REM Surface Engineering s’est tourné vers Nikon et ses technologies de rayons X haute résolution pour découvrir les défauts internes et la rugosité de surface de pièces que d’autres méthodes ne pouvaient pas détecter, ce qui a permis de résoudre un problème essentiel pour ses clients industriels.
La technologie de tomodensitométrie par rayons X (CT) de Nikon a permis à REM Surface Engineering de transformer ses applications de test et d’inspection uniques et particulièrement exigeantes. Opérant à la pointe de l’excellence en matière d’ingénierie, REM Surface Engineering, basé ‘dans le Connecticut, a acquis un avantage crucial grâce à son partenariat avec Nikon et ses systèmes de tomodensitométrie à rayons X haute résolution. Ces solutions d’imagerie avancées ont permis à REM Surface Engineering de découvrir des défauts internes et des irrégularités de surface dans les composants de leurs clients qui étaient auparavant indétectables par des méthodes conventionnelles.
Fondée en 1965, REM Surface Engineering a mis en place une technologie de superfinition isotrope brevetée pour les composants métalliques. Une large gamme d’alliages peut être finie par REM Surface Engineering, y compris des pièces qui sont fabriquées par des procédés additifs traditionnels ou plus récemment développés. Les secteurs tels que l’espace, l’aéronautique, l’automobile et la défense nécessitent des composants avec des textures de surface optimisées pour répondre aux exigences de performance spécifiques de leurs applications, y compris des augmentations de la résistance à la fatigue de contact et à la fatigue de flexion, un débit amélioré pour réduire les turbulences et la chute de pression, et bien d’autres.
« Nous avons une technologie de polissage chimique pure », déclare Justin Michaud, Président et Directeur de REM Surface Engineering. « C’est comme une version plus raffinée du broyage chimique ou de la gravure chimique, où nous sommes beaucoup plus précis dans notre application de ces produits, tant du point de vue de la formulation que du point de vue de l’application, pour pouvoir contrôler la façon dont nous modifions la texture de la surface. De plus, nous avons un procédé combinatoire de polissage chimique-mécanique qui utilise des produits chimiques appariés aux alliages pour permettre un affinage de surface en douceur au moyen d’approches spécialisées de finition de masse; cette technique est capable de maintenir les géométries des composants à un degré beaucoup plus élevé que les procédés abrasifs traditionnels, et elle peut réduire davantage la texture de surface au besoin. »
Cette modification des textures de surface crée un degré de douceur crucial pour les clients de haute technologie de REM Surface Engineering, dont les produits finaux exigent souvent la plus grande réduction possible de la rugosité et des déformations de surface, aussi mineures soient-elles.
« Les engrenages, les huiles d’avion, les moteurs de fusée et d’autres composants de précision bénéficient de surfaces plus lisses en termes de fatigue de contact, d’efficacité du flux d’air ou de conditions de fonctionnement difficiles », explique M. Michaud.
Validation par tomodensitométrie à rayon X de Nikon
Bon nombre des pièces qui entrent dans les assemblages terminés sont actuellement créées par la fabrication additive, qui a initialement créé des goulots d’étranglement pour l’équipe REM Surface Engineering.
« Il y a près de 15 ans, les fabricants aérospatiaux avec lesquels nous travaillions sont devenus parmi les premiers à se lancer dans la fabrication additive de métaux en toute évidence », déclare M. Michaud. « Lorsque ces pièces ont commencé à arