Au cours des dernières années, l’accent a été mis de plus en plus sur la qualité perçue, c’est-à-dire le jugement des clients sur la qualité globale de la construction d’une voiture. Cet aspect est généralement axé sur la qualité de l’ajustement des panneaux, en particulier sur le jeu et l’affleurement entre ces panneaux.
Par exemple, le jeu entre la porte avant et la porte arrière est très important pour des raisons esthétiques, mais aussi pour des raisons fonctionnelles – si la porte arrière dépasse de la porte avant, cela peut provoquer des bruits d’air dans l’habitacle.
Pour garantir l’ajustement correct des panneaux dans la garniture et la finition, la caisse en blanc doit être assemblée correctement dans l’atelier de carrosserie. Cela commence par l’outillage où les pièces du sous-ensemble sont épinglées et serrées. Au fur et à mesure que ces petites pièces sont assemblées pour former un soubassement, et finalement une caisse en blanc, la qualité de construction de ces grands ensembles aura une incidence directe sur l’ajustement et la finition (qualité perçue) de la voiture finie.
Les trous et les surfaces utilisés par les goupilles d’outillage et les surfaces de serrage sont essentiels pour obtenir la qualité de construction et, en fin de compte, la qualité perçue. Il est essentiel de disposer de données exactes et précises pour ces entités afin de garantir l’exactitude de l’outillage et, au final, la qualité de construction de la caisse en blanc, qui a une influence directe sur l’ajustement et la finition. De nombreux ateliers de carrosserie automobile utilisent la mesure en ligne pour mesurer les assemblages sous le châssis et de caisse en blanc.
La plupart des technologies utilisées pour ces mesures sont des données relatives – elles ne sont pas d’une précision absolue. Les données des systèmes relatifs ne sont pas d’une précision absolue et ne peuvent pas être utilisées pour déterminer la précision de l’outillage – après avoir mesuré les trous et les surfaces de serrage. Lorsqu’un système relatif détecte un problème (caractéristique hors tolérance), l’assemblage est généralement soumis à un système de mesure de référence (MMT) pour confirmer ou infirmer les résultats du système de mesure en ligne.
En utilisant un système de mesure absolu, traçable et précis pour mesurer ces assemblages dans l’atelier de carrosserie, les données peuvent être utilisées pour ajuster l’outillage afin d’assurer une meilleure qualité de fabrication et fournir une analyse statistique précise du processus, car les données sont absolues.
Le Laser Radar Nikon peut atteindre une précision et une répétabilité de niveau « MMT » dans l’atelier, fournissant des données précises, traçables et fiables, permettant aux constructeurs automobiles d’améliorer le processus et la qualité des assemblages au point de fabrication.
La précision du Laser Radar Nikon peut être démontrée à l’aide d’un artefact indépendant, tel qu’un tétraèdre Inora. Le Laser Radar a une EMT comparable à celle des MMT HA. Vous trouverez ci-dessous des exemples de résultats de mesure d’une Inora.
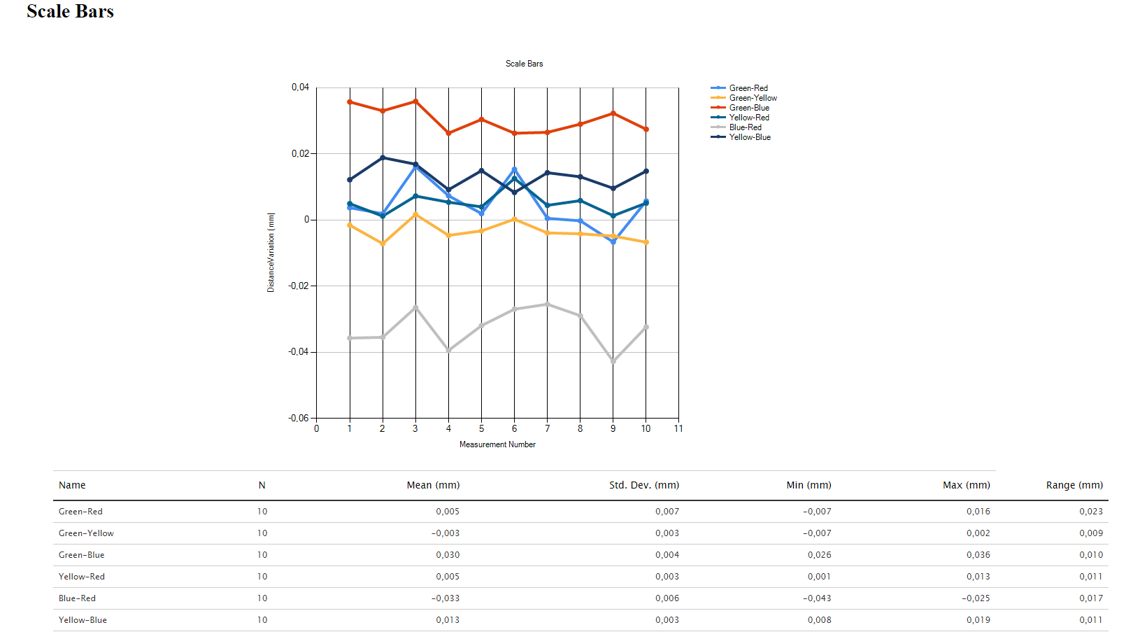
Lors de la mesure de pièces et de composants, le Laser Radar Nikon utilise un faisceau laser infrarouge pour capturer des données de balayage dans des modèles spécifiques qui sont alignés sur le modèle CAO. Lors de la mesure de trous, de rectangles, de polygones et de surfaces, le Laser Radar Nikon est capable de scanner la surface et les bords de l’entité et d’extraire le résultat correct par rapport au modèle CAO.
