Nikons Röntgen-Computertomographie-Technologie (CT) hat es dem Schwergewicht unter den Digitalkamera-Objektiven, Tamron, ermöglicht, einen noch nie dagewesenen Einblick in die Feinheiten seiner branchenführenden Komponenten zu gewinnen.
Das japanische Unternehmen Tamron stand vor der Herausforderung, die Verformung von aus Kunststoff geformten Objektivkomponenten genau zu analysieren. Nikons MCT225-Gerät löste dieses Problem, indem es dem Unternehmen ermöglichte, 3D-Modelle aus CT-Scans zu erstellen, die direkt mit CAD-Modellen und Analyseergebnissen mit der VGSTUDIO MAX Software verglichen werden können.
Dies brachte eine Reihe von Vorteilen mit sich: Die Notwendigkeit, mehrere Messpunkte auszurichten, entfiel und die Beobachtung der Faserorientierung in den faserverstärkten Kunststoffen von Tamron wurde möglich – eine entscheidende Entwicklung, die die Analysegenauigkeit verbesserte.
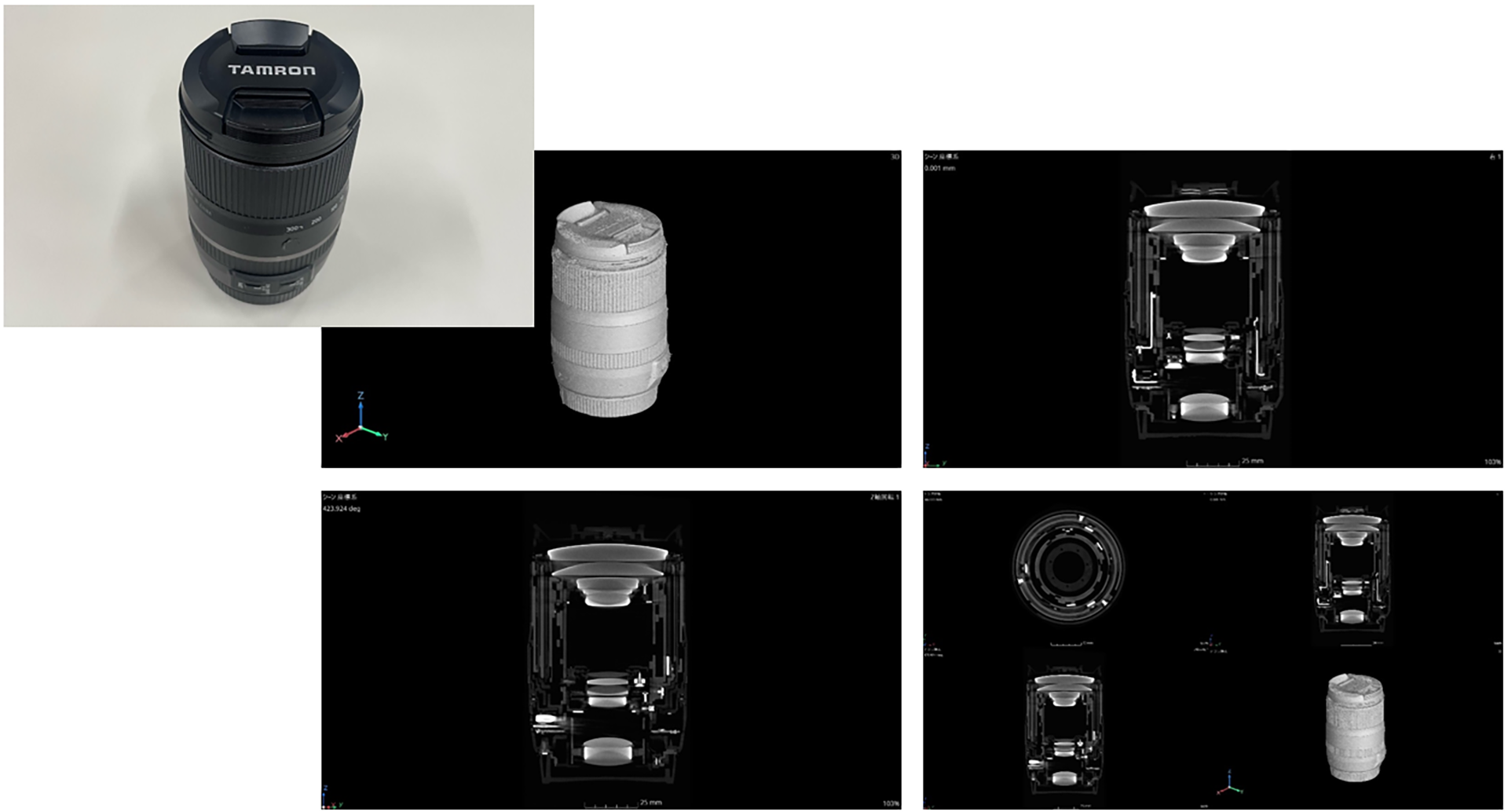
Tamron hat seinen Hauptsitz in Saitama City und arbeitet kontinuierlich an der Entwicklung fortschrittlicher optischer Technologien, wobei Kreativität und technische Stärke kombiniert werden, um qualitativ hochwertige Produkte zu entwickeln und anzubieten, auf die sich Benutzer weltweit verlassen können.
Tamron blickt auf eine Geschichte von über sieben Jahrzehnten zurück. Das Unternehmen wurde 1950 unter dem Namen Taisei Optical Equipment Manufacturing gegründet und bot zunächst Technologie zum Polieren von Linsen für Kameras und Ferngläser an.
