เพื่อช่วยในการควบคุมคุณภาพของบริษัทผู้ผลิตซิลิคอนเวเฟอร์ให้เป็นไปอย่างมีคุณภาพ หน่วยธุรกิจ Industrial Metrology (มาตรวิทยาอุตสาหกรรม) ของ Nikon Corporation (https://industry.nikon.com) จึงได้นำเสนอโซลูชันที่มีความแม่นยำสูงเพื่อให้สามารถตรวจสอบรหัส ID ของเวเฟอร์ได้อย่างรวดเร็วและครบถ้วน หลังจากที่มีการสลักด้วยเลเซอร์ลงบนพื้นผิวของเวเฟอร์ เทคโนโลยีนี้จะใช้ระบบการวัดด้วยวิดีโอแบบคอนโฟคอล NEXIV VMZ-K3040 ร่วมกับมุมมองแบบ 2 มิติ และ 3 มิติ สำหรับการวัดประเมินตัวอักษรที่ใช้ระบุเวเฟอร์ในแต่ละแผ่น
NEXIV จะเชื่อมต่อเข้ากับตัวโหลดเวเฟอร์อัตโนมัติซึ่งจะส่งเวเฟอร์เซมิคอนดักเตอร์จาก FOUP (front opening unified pod) ไปยังระบบการวัดด้วยวิดีโอและส่งคืนกลับมาในภายหลัง
โดยไม่ต้องจัดการด้วยตนเอง เพื่อหลีกเลี่ยงความสิ้นเปลืองจากข้อผิดพลาดที่มีค่าใช้จ่ายสูง ความสามารถในการอ่านรหัสที่ระบุ (ID) เวเฟอร์ได้อย่างน่าเชื่อถือ จากขั้นตอนการประมวลผลหลายร้อยครั้ง ขั้นตอนใน FAB จึงมีความสำคัญต่อความสำเร็จโดยรวมของการดำเนินงาน เครื่องมืออ่าน OCR (optical character recognition) ของ SEMI (Semiconductor Equipment and Materials International) ในทุกตำแหน่งการทำงานต้องสามารถตรวจจับตัวอักษรพิเศษในรหัสซีเรียลได้โดยไม่มีข้อผิดพลาด เพื่อให้แน่ใจว่าเวเฟอร์ดังกล่าวเป็นเวเฟอร์ที่ถูกต้อง อย่างไรก็ตาม รอยเลเซอร์จะค่อย ๆ เลือนรางลงเมื่อมีการดำเนินการต่อไปและจะทำให้เครื่องอ่าน OCR จำแนกตัวอักษรได้ยากขึ้นและมองไม่เห็นความแตกต่างมากขึ้นเรื่อย ๆ โซลูชันของ Nikon จะช่วยให้แน่ใจได้ว่ารอยเลเซอร์บนเวเฟอร์เปล่านั้น จะมีระดับความลึกและขนาดที่เหมาะสมเสมอ เพื่อให้หมายเลขซีเรียล (ตัวอักษร OCR และข้อมูลเมทริกซ์ SEMI T7) สามารถอ่านได้เสมอ
แม้ว่าจะเป็นช่วงหลังของการดำเนินการและการจัดส่งก็ตาม การประเมินคุณภาพของการสลัก ID ด้วยเลเซอร์นั้น จะต้องดำเนินการทันทีหลังจากที่มีการสลักเวเฟอร์ การดำเนินการตรวจสอบด้วยวิดีโออัตโนมัติที่ดำเนินการโดย NEXIV คอนโฟคอล จะมอบผลลัพธ์ที่น่าประหลาดใจในแง่ของความครอบคลุมและความแม่นยำ เนื่องจากความสามารถส่วนหนึ่งของระบบการวัดด้วยวิดีโอนั้น จะสามารถเก็บบันทึกตำแหน่งที่ถูกต้องตามจริงของทุกคุณลักษณะ ในขณะเดียวกัน ปริมาณงานที่สูงของขั้นตอนการทำงานแบบอัตโนมัตินั้นมีความสม่ำเสมอ พร้อมทั้งการบูรณาการเข้ากับการทำงานในสายการผลิตของโรงงานได้อย่างราบรื่น ความเร็วสูงในการปฏิบัติงานจะทำให้สามารถตรวจสอบข้อมูลการเสื่อมสภาพที่บ่งชี้ถึงคุณภาพแบบเรียลไทม์ได้อย่างทันท่วงที เพื่อให้สามารถบำรุงรักษาเครื่องมือสลักด้วยเลเซอร์ได้ในเวลาที่เหมาะสม
