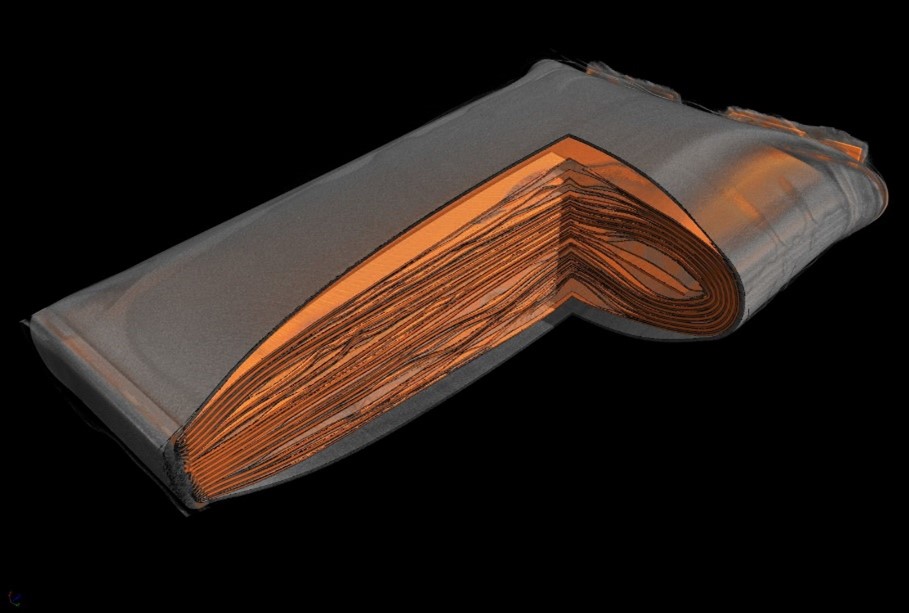
Lithium-ion battery cell inspection complexities
Lithium-ion cell manufacturing requires many steps and multiple inspections. Current manual inspection methods are complex, slow, and costly. For both quality control and R&D, an operator inspects samples at each stage of the process to check for flaws or defects. It is therefore impossible to perform thorough checks on 100% of parts in a high-throughput environment.
The most common in-line X-ray inspection on the shop floor is 2D radiography. This is fast and much better than not checking the cells at all, but it is imprecise; it cannot assess the complex three-dimensional assembly. Cathode and anode sheets which do not lie perfectly flat result in inaccurate measurements, which lead to undetected defects or unnecessary scrap.
After stacking, the anode often extends beyond the cathodes in the stack. Any inconsistency in the overhang region can lead to reduced performance or even a short circuit. Therefore, engineers need to control the relative lengths of the cathode and anode sheets precisely.
Stacking of the anodes and cathodes is one of the most important processes that battery manufacturers need to investigate and monitor, as errors can lead to offsets and unacceptable overhangs. With suitable inspection techniques, operatives can correct any variance from the nominal value before it drifts out of tolerance, limiting or perhaps even pre-empting scrap. However, to ensure successful inspection of this type, it requires full automation, precision, and speed.
These complexities have prompted battery manufacturers to explore in-line 3D inspection instead of in-line 2D radiography or manual inspection methods.
A CT scan of a cell clearly reveals the ends of the electrode sheets, however, battery manufacturers could not find a solution that is sufficiently fast and accurate to perform the necessary inspections in 3D – until now.
