Nikon Corporation(https://industry.nikon.com)의 산업 계측 사업부에서는 실리콘 웨이퍼 제조 기업의 품질 관리를 지원하기 위해 고도로 정확한 솔루션을 제공하여 웨이퍼 표면에 레이저로 각인한 후 웨이퍼 ID 코드를 신속하고 종합적으로 검사합니다. 이 시스템은 이중 2D 및 3D 광학 장치와 함께 당사의 NEXIV VMZ-K3040 공초점 화상 측정 시스템을 사용하여 각 웨이퍼를 식별하는 문자의 문자열을 측정하는 것을 기반으로 합니다.
NEXIV는 사람이 직접 처리할 필요 없이 반도체 웨이퍼를 FOUP(front opening unified pod)에서 화상 측정 시스템으로 안정적으로 이송한 후 반환하는 자동 웨이퍼 로더와 연결되어 있습니다.
비용이 많이 드는 오류와 폐기물을 방지하기 위해서는 FAB에 존재하는 수백 가지 처리 단계에서 웨이퍼 식별(ID) 코드를 안정적으로 읽을 수 있는 능력이 이 작업의 전반적인 성공에 매우 중요합니다. 따라서 모든 스테이션의 SEMI(Semiconductor Equipment and Materials International) OCR(optical character recognition) 판독기는 한 치의 오차도 없이 일련번호에 있는 고유 문자를 정확하게 감지하여 올바른 웨이퍼인지 확인할 수 있어야 합니다.
하지만, 공정이 진행되면서 레이저 마크가 서서히 마모되어 점점 더 희미해지므로 OCR 판독기가 구분하기가 어려워집니다. Nikon의 솔루션은 베어 웨이퍼에 있는 레이저 마크가 항상 최적의 깊이와 치수를 가질 수 있도록 보장함으로써 가공 및 출하 후에도 항상 일련번호(OCR 문자 및 SEMI T7 매트릭스 데이터)를 읽을 수 있게 합니다. 레이저 ID 마크의 품질 평가는 웨이퍼가 각인된 직후에 바로 수행됩니다. 공초점 NEXIV에 의해 수행되는 화상 검사 자동화 루틴은 놀라울 정도로 광범위하고 정확하며 이는 모든 대상의 실제 위치를 포착할 수 있는 화상 측정 시스템의 능력 덕분입니다. 이와 동시에 자동화된 이 절차의 높은 처리량은 공장 현장에서 원활하게 통합됩니다. 이러한 고속 작업은 마킹 품질 악화에 대한 실시간 정보를 즉시 공유하는 것을 가능하게 하므로 레이저 마킹 도구를 적시에 유지보수할 수 있습니다.
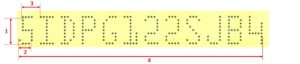
없음 |
측정 포인트 | 광학 장치 사용 |
지정된 도트 |
문자 도트 직경 |
명시야 |
1 |
문자 높이 | |
2 |
문자 너비 | |
3 |
문자 간격 |
|
4 |
전체 라인 길이 |
|
지정된 도트 | 도트 깊이 |
공초점 |
OCR 문자에 대한 니콘의 검사 및 보고 순서는 명시야 2D 광학 장치를 갖춘 원형 캘리퍼의 사용으로 시작되어 레이저 마크를 측정하고 그 직경과 중심 좌표를 계산합니다. 그런 다음, 문자의 높이, 너비, 간격 및 전체 라인 길이를 측정합니다. 공초점 3D 광학 장치를 사용하여 레이저 마크의 깊이를 확인합니다. SEMI T7 매트릭스 데이터의 경우, 유사한 절차를 따릅니다. NEXIV VMZ-K3040 공초점 화상 측정 시스템의 장점은 각 모드에 대해 두 대의 별도 기계를 사용하는 시중의 다른 시스템과 달리 단일 검사 프로그램 내에서 명시야 모드와 공초점 모드 간 전환이 가능하다는 것입니다. 이 덕분에 정확성이 우수하며, 속도가 더 빠르고, 검사 프로세스가 원활하게 진행됩니다.
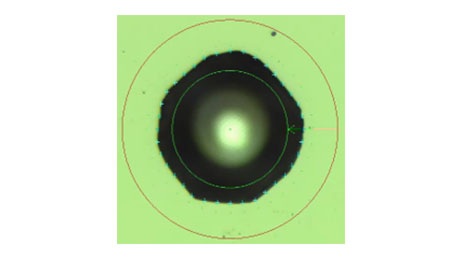
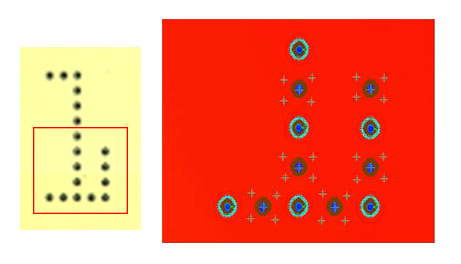
싱가포르 니콘 센터의 통합 솔루션 관리자인 Goh Wei Chen은 “반도체 제조 산업을 위해 우리가 개발해 온 이 품질 관리 솔루션은 이미 전 세계 파운드리에서 성공적인 것으로 입증되었습니다. 이렇게 중요한 품질 관리 기능에 대해 그동안 달성한 높은 정확도와 처리량은 설득력 있는 영업 제안이 되리라는 것을 증명하고 있습니다.”라고 말했습니다. 웨이퍼 ID 코드 측정 응용 분야는 계측 기능이 제조 공정을 주도하게 할 수 있도록 라인 제어에 자동 피드백을 갖추어 산업 생산에서 실시간 검사의 보급률을 높이겠다는 니콘의 목표를 보여주는 또 다른 예입니다. Quality 4.0이라고 알려진 이 접근 방식은 단순히 부품이 합격인지, 실패인지, 폐기해야 하는지 여부를 결정하는 데 측정을 사용하는 것이 아니라 생산 라인의 마무리 단계에서 모든 제품의 우수한 품질을 보장합니다. 보다 자세한 내용은 여기에서 확인할 수 있습니다.