Die Röntgen-Computertomografietechnologie (CT) von Nikon ermöglichte es Tochigi Nikon, einem führenden Hersteller optischer Komponenten, eine bahnbrechende Lösung zu entwickeln, die die Welt des Präzisionsspritzgusses von Kunststoffteilen verändert hat.
Das in Japan ansässige Unternehmen Tochigi Nikon sah sich mit einem branchenweiten Problem konfrontiert: Die Herstellung von zylindrischen Kunststoffkomponenten, wie z. B. Kameraobjektiven, war eine mühsame Angelegenheit, da diese Produkte bei ihrer Herstellung hochgenaue, möglichst perfekte Kreise erfordern. Die Gussform entsprechend zu modifizieren, war arbeits- und zeitintensiv und erforderte oft qualifizierte Techniker und mehrere Korrekturzyklen.
Heute hat Tochigi Nikon den Formkorrekturprozess mit Hilfe der CT-Technologie von Nikon optimiert, was zu erheblichen Kosteneinsparungen und Effizienzsteigerungen in bemerkenswert kurzer Zeit geführt hat; die Ingenieure von Tochigi Nikon haben sich in nur drei Monaten auf das neue Paradigma eingestellt.
Tochigi Nikon wurde 1961 als hundertprozentige Tochtergesellschaft von Nikon gegründet und produziert optische Komponenten und Module innerhalb der globalen Nikon-Gruppe. Dank der fortschrittlichen Produktionstechnologie im Bereich der Präzisionsobjektive hat Tochigi Nikon ein breites Spektrum an optischen Linsen entwickelt, die in Branchen rund um den Globus zum Einsatz kommen.
Innerhalb von Tochigi Nikon konzentriert sich die erste Abteilung für Fertigungstechnik auf Ersatzobjektive für spiegellose Kameras, während der Engineering-Sektor für die Massenproduktion von Kunststoffspritzgussteilen zuständig ist, einschließlich derjenigen, die in Ersatzobjektiven für spiegellose Kameras verwendet werden.