L’image ci-dessous montre les différents modèles de balayage disponibles pour le Radar Laser afin de mesurer ces entités clés.
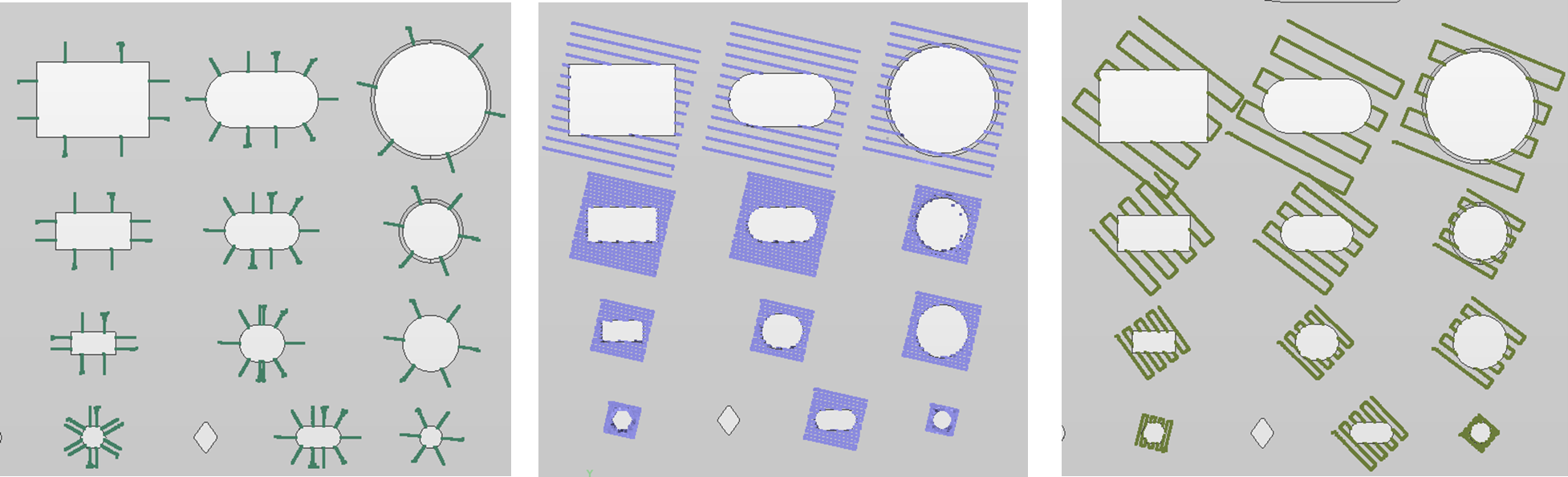
Récemment, Nikon a réalisé plusieurs tests pour ces caractéristiques sur une pièce d’essai. Le Laser Radar a mesuré chaque entités 30 fois à partir de plusieurs distances et angles différents pour démontrer la haute répétabilité réalisable.
Ces mesures ont été effectuées entre 1 et 5 mètres de distance, et jusqu’à un angle d’incidence de 60 degrés. Vous trouverez ci-dessous l’illustration de l’installation avec le Laser Radar à 5 distances différentes de la pièce à mesurer. Le tableau ci-dessous indique la plage maximale et moyenne de la position mesurée pour chaque type d’entités à toutes les distances et sous tous les angles pour le motif en étoile rapide :
Type d’entité | Trou | Fente | Rectangle | Polygone | Surface |
Plage moyenne | 0,05 mm | 0,07 mm | 0,06 mm | 0,04 mm | 0,02 mm |
Plage maximale | 0,10 mm | 0,15 mm | 0,16 mm | 0,12 mm | 0,05 mm |
Délai de mesure | 2,6 s | 2,6 s | 2,3 s | 2,7 s | < 0,5 s |
Les résultats de la répétabilité de la distance sur ces entités sont inférieurs à 160 microns avec une plage moyenne de moins de 0,1 mm pour 30 mesures entre 60 degrés, et de 1 m à 5 m pour le modèle de balayage en étoile et les paramètres d’extraction communs.
Si l’on utilise un schéma de balayage plus détaillé, comme ceux présentés ci-dessus, la plage peut être réduite à moins de 0,12 mm, ce qui prend plus de temps à mesurer, mais permet également d’effectuer des mesures à des angles d’incidence plus élevés.
Ces données illustrent l’intolérance du Laser Radar aux configurations d’angle et de plage. La capacité du Laser Radar à mesurer les entités de manière répétée à partir d’une large plage d’angles et de distances permet un large champ de vision et une couverture élevée des entités, ce qui signifie que peu de positions sont nécessaires pour la mesure, même sur une carrosserie complète.
La possibilité d’obtenir des données répétables et précises dans l’atelier fournira aux clients des données fiables et exploitables, ce qui permettra aux constructeurs automobiles d’améliorer et de valider la qualité des assemblages au point de fabrication dans l’atelier de carrosserie.
Grâce à la précision et à la répétabilité du radar laser Nikon, nous pouvons amener la MMT dans l’atelier, garantissant ainsi des données de qualité, précises et répétables. Demandez plus d’informations directement à notre équipe de vente et d’application en Europe ici ou consultez notre Centre de ressources pour les brochures et les Livres blancs. ;