This scan of the month features a titanium DfAM heat exchanger from Katholieke Universiteit Leuven (KU Leuven) which is currently being investigated by the additive manufacturing research group of KU Leuven. The scan was performed by Lauren Enghien (Applications engineering manager X-ray & CT). X-ray CT enables non-destructive visualization of the inner structures and defects of metal additively manufactured parts and to simulate the behavior of the parts before being installed.
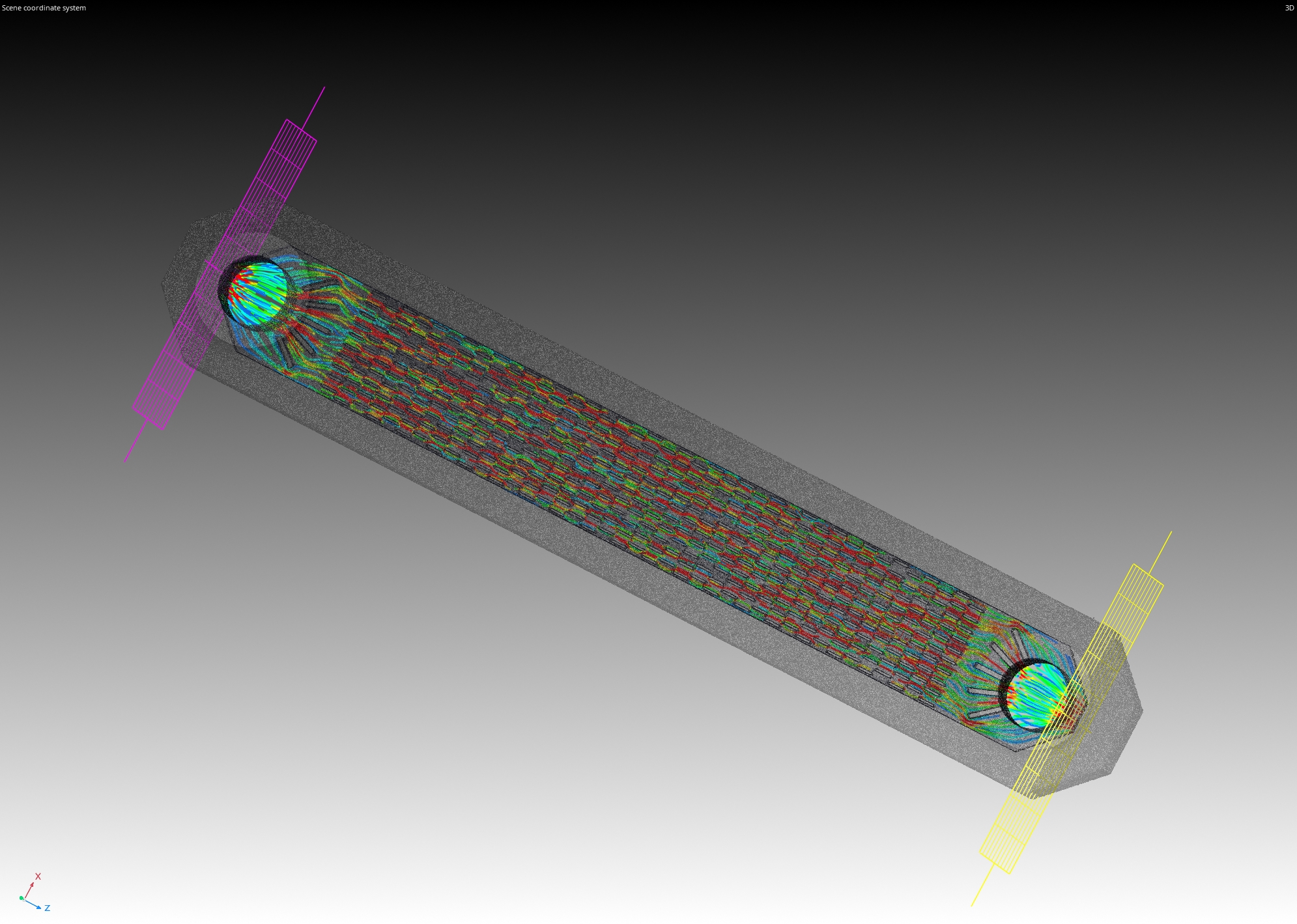
Figure 1: absolute permeability (flow direction) analysis performed in VG Studio Max 3.5.1
The scanned object is part of ongoing research on the performance of additively manufactured compact heat exchangers (cHEX) at the AM team at KU Leuven. The scanned cHEX is built with Ti64 using Laser Powder Bed Fusion (LPBF) techniques and has overall dimensions of 26×92 mm². Inside, a channel is outfitted with a periodically structured, compact offset-strip fin design with wall thicknesses reaching as small as 250 µm. This research aims at better understanding the influencing factors during LPBF on cHEX-performance by visualizing the flowfield through µPIV measurements, as well as by improving simulation strategies for periodically structured heat exchangers.