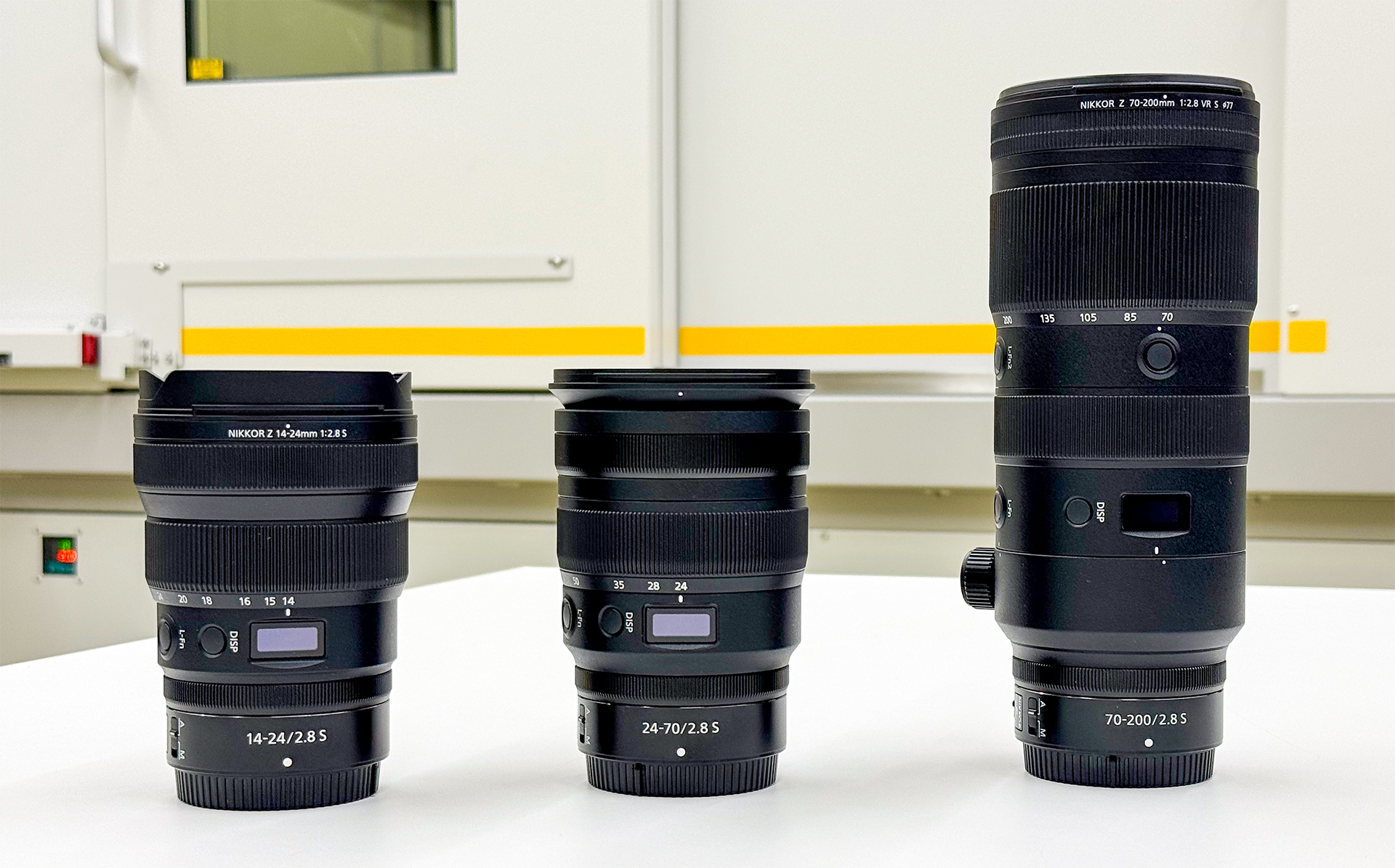
Die spritzgegossenen Bauteile der Ersatzobjektive erfordern einen Kreis, der möglichst perfekt rund sein muss. Aufgrund der in der Industrie herrschenden Zwänge sind diese Teile jedoch nicht in einem perfekten Kreis angeordnet und müssen daher noch weiter untersucht werden.
Um dieses Problem zu lösen, wird die Gussform modifiziert, um die Unrundheit der Kunststoffkomponente zu korrigieren und sie einer perfekten Kreisform anzunähern. Dieser Prozess der „Formkorrektur“ wird in der Regel zwei- oder dreimal wiederholt, um die Genauigkeit schrittweise und mit zunehmendem Aufwand zu verbessern.
Verbesserte Formkorrektur mit der CT-Bildgebung von Nikon
Aber das war nicht die einzige Herausforderung. In den letzten Jahren sind spritzgegossene Kunststoffteile aufgrund ihrer geringen Größe, der Gewichtsreduzierung und der verbesserten Funktionalität immer komplexer in der Formgebung geworden.
Auch die Vermessung dieser Teile mit herkömmlichen KMG und Bildmessmaschinen ist nicht einfach, denn das Messprogramm und die Erstellung von Änderungsanweisungen für die Formen erhöhen den gesamten Arbeitsaufwand und machen den Prozess noch zeit- und kostenintensiver.
Auf der Suche nach einer Lösung für diese Herausforderungen entdeckte Tochigi Nikon das Nikon MCT225 und erkannte sofort, wie es zur Optimierung des Formkorrekturprozesses und damit zu Kosteneinsparungen und Effizienzsteigerungen beitragen konnte.