Mit zunehmender Erfahrung wagte sich Tamron an die Herstellung von Wechselobjektiven für Spiegelreflexkameras. Im Jahr 1958 wurde das Markenzeichen eingetragen und 1970 änderte das Unternehmen offiziell seinen Namen in Tamron.
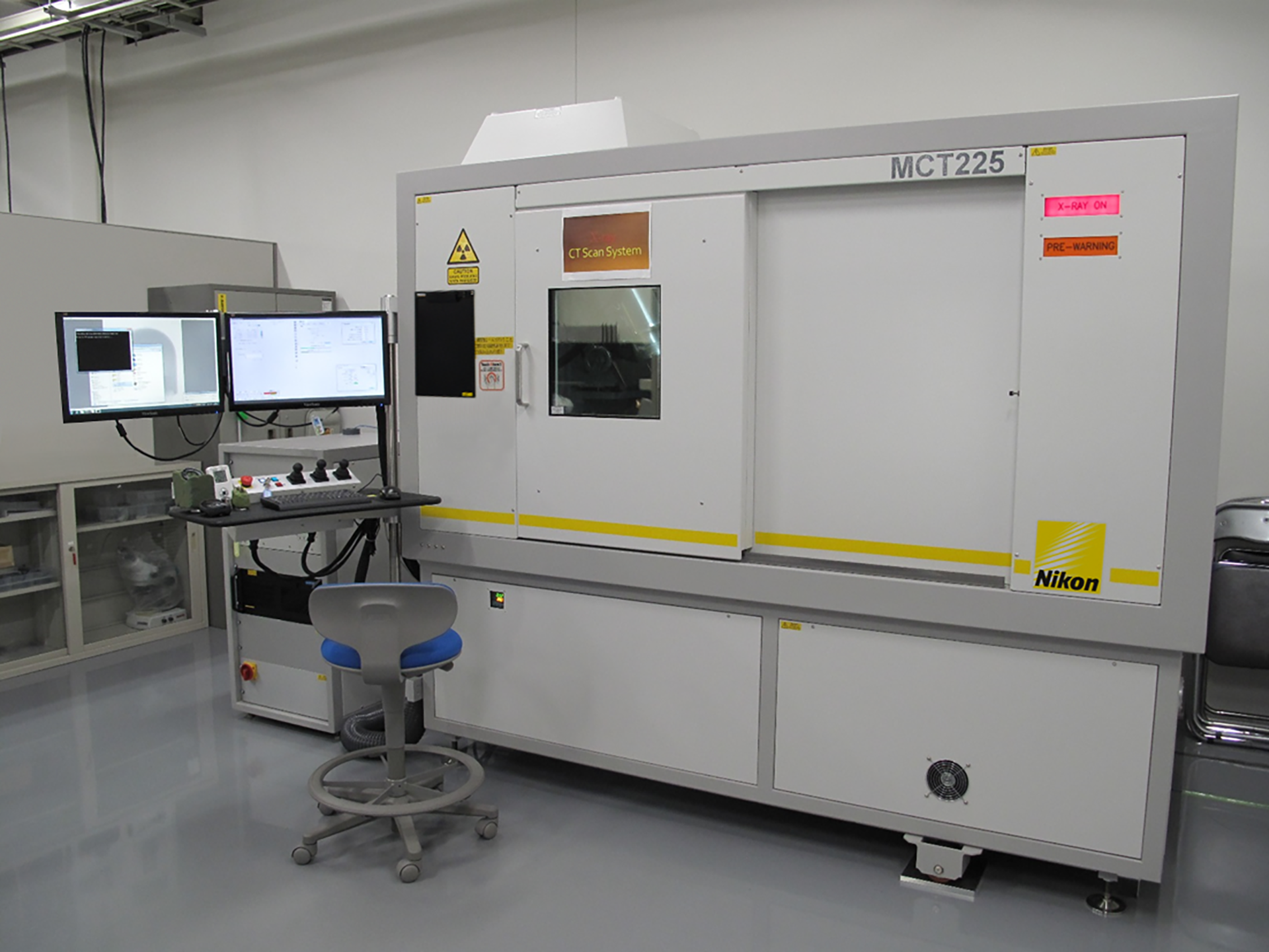
Im Laufe der Jahre hat sich Tamron zu einem umfassenden Hersteller optischer Geräte entwickelt, der über eine weltweit integrierte Geschäftsstruktur verfügt, die Forschung und Entwicklung, Planung, Design, Produktion, Vertrieb und Support umfasst. Die Produktpalette erweiterte sich um Marken-Wechselobjektive für digitale Spiegelreflexkameras für den allgemeinen Verbraucher, OEM-Produkte und optische Komponenten für verschiedene Industriebereiche.
Das MCT225 bietet Einblicke in die Qualität des Endprodukts
Im April 2014 übernahm Tamron das Röntgen-CT-Messsystem MCT225 von Nikon, zusammen mit zwei überholten Computern. Diese anfängliche Einrichtung ermöglichte es Tamron, die Qualität von Kunststoffformteilen und kritischen mechanischen Komponenten ihrer Objektiveinheiten abzubilden und zu bewerten. Tamron konnte die Qualität des fertigen Produkts beurteilen, indem es die Design-Spezifikationen mit den tatsächlichen Messungen verglich, die durch die CT-Bildgebung mit der VGSTUDIO MAX Software gewonnen wurden.