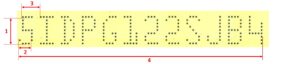
เลขที่ |
จุดวัด | ระบบออปติกที่ใช้ |
จุดที่ระบุ |
เส้นผ่านศูนย์กลางจุดตัวอักษร |
ไบรท์ฟิลด์ |
1 |
ความสูงของตัวอักษร | |
2 |
ความกว้างของตัวอักษร | |
3 |
ระยะห่างของตัวอักษร |
|
4 |
ความยาวทั้งบรรทัด |
|
จุดที่ระบุ | ความลึกของจุด |
คอนโฟคอล |
ลำดับการวิเคราะห์และการรายงานของ Nikon สำหรับตัวอักษร OCR เริ่มต้นด้วยการใช้คาลิเปอร์วงกลมกับระบบออปติก 2 มิติ แบบไบรท์ฟิลด์เพื่อวัดการสลักด้วยเลเซอร์และคำนวณเส้นผ่านศูนย์กลางและพิกัดของการสลักที่จุดศูนย์กลาง จากนั้นจะเป็นการวัดความสูง ความกว้าง ระยะห่าง และความยาวทั้งหมดของบรรทัด และใช้ระบบออปติก 3 มิติ แบบคอนโฟคอลเพื่อหาความลึกของการสลักด้วยเลเซอร์ ในกรณีของข้อมูล SEMI T7 Matrix จะดำเนินการตามขั้นตอนที่คล้ายกัน ข้อดีของระบบการวัดด้วยวิดีโอแบบคอนโฟคอล NEXIV VMZ-K3040 ก็คือความสามารถในการสลับระหว่างโหมดไบรท์ฟิลด์กับโหมดคอนโฟคอลได้ในโปรแกรมวิเคราะห์เพียงโปรแกรมเดียว ซึ่งต่างจากระบบอื่น ๆ ในตลาดที่ต้องใช้สองเครื่องแยกกันสำหรับแต่ละโหมด ประโยชน์ที่ได้คือมีความแม่นยำที่เหนือกว่า เร็วกว่า และเป็นกระบวนการตรวจสอบที่ราบรื่น
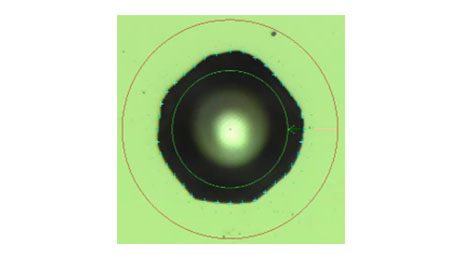
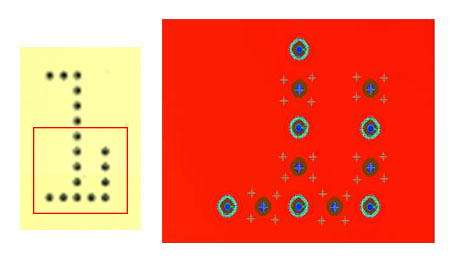
Goh Wei Chen ผู้จัดการฝ่ายโซลูชันบูรณาการ (Integrated Solutions) ของ Nikon ในสิงคโปร์ได้ให้ความเห็นไว้ว่า “โซลูชันการควบคุมคุณภาพที่เราได้พัฒนาขึ้นมาสำหรับอุตสาหกรรมการผลิตเซมิคอนดักเตอร์นี้ ได้รับการพิสูจน์แล้วว่าประสบความสำเร็จในธุรกิจบริษัทรับจ้างผลิตทั่วโลก ความแม่นยำและปริมาณงานระดับสูงที่บรรลุผลได้นั้น กำลังพิสูจน์ให้เห็นถึงจุดแข็งในด้านข้อเสนอการขายที่น่าสนใจสำหรับระบบการควบคุมคุณภาพที่สำคัญนี้” แอปพลิเคชันการวัดรหัส ID ของเวเฟอร์เองก็เป็นอีกตัวอย่างหนึ่งของจุดมุ่งหมายที่ Nikon ต้องการเพิ่มความแพร่หลายของการใช้ระบบตรวจสอบแบบเรียลไทม์ในการผลิตเชิงอุตสาหกรรม ด้วยฟีดแบคแบบอัตโนมัติที่ส่งไปยังจุดควบคุมสายงาน ทำให้การทำงานของหน่วยมาตรวิทยาสามารถขับเคลื่อนกระบวนการผลิตได้ แนวทางนี้ซึ่งเรียกว่า Quality 4.0 จะช่วยสร้างความมั่นใจได้ว่าผลิตภัณฑ์ทุกตัวที่ปลายทางของสายการผลิตจะเป็นผลิตภัณฑ์ที่ดี แทนที่จะใช้การวัดเพียงเพื่อตัดสินว่าชิ้นส่วนนั้นผ่านหรือไม่ผ่านการตรวจสอบ และต้องทำลายชิ้นส่วนนั้นทิ้งหรือไม่ สามารถดูรายละเอียดเพิ่มเติมได้ที่นี่