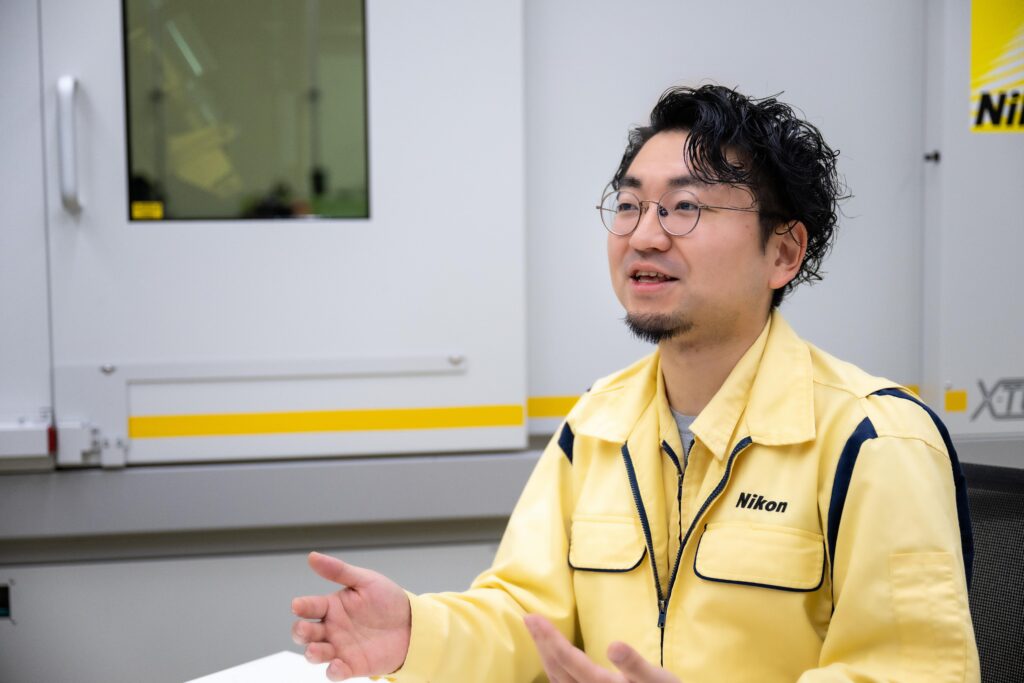
„Einer der Gründe, warum wir uns für die industriellen Röntgen-CTs von Nikon entschieden haben, war, dass Nikon in der Klasse der Mikrofokus-Röntgenquellen, dem größten Markt der Welt, den höchsten Marktanteil hat“, erklärt Shota Miyamoto, Ingenieur bei Tochigi Nikon.
Die Mess-Computertomografie (MCT) von Nikon ist eine von Nikon entwickelte und hergestellte Hochleistungs-Mikrofokus-Röntgenquelle, die eine hohe Bildqualität und eine lange Betriebsdauer bietet. Das MCT225 von Nikon macht sich dies zunutze und bietet hochpräzise Messmöglichkeiten mit einer Genauigkeit von 9 + L/50 μm bei der Messung einer einzelnen groben Materialprobe.
Einer der Hauptvorteile ist die Fähigkeit, sowohl die Innen- als auch die Außenabmessungen von Produkten ohne physischen Kontakt oder Einschränkungen effizient zu messen, erklärt Miyamoto. Dieses Konzept der berührungslosen Messung entspricht der Richtlinie VDI/VDE2630 des Verbandes Deutscher Techniker und gewährleistet eine zuverlässige und präzise Vermessung.
Automatisierung der Formvermessung mit dem MCT225 von Nikon
Der Zweck der Formkompensation besteht darin, die Abmessungen der in der Form hergestellten Teile so zu verändern, dass sie den vorgesehenen Abmessungen entsprechen. In der Vergangenheit wurden nach der Herstellung von Testprodukten für die Formkorrektur manuelle Messungen mit Digital-Mikrometern, Prüfstiften und anderen Werkzeugen durchgeführt, zusätzlich zu den automatischen Messergebnissen aus KMG und Bildmessmaschinen.
Anschließend wurde die Form korrigiert, wobei durch Wiederholung der Mess- und Werkzeugkorrekturzyklen die Genauigkeit der Teile schrittweise erhöht wurde.