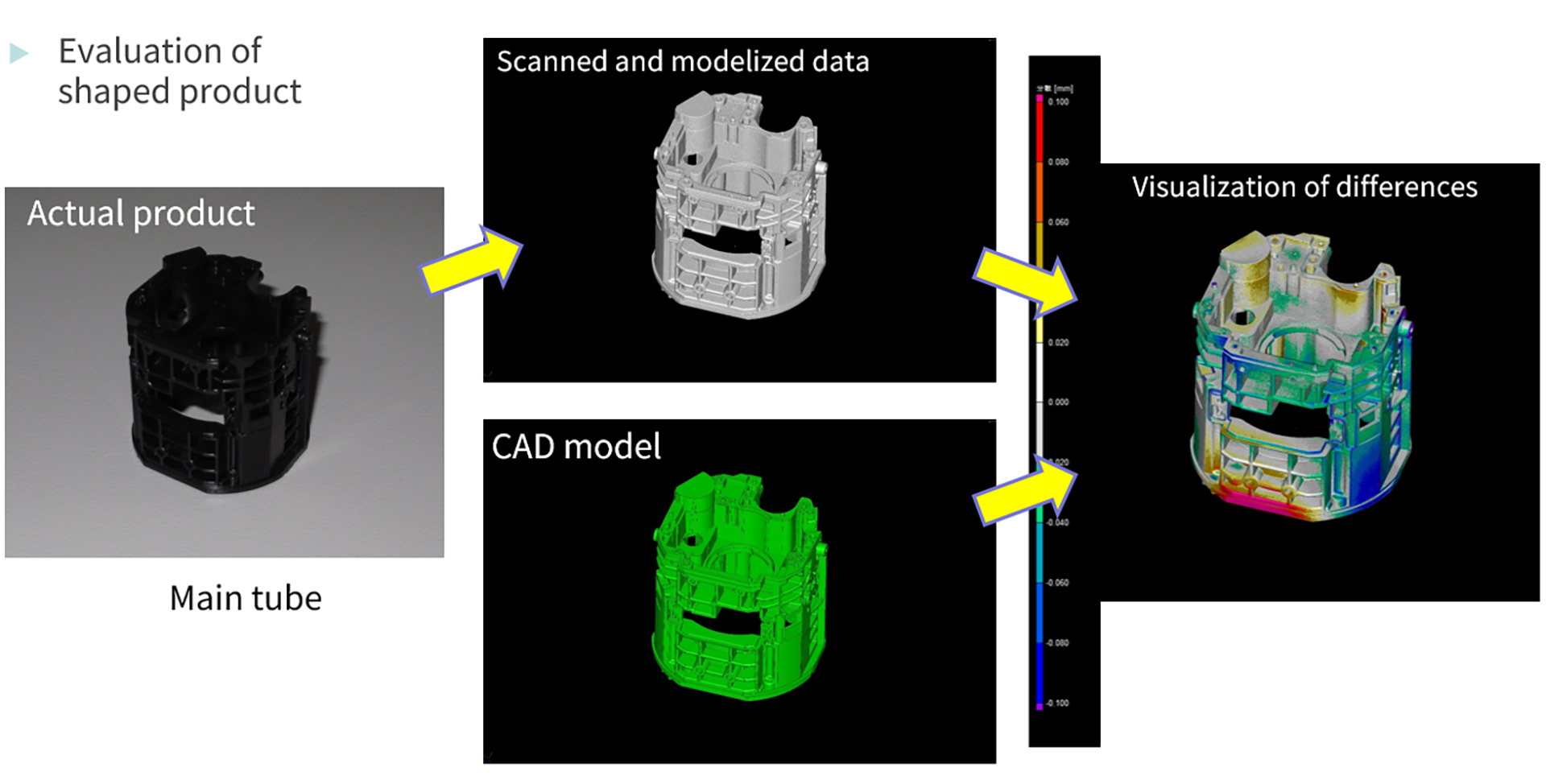
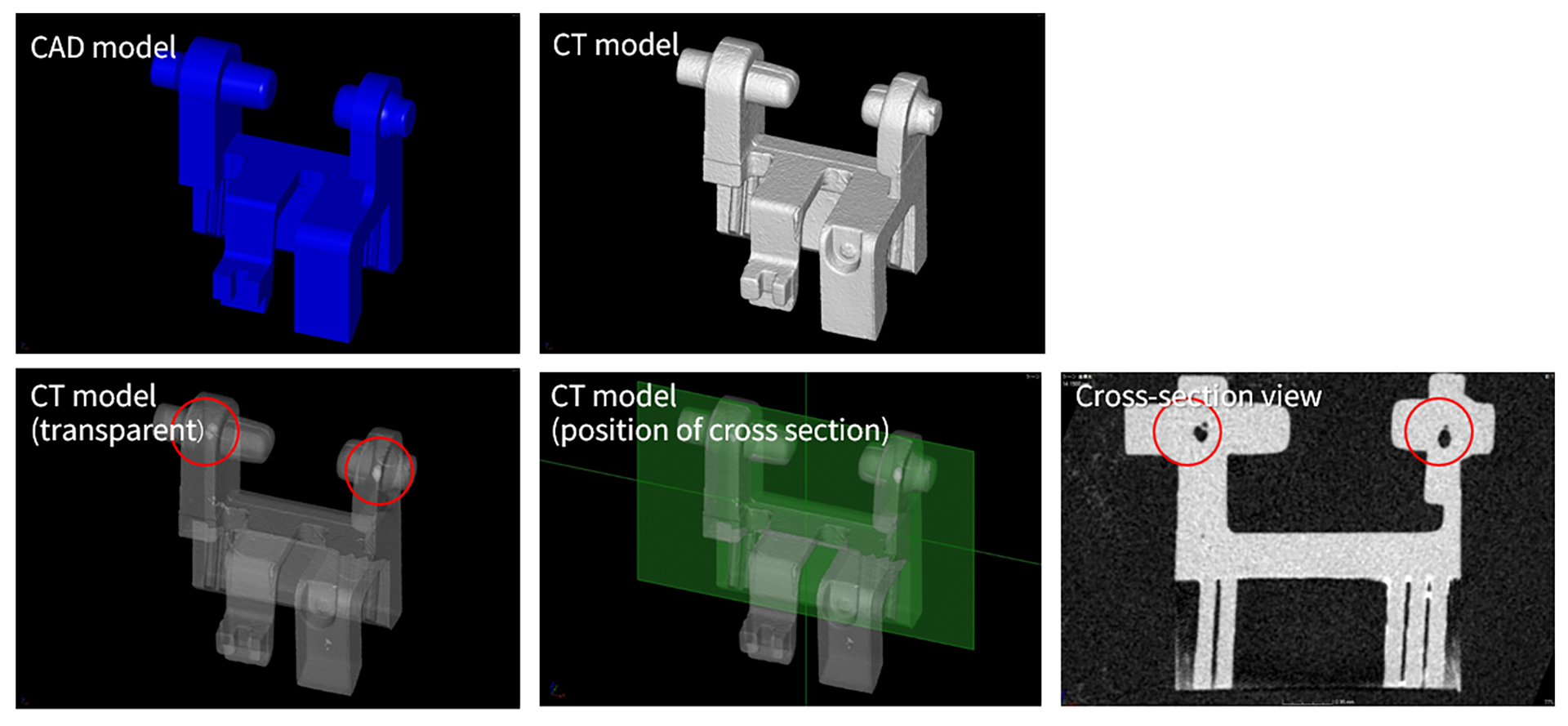
Im Laufe der Zeit erwies sich das MCT225-System als unschätzbar wertvoll, so dass Tamron im Oktober 2023 seine Kapazitäten um eine zweite MCT225-Einheit und einen zusätzlichen überholten Computer erweiterte.
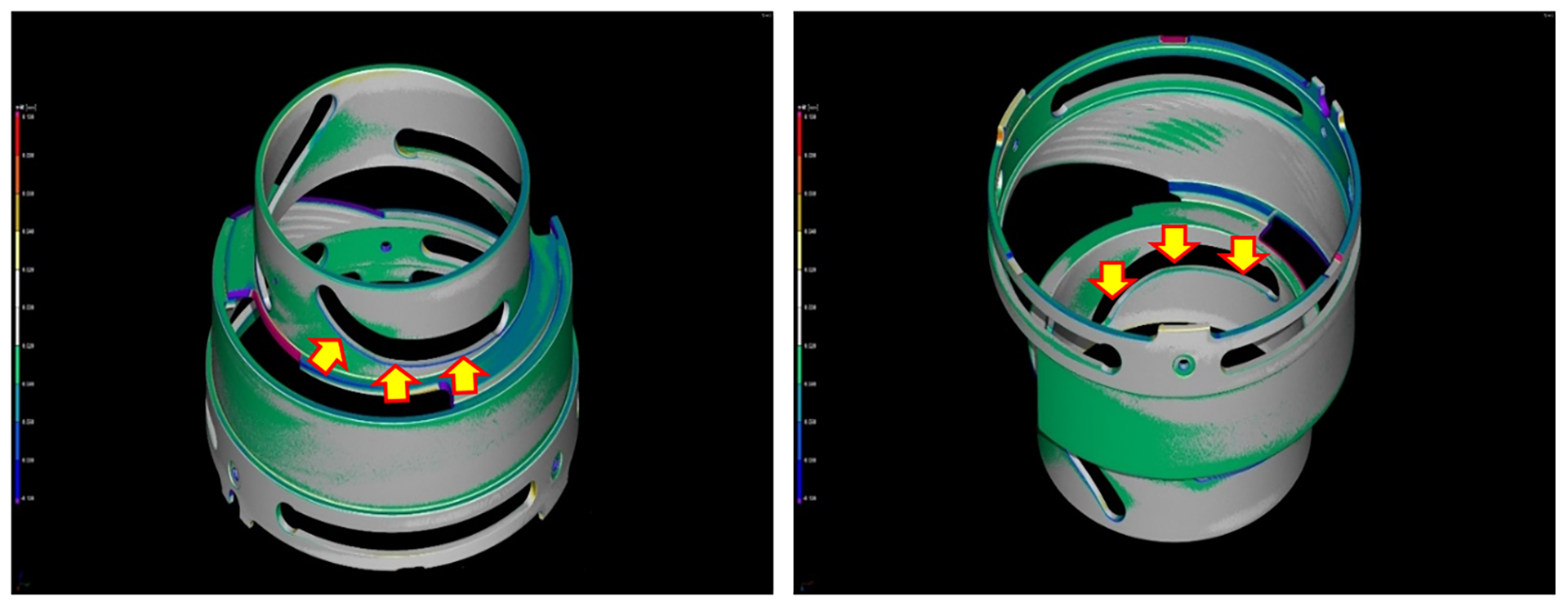
Die aus diesen Auswertungen gewonnenen Erkenntnisse wurden dann in die Ergebnisse der Flussanalyse zurückgeführt, so dass Tamron die Genauigkeit seiner Analyseprozesse kontinuierlich verbessern konnte. Neben der Bewertung der Qualität des Endprodukts erleichterten die MCT225-Systeme auch die Beurteilung der Variabilität von geformten Produkten, die Erkennung von Hohlräumen und Rissen, die Beobachtung der Faserorientierung in verstärkten Kunststoffen, die Untersuchung von Defekten in Montagezuständen, die Analyse von Konkurrenzprodukten und die Untersuchung von Defekten in elektronischen Substraten.