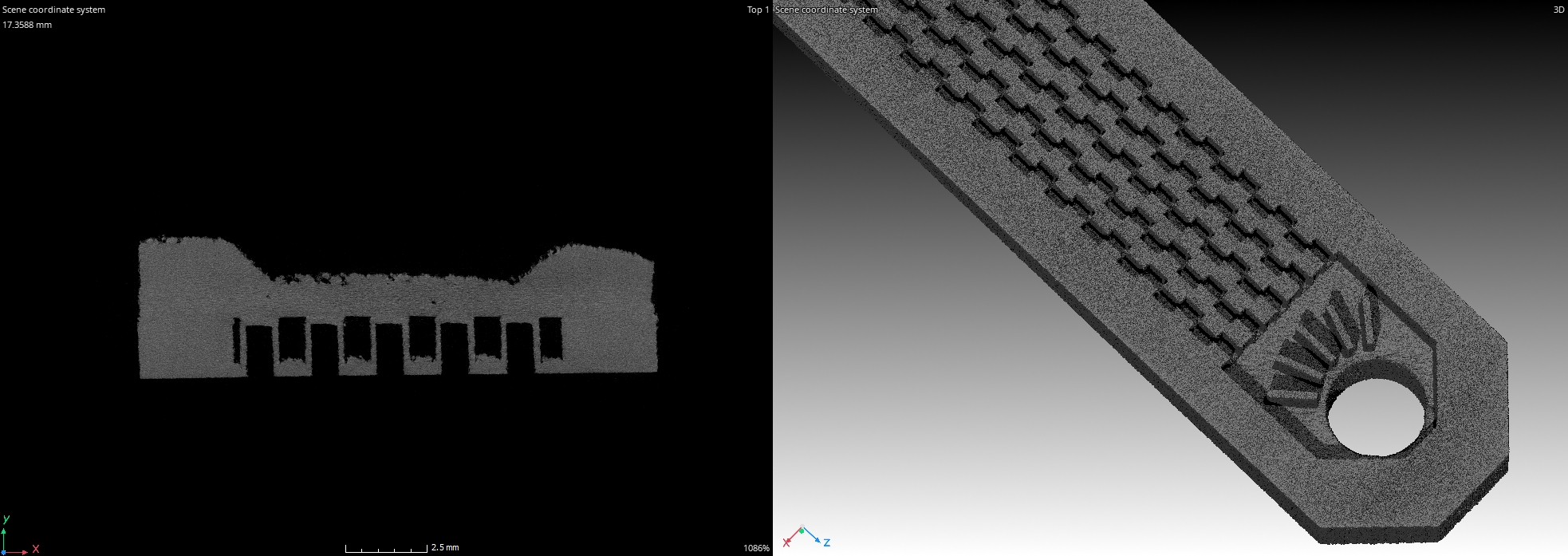
Figure 2: Section view and close-up 3D rendering of the heat exchanger
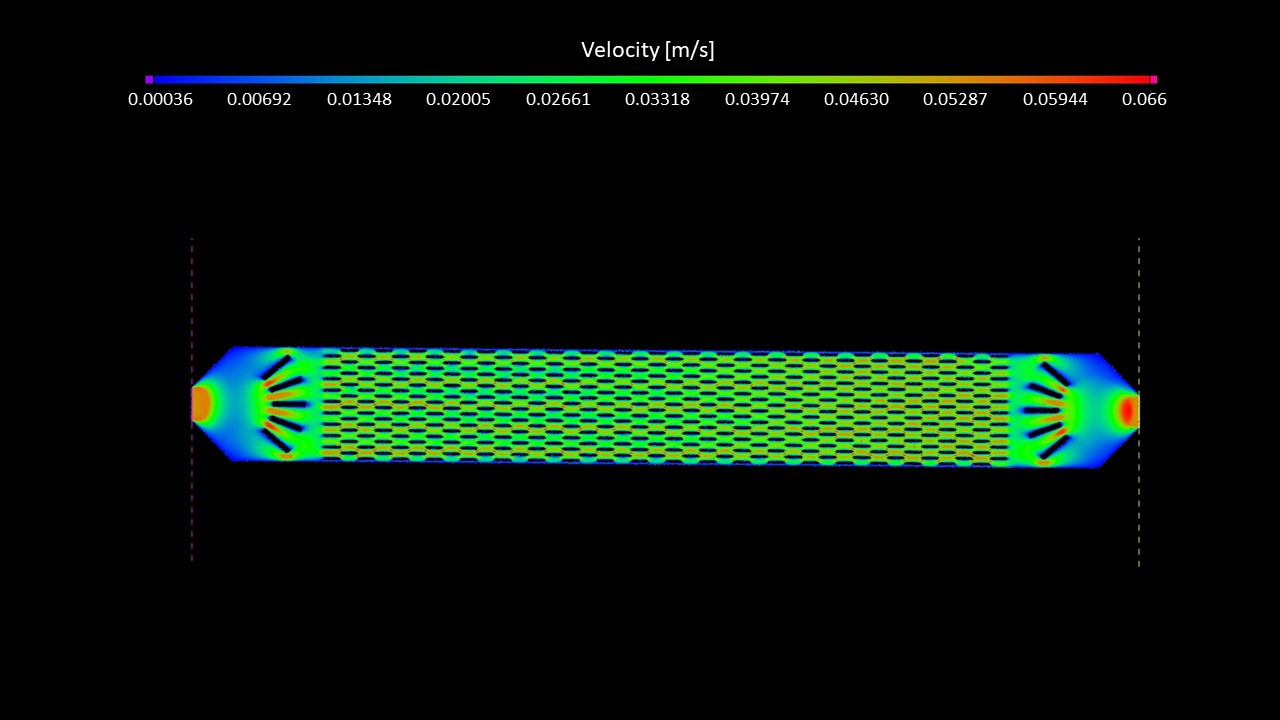
Figure 3: CFD Analysis on the heat exchanger
This X-ray CT scan was acquired using Nikon’s helical acquisition algorithm (X.tend) at a combined X-ray power of 9 Watts and a voxel resolution of 7 µm, using a Nikon XTH 225 ST 2.X. This system comes equipped with up to three different Nikon microfocus X-ray sources: a 180 kV, 20 W transmission target, a 225 kV, 225 W reflection target and a 225 kV, 450 W Rotating.Target 2.0. While the Rotating target offers unique advantages for higher power applications at high resolution, this scan was performed using the 225 kV reflection target option coupled with a Varex XRD 4343CT flat panel detector. For this scan the detector acquired 14184 projections (individual radiographs) at an exposure time of 1415 ms, resulting in a total scan time of ~5 hours and 30 minutes because of the resolution and the material (which is quite a long scan compared to the speed of our X-ray CT scans that can be as low as 1 minute).