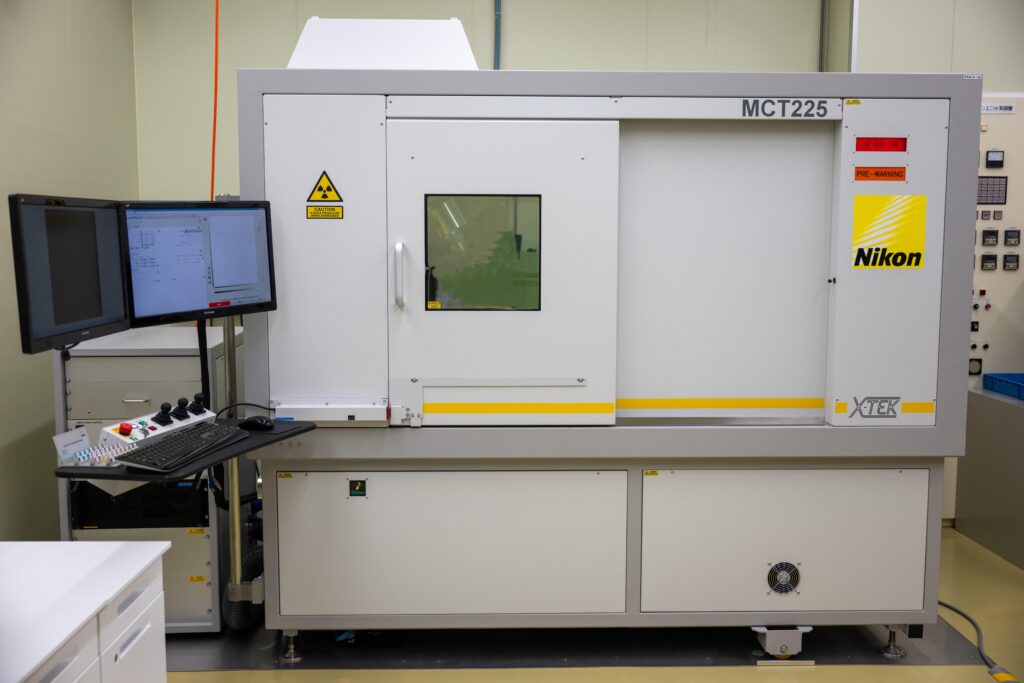
„Das MCT225 ermöglicht es, bei der Erstellung eines Messprogramms für Spritzgussteile ein Messprogramm nur mit CAD-Daten zu erstellen“, erklärt Miyamoto. „Neben der Tatsache, dass keine physischen Proben vorbereitet werden müssen, sehe ich eine große Lösung auch darin, dass keine Präzisionsvorrichtungen zum Einrichten der Teile erforderlich sind.
„Außerdem ist es nicht mehr erforderlich, ein Messprogramm mit mehreren Probenpositionen zu erstellen, die Geschicklichkeit erfordern, oder das Programm bei der Überprüfung des Messstatus zu überarbeiten, wodurch sich der Arbeitsaufwand erheblich verringert hat.“
Optimierung der Arbeitsabläufe bei der Formkompensation
Die durch das MCT225 erfassten Daten werden mittels Stapelverarbeitung automatisch in das STL-Format konvertiert. Die STL-Daten und Messprogramme werden auf einem Server gespeichert. Die Arbeiter müssen dann nur noch die Aufnahmebedingungen lesen und die Teile platzieren, wodurch sich die Zeit für den Röntgen-CT-Scan auf nur fünf Minuten reduziert.