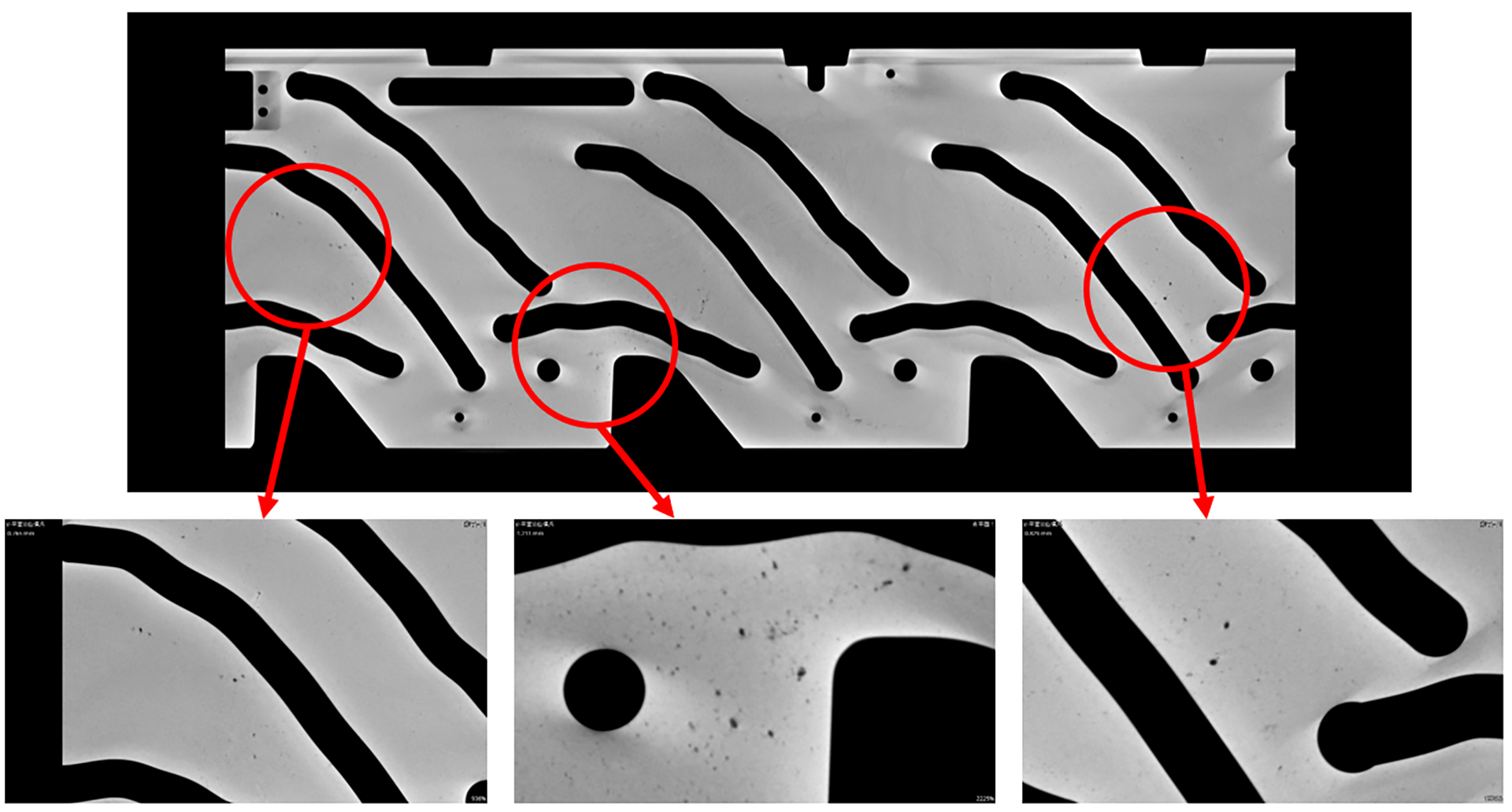
„Wir finden sowohl das Gerät als auch die Software des MCT225 sehr benutzerfreundlich“, sagt der Sprecher von Tamron. „Die Reaktion auf unsere Hilfe bei der regelmäßigen Wartung oder Fehlerbehebung war immer schnell. Ich fühle mich auch dadurch beruhigt, dass ich die Möglichkeit habe, den Messraum von Nikon zu mieten, wenn das Gerät für eine bestimmte Zeit nicht benutzt werden kann, z. B. während der Wartung oder bei einem dringenden Problem.“
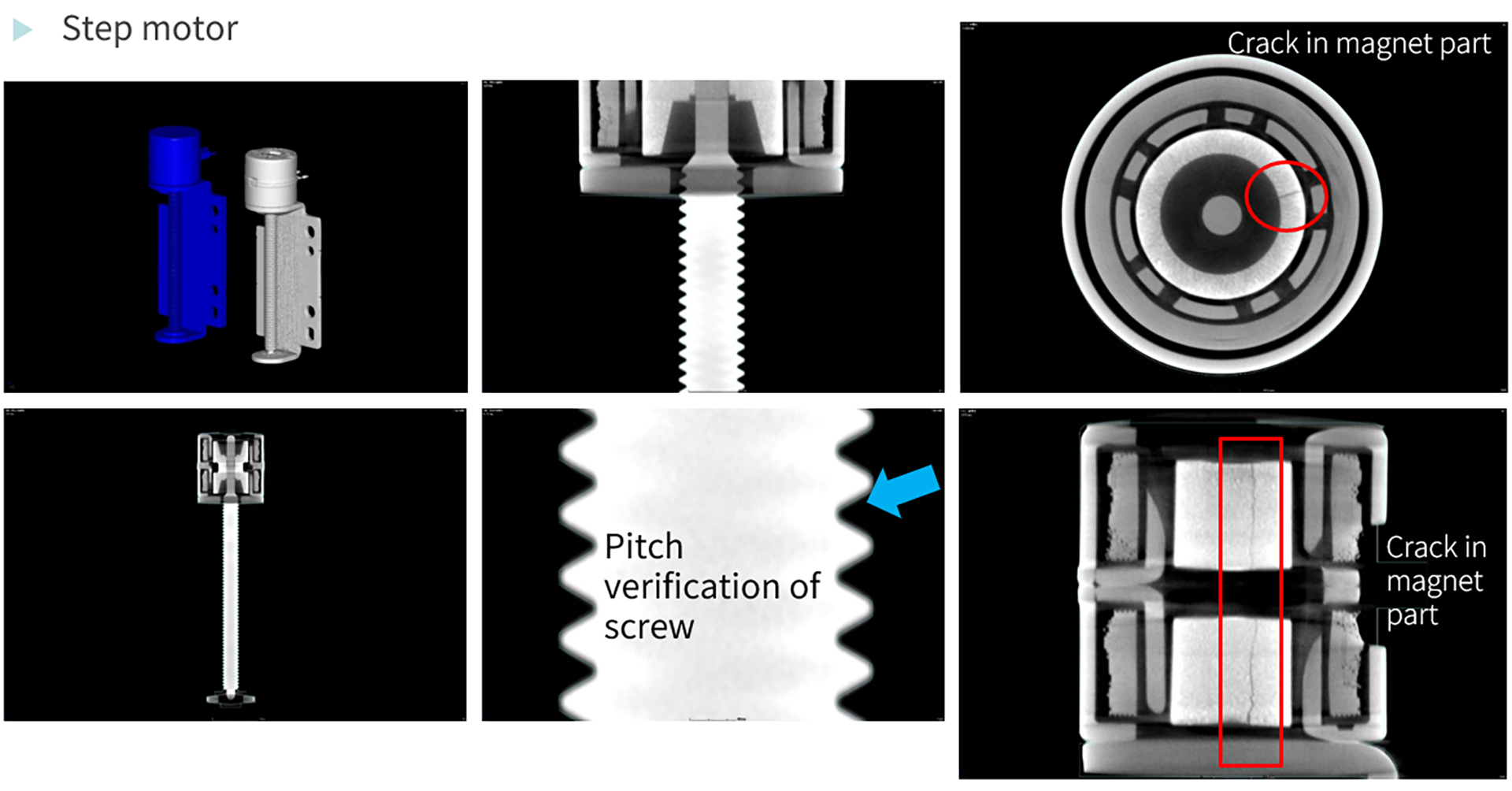
Das MCT225 markiert den Meilenstein eines Jahrzehnts
Um das Jahr 2021 begann die Fertigungsabteilung von Tamron mit der Nutzung von PolyWorks, einer 3D-Messsoftware, um geformte Produkte zu vermessen. Im darauf folgenden Jahr, 2022, haben sie ihre Möglichkeiten weiter ausgebaut, indem sie die Geometriekorrekturfunktion von VGSTUDIO MAX zur Korrektur von Formen nutzten.
Diese hochmodernen Tools und Software finden in vielen Abteilungen des Unternehmens Anwendung. Die Abteilung für Forschung und Entwicklung, die Abteilung für Produktdesign, die Abteilung für Formenbau und die Abteilung für Qualitätssicherung haben diese Technologien in ihre Arbeitsabläufe integriert – ein Beweis für Tamrons Engagement in der technologischen Entwicklung.
Es ist ein Jahrzehnt her, dass Tamron sein erstes MCT225-Gerät erworben hat, ein Meilenstein, der den Beginn einer transformativen Reise markiert. Dieses Gerät hat eine entscheidende Rolle bei der technologischen Entwicklung des Unternehmens gespielt – Tamron hat es sogar in die Besuchertouren integriert, um seinen innovativen Ansatz bei der Herstellung und Qualitätskontrolle zu demonstrieren.