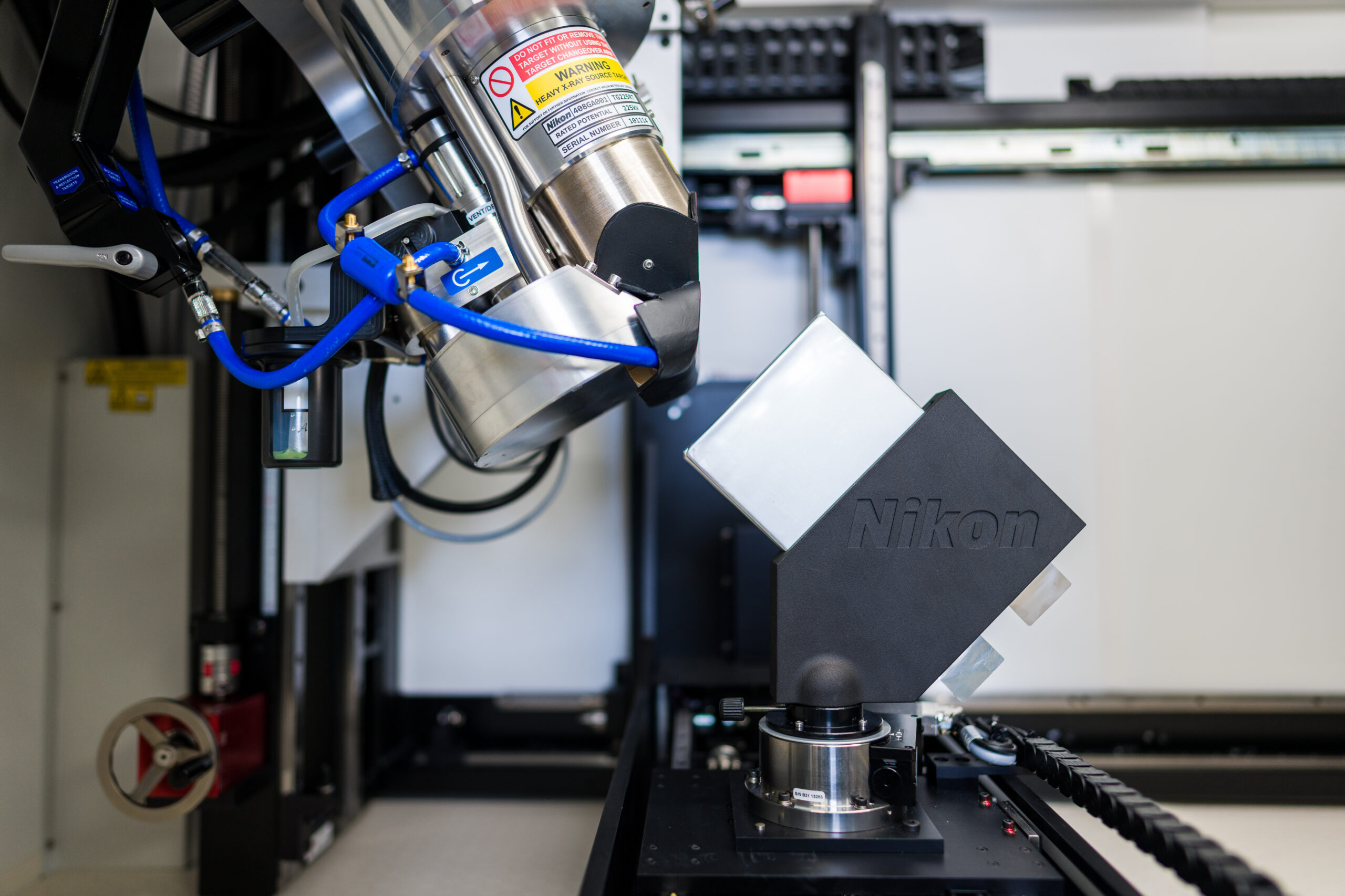
The solution; LiB.Overhang Analysis
Nikon has been listening to battery manufacturers and developing cutting-edge technology for lithium-ion battery cell inspection. We now have tools that answer the industry requests for automation, accuracy and increased inspection frequency throughout the process. Our 3D X-ray CT technology makes it easier to determine anomalies and identify at which step they occur, and is now efficient enough to work in a high-throughout production line.
LiB.Overhang Analysis process and benefits
Nikon’s experts optimise LiB.Overhang Analysis to suit each specific cell type, creating an AI model using state-of-the-art Machine Learning techniques. Configurable software then analyses the data, identifying and measuring anode overhang. This approach is extremely tolerant to scan artefacts, allowing ultra-fast CT scans to be analysed with excellent repeatability.
- Nikon Automation OPC UA Interface enables shopfloor processes to identify cells when ready, instructing the Nikon equipment to scan.
- Data processing, including rapid CT reconstruction and AI analysis, is automatic.
- The system identifies and measures the electrodes. Typical accuracy is better than ± 80 µm (3σ), depending on the cell size and type.
- Nikon Automation OPC UA Interface automatically feeds back the results for use by other production systems, enabling Statistical Process Control.
Quick scan times
Traditional X-ray CT scanning and analysis requires long scan times of approximately 30 minutes. But Nikon can scan nearly two orders of magnitude faster than conventional approaches – in just 20 seconds, depending on cell type! Thanks to Nikon’s powerful 225kV Rotating.Target 2.0 and its Half.Turn CT acquisition technology, which requires the cell to only rotate by just over 180 degrees (rather than the traditional 360 degrees), scan time is significantly reduced while retaining industry-leading image quality.
Comprehensive, integrated, and adaptable
LiB.Overhang Analysis is not an off-the-shelf product, but a flexible, comprehensive, integrated tool which is fully configurable to your needs.
- Configurable measurement approaches meet individual requirements.
- Machine-readable output enables automatic sentencing.
- Industry-standard OPC UA provides easy integration with production line processes.
- Allows cell-level traceability when combined with a Manufacturing Execution System.
- Enables Industry 4.0 practices via Statistical Process Control and closed-loop feedback.