„Wir können nun STL-Daten und Messprogramme vom Server abrufen und die Messungen an unserem Arbeitsplatz durchführen, was die Arbeitsbelastung und den Zeitaufwand der Bediener im Vergleich zum vorherigen System erheblich reduziert hat“, sagt Miyamoto. „Tochigi Nikon hat ein hausinternes Makro entwickelt, das auf die zylindrische Messung spezialisiert ist und die Zeit zum Erstellen des Programms für die Bauteilmessung sowie die Zeit für Programmänderungen um bis zu 50 Prozent im Vergleich zum vorherigen Verfahren reduziert hat.“
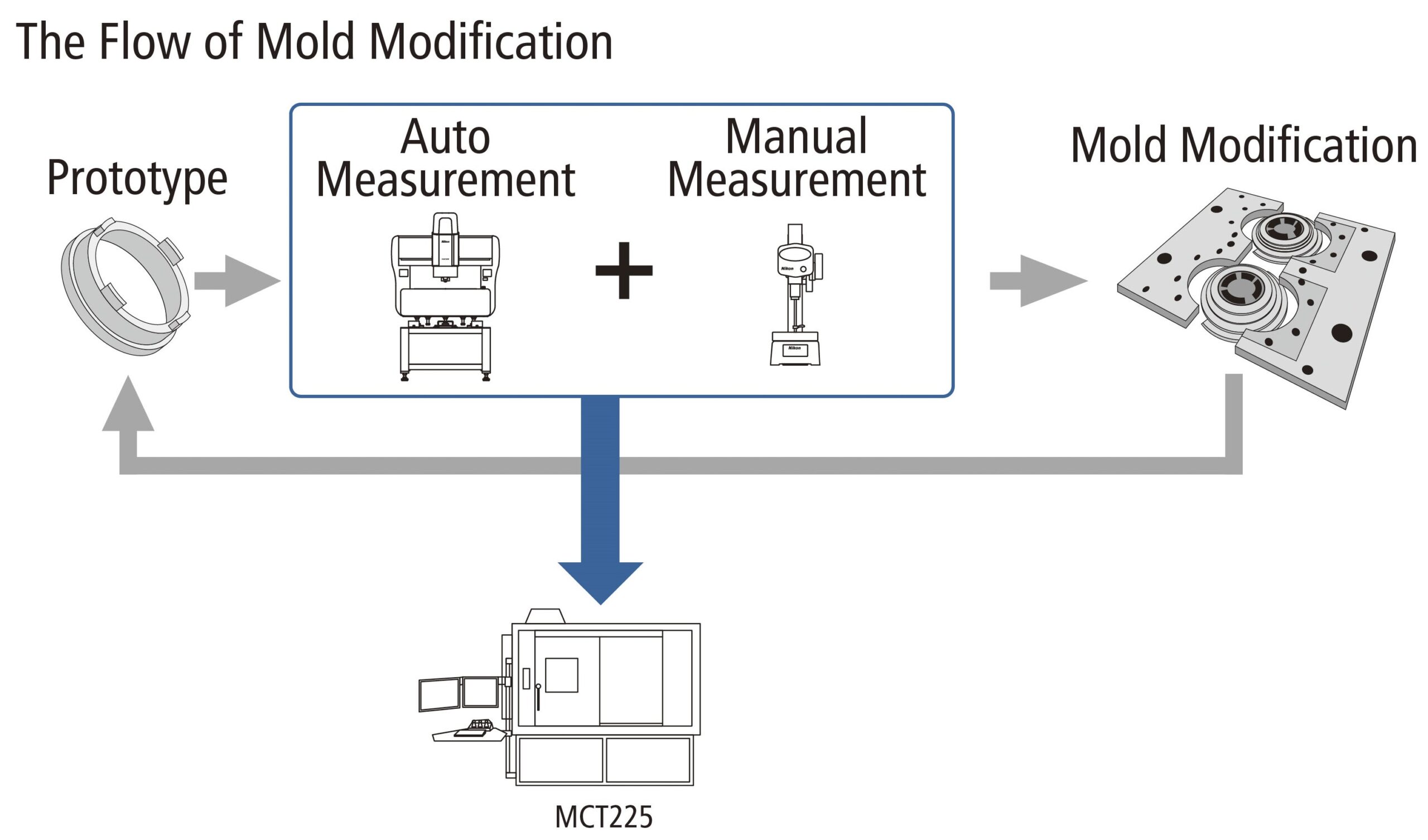
Die mit dem MCT225 erhaltenen STL-Daten können mit der 3D-Messsoftware Polyworks Inspector verwendet werden, um anhand der 3D-Daten, die mittels einer Farbkarte visualisiert werden, den Umfang der Formkompensation zu bestimmen, was die Analyse nach der Messung erheblich vereinfacht. Miyamoto sagt, dass sein Ingenieurteam dank des MCT225 in der Lage war, Messungen in nur drei Monaten durchzuführen.