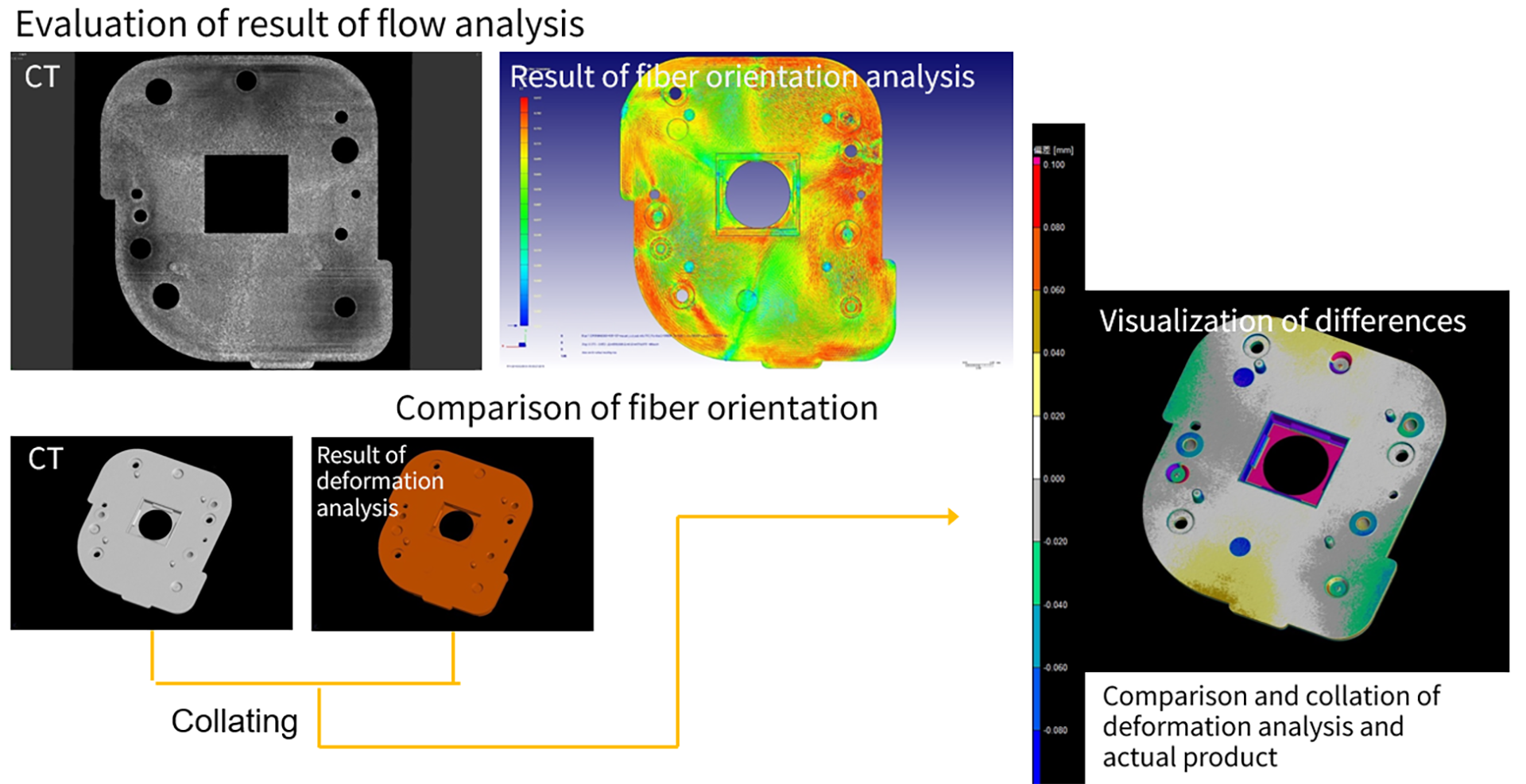
„Bevor wir das MCT225 einsetzten, suchten wir nach einer Möglichkeit, die Verformung von Kunststoffformteilen, die mechanische Komponenten von Objektiven sind, ähnlich wie bei der Strömungsanalyse dreidimensional zu bewerten“, erklärt der Sprecher von Tamron. „Um die Anzahl der Korrekturen an den Formen zu reduzieren, war es notwendig, die Vorhersagegenauigkeit der Strömungsanalyse zu verbessern, aber die Ergebnisse von Punktmessungen mit Kontaktmessgeräten und dreidimensionaler Analyse waren nicht sehr kompatibel.“
Um die Verformung von Kunststoffformteilen genau zu beurteilen, hat Tamron 3D-Modelle durch CT-Scans erstellt. Sie verglichen diese 3D-Modelle mit CAD- und 3D-Analyseergebnissen mit der Software VGSTUDIO MAX. Mit diesem Ansatz entfällt die Notwendigkeit, mehrere Punkte zu messen und mit Kontaktmessgeräten auszurichten. Stattdessen hat der direkte Vergleich zwischen dem tatsächlichen Artikel und der Analyse auf Modellebene die Effizienz der Überprüfung drastisch erhöht. Da Tamron füllstoffverstärkte Kunststoffe verwendet, erhöht die Beobachtung der Faserorientierung durch CT-Scans die Genauigkeit der Analyse.
Tamron hat auch Techniken zur Reduzierung von Artefakten, einer Art Bildrauschen, eingeführt, indem Metallfilter während der Aufnahme verwendet werden.
Nikons Technologien sind bei Tamron beliebt