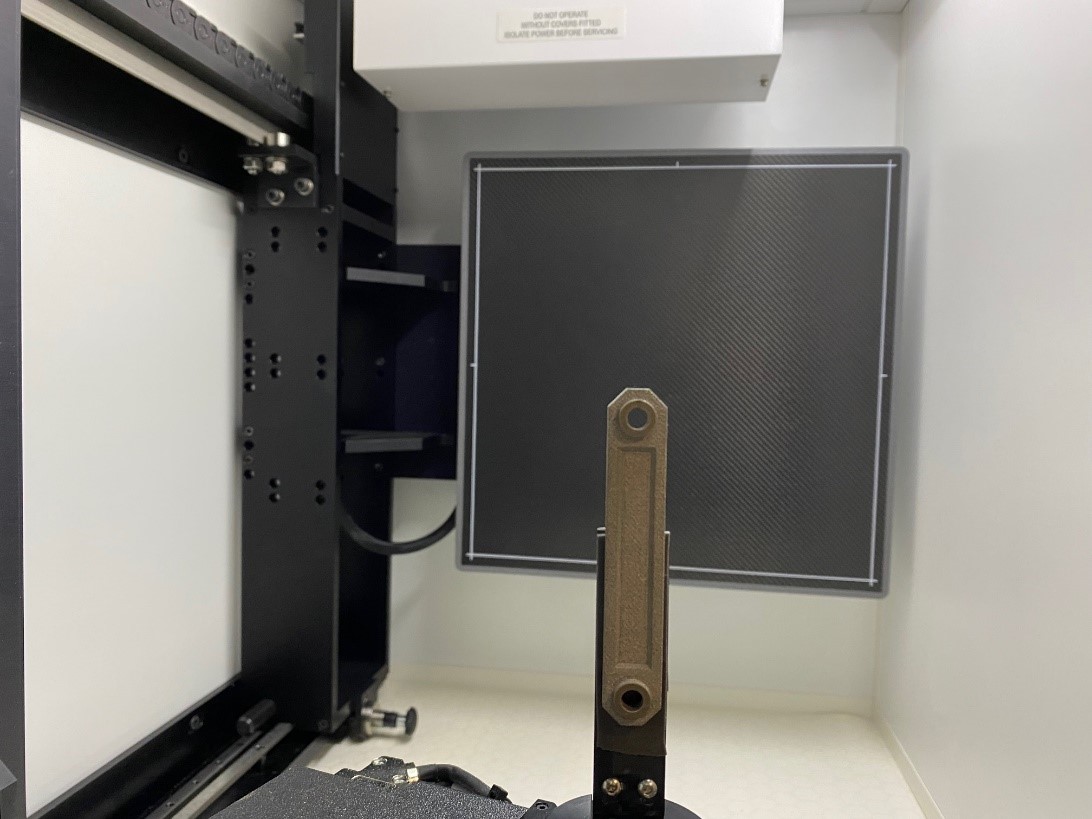
Figure 4: Scan setup
X-ray CT data was reconstructed using an exact helical reconstruction algorithm in Nikon CT Pro 3D and rendered in Volume Graphics Studio Max 3.5.1. The 3D images shown are composed of multiple volumes from the same scan and after applying different inspections. These inspections consisted out of two defect analyses able to find pores (Figure 6) and inclusions/foreign materials (Figure 5) down to 14 µm in diameter. Afterwards, an absolute permeability analysis (Figure 1 and 3) was performed on the cHEX to simulate the flow-field within the object. The high resolution of this scan in combination with the possibility to perform CFD simulation on the obtained render could provide new data of flow-fields inside LPBFed cHEX. Therefore, this technique could be valuable for KU Leuven’s future research that aims at enabling LPBF for commercial, high performant heat exchangers.