„Darüber hinaus haben wir durch die Optimierung beim Erstellen von Messprogrammen und bei der Vorbereitung von Korrekturanweisungen für die Werkzeugkorrektur den Zeitaufwand für die Werkzeugkorrektur um bis zu acht Wochen reduziert, was einer Verkürzung um 30 Prozent entspricht.“
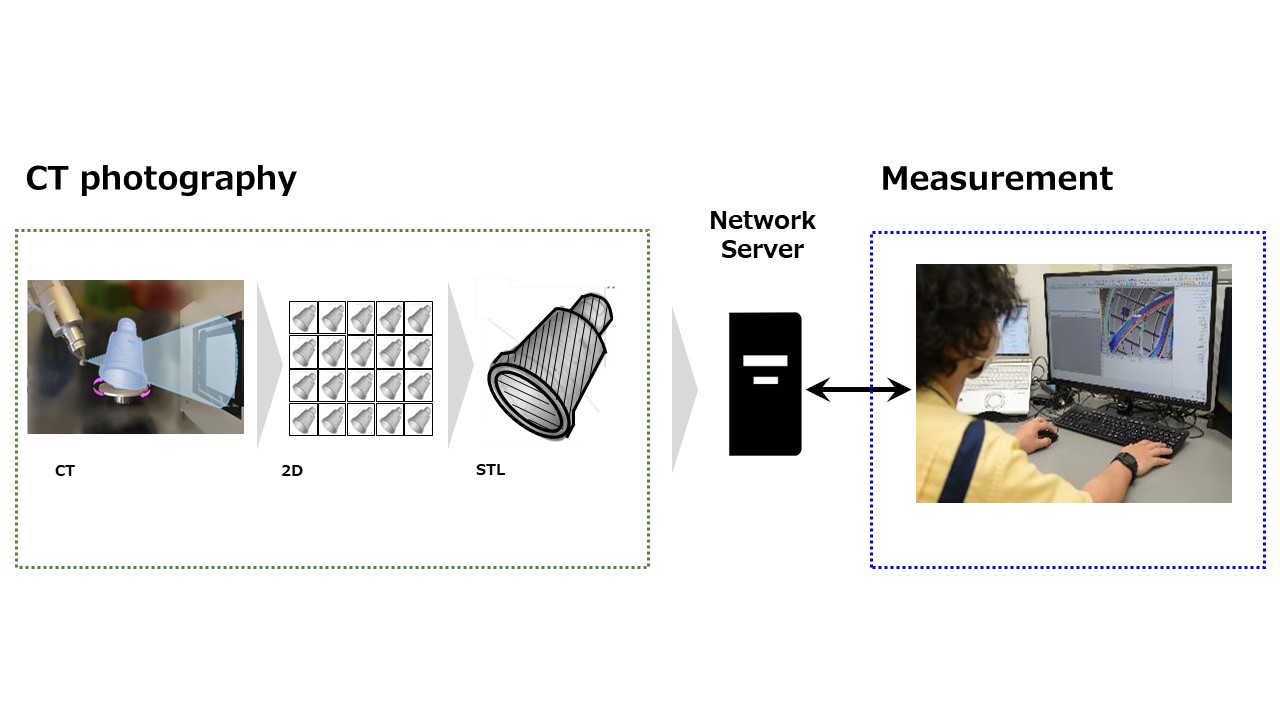
Das MCT225 von Nikon sorgt für Innovation beim Messvorgang
Das MCT225 ermöglicht die Messung von 3D-Daten in beliebiger Form, selbst in engen Räumen, ohne fehlende Elemente. Dies ist sehr nützlich bei der Messung von Spritzguss-Kunststoffteilen. Wenn zum Beispiel ein planares Teil – das für die Funktionalität des Objektivs entscheidend ist – nicht zentriert ist, wird die Messung mit einem KMG schwierig.