„Anfänglich haben wir das Gerät hauptsächlich für die Aufnahme von Objektiven und geformten Produkten in der Entwicklungsabteilung zu Evaluierungszwecken verwendet, aber schon bald erhielten wir Anfragen aus anderen Abteilungen, und die Nutzung innerhalb des Unternehmens nahm schnell zu“, sagt der Sprecher von Tamron.
Im Jahr 2017 fügte Tamron eine weitere Lizenz für VGSTUDIO MAX hinzu. 2019 führte das Unternehmen ein PolyWorks-Gerät für das Helical Scanning und den Einsatz in der Manufacturing Division ein.
„Im Jahr 2021 haben Nikon und Volume Graphics gemeinsam ein Projekt zur Reduzierung der Arbeitsstunden für Messungen in der Fertigungsabteilung unter Verwendung der MCT225-Makrofunktion und der Geometriekorrektur von VGSTUDIO MAX sowie für die CAE-Implementierung unter Verwendung von Bilddaten aus der Baugruppe beratend unterstützt und dabei jeweils bestimmte Ergebnisse erzielt“, erklärt der Sprecher von Tamron. „Das war ein wichtiger Entscheidungsfaktor für die Einführung der zweiten Einheit.“
Nikons Vorschlag ermöglichte es Tamron, die Herausforderungen bei der Bewertung von geformten Produkten zu überwinden und die Genauigkeit der Fließanalyse zu verbessern.
MCT225-Workshops schulen über 100 Tamron-Mitarbeiter
Das MCT225-System wird heute von vielen Abteilungen innerhalb von Tamron für die Bewertung von Baugruppen und die Erkennung von Fehlern in gegossenen Komponenten eingesetzt. Seit Juni 2017 wurden in den MCT225-Workshops mehr als 100 Mitarbeiter aus allen Abteilungen in der Bedienung des Systems geschult.
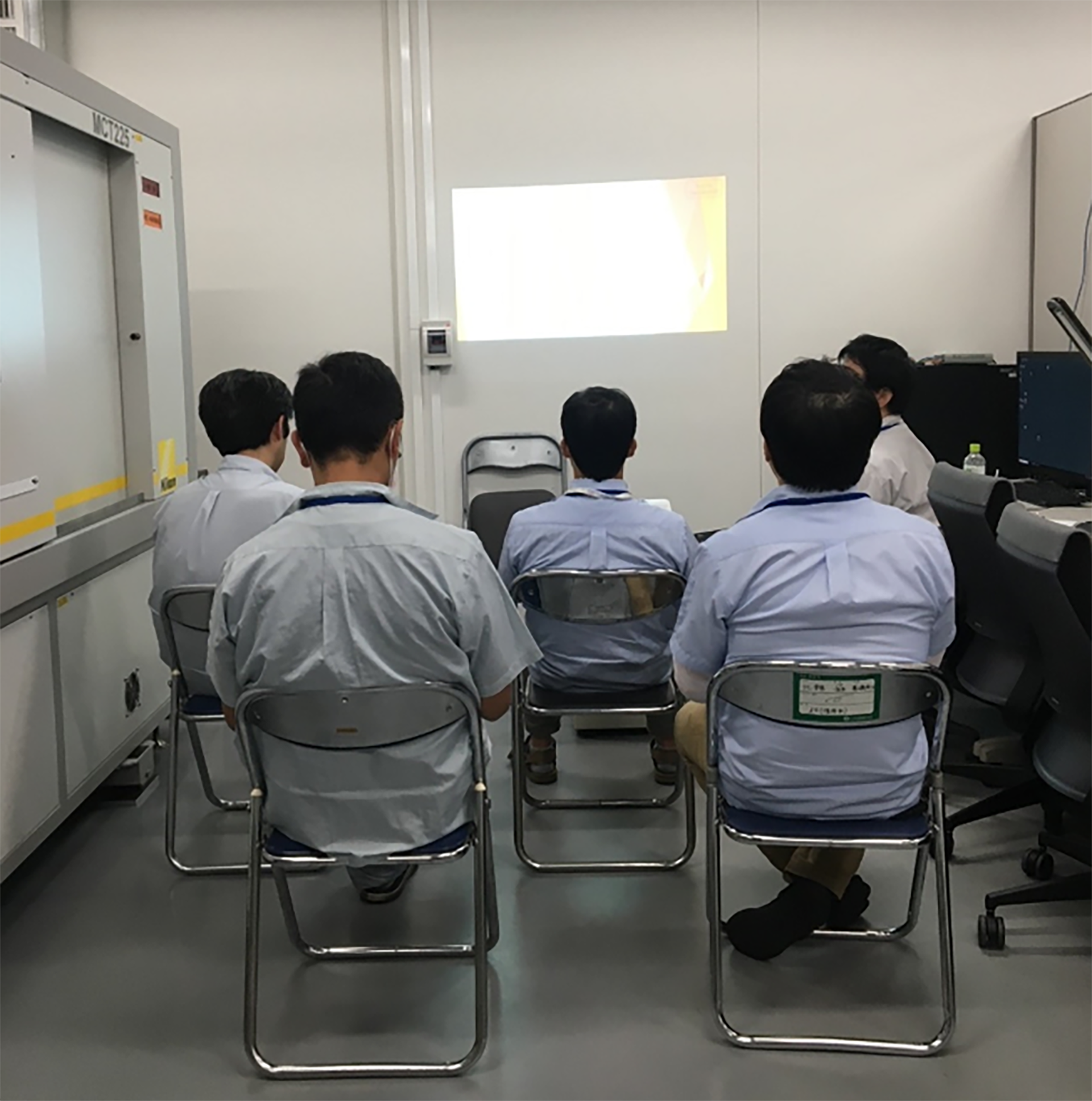
„Unsere Leistungen bei der Verbesserung der Betriebseffizienz wurden anerkannt. 2018 erhielt die Forschungs- und Entwicklungsabteilung den President’s Award für die Verbesserung der Betriebseffizienz durch die Entwicklung von Techniken zur Nutzung von CT-Scannern“, so der Sprecher von Tamron.
„Im Jahr 2023 erhielten wir, auch dank der Beratung durch Nikon, zum zweiten Mal den President’s Award für die Verbesserung der Genauigkeit und die Reduzierung der Arbeitsstunden durch die Nutzung von CT und die Erstellung einer automatischen Korrektursoftware in der Fertigungsabteilung.“
Obwohl die fortschrittliche Technologie und die Fähigkeiten des MCT225 von Nikon zweifellos überzeugende Faktoren waren, wurde die Entscheidung von Tamron, das System zu übernehmen, auch von praktischen und budgetären Überlegungen beeinflusst.
„Im Vergleich zu anderen Produkten war der MCT225 für seine Leistung sehr angemessen im Preis“, erklärt der Tamron-Sprecher. „Außerdem war die räumliche Entfernung zum Support-Standort von unserem Unternehmen gering, was uns auch in organisatorischer Hinsicht ein Gefühl der Sicherheit gab.
„Nicht nur das Produkt war ansprechend, sondern auch die Persönlichkeit des Vertriebsmitarbeiters war ein entscheidender Faktor, wie der damalige Abteilungsleiter sagte. Letztendlich hat die Entscheidung für Nikon zum Erfolg geführt.“
Die Entscheidung für das MCT225 von Nikon hat sich für Tamron als Triumph erwiesen. Seit seiner Einführung wurde das System in den verschiedenen Abteilungen des Unternehmens in großem Umfang angenommen, so dass inzwischen über 100 Mitarbeiter mit dem System vertraut sind. Diese weit verbreitete Akzeptanz unterstreicht den transformativen Einfluss, den das MCT225 auf die Arbeitsabläufe und Prozesse von Tamron hat.