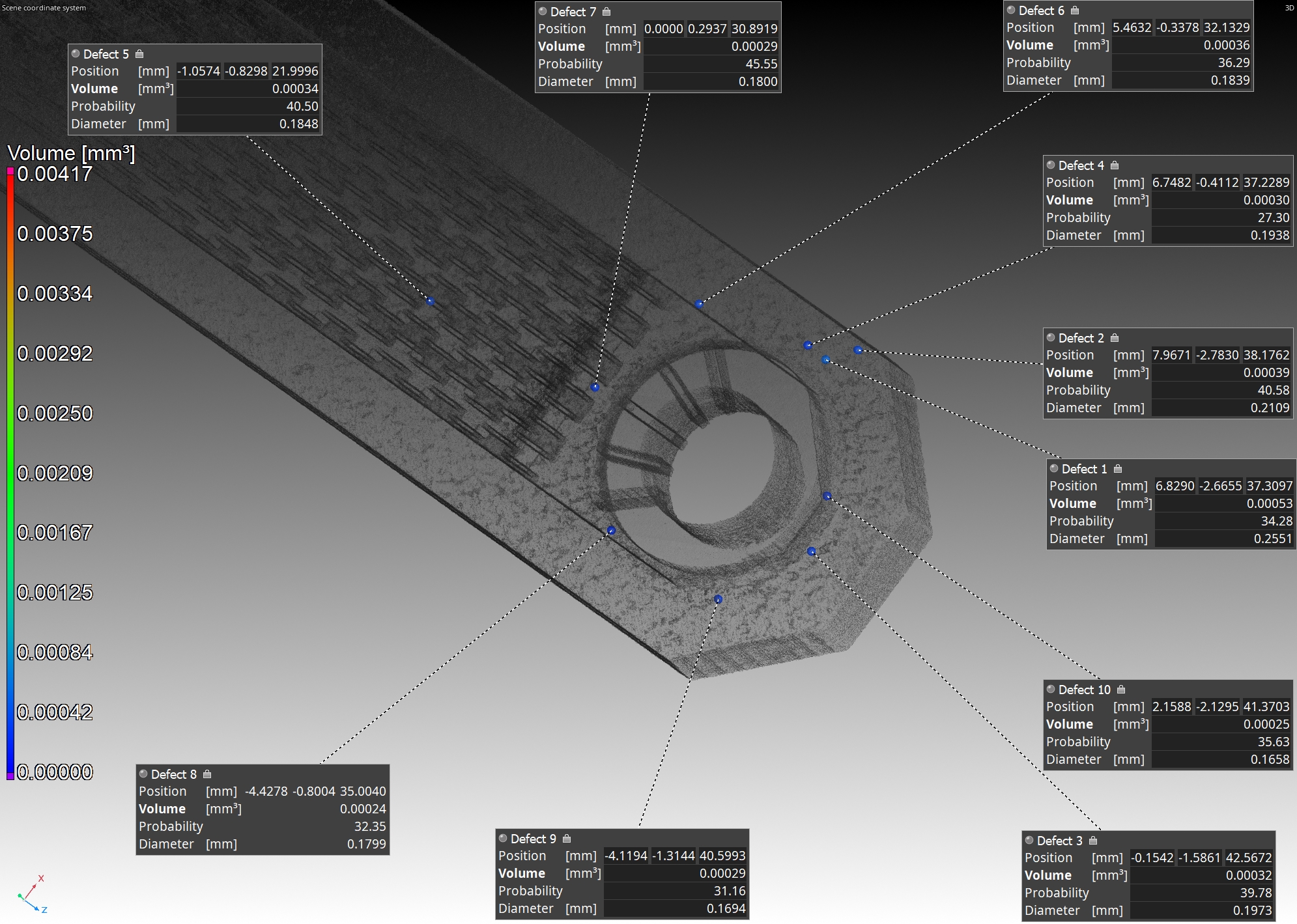
Figure 5: Inclusion analysis performed in VG Studio Max 3.5.1 with annotations on the 5 largest inclusions (foreign material)
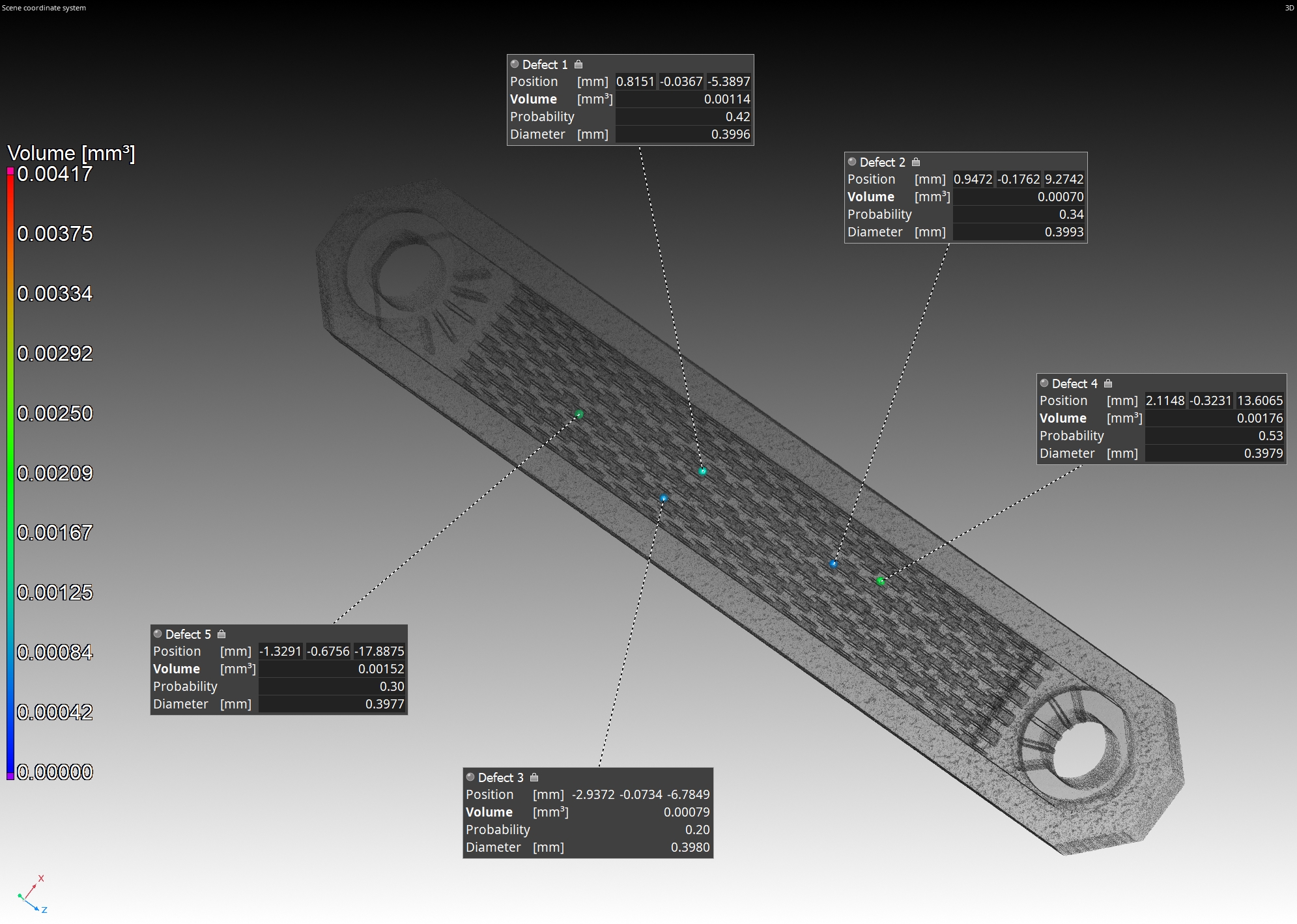