„Das MCT225 konvertiert das gesamte Bild in den 3D-Raum, wobei es keine Formbeschränkungen für die Messung gibt, die Messfreiheit hoch ist und keine fehlenden Daten vorhanden sind“, sagt Miyamoto. „Es kann berührungslos und ohne Einschränkung aufgenommen werden, ohne dass ein spezielles Werkzeug erforderlich ist, und auch die Aufnahme selbst erfordert keine besonderen Fähigkeiten. Es funktioniert sowohl mit Microsoft Excel als auch mit herkömmlichen Messungen. Ich bin der Meinung, dass das MCT225 eine wesentliche Neuerung in den Messprozess gebracht hat.“
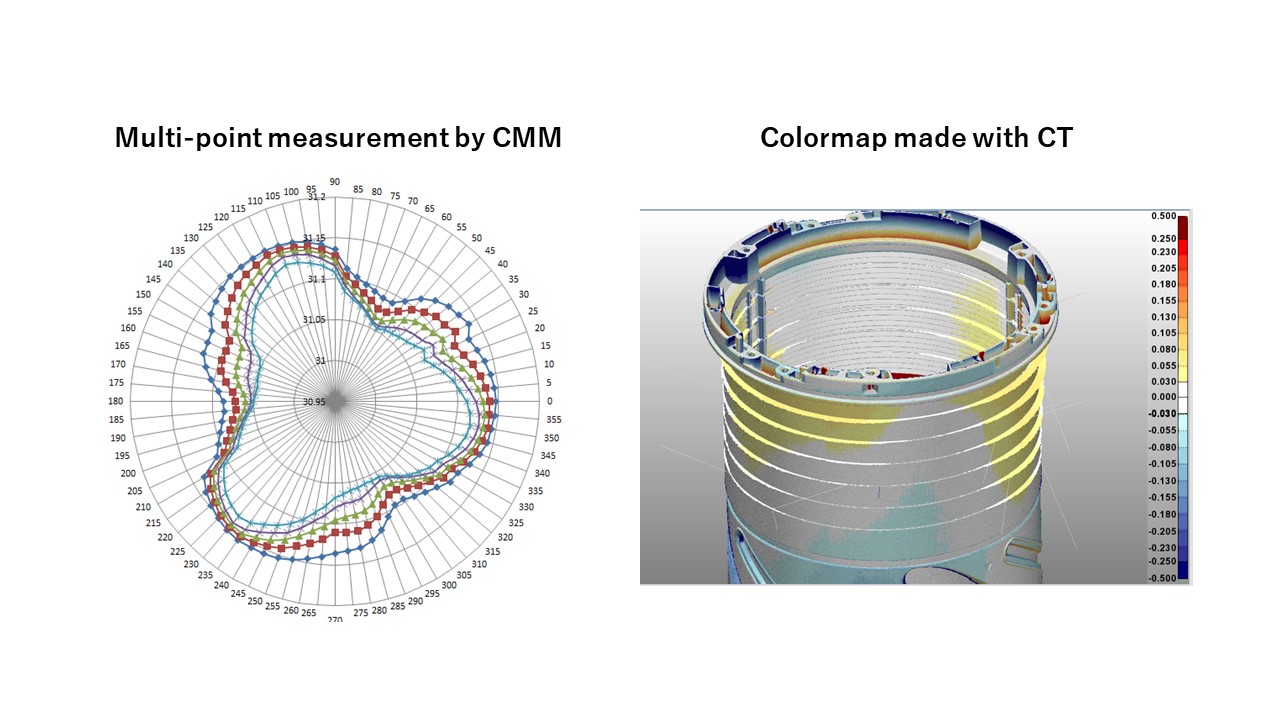
Im Geschäftsjahr 2020 erzielte Tochigi Nikon eine Kostenreduzierung von rund 80 Prozent, die sich aus mehreren Vorteilen ergab, darunter die Auswirkungen einer verkürzten Zeit für die Erstellung von Messprogrammen, kürzere Korrekturzeiten, Mitarbeiter mit Mehrfachqualifikationen und geringere Kosten für Unteraufträge.
„In Zukunft möchten wir mit Volume Graphics an der Bearbeitung von Freiformflächen mit Geometriekorrektur arbeiten“, sagt Miyamoto. „Mit Hilfe von Reverse Engineering CT-Messungen, Geometriekorrekturen und Formbearbeitungen können wir die Präzision von Bauteilen durch die Bearbeitung von Freiformflächen erhöhen und die Effizienz durch den effektiven Einsatz von 3D verbessern.“
Die Zukunft der Herstellung von Kunststoff-Spritzgussformen steht vor einem bedeutenden Wandel, der durch die Abkehr von herkömmlichen KMGs und Bildmessmaschinen hin zu einer fortschrittlicheren und messbareren Röntgen-CT-Technologie vorangetrieben wird. Da sich Hersteller wie Tochigi Nikon diesen transformativen Ansatz zu eigen machen, sind sie gut positioniert, um bemerkenswerte Produktivitätssteigerungen zu erzielen und ihren Wettbewerbsvorteil in einem zunehmend anspruchsvollen globalen Markt zu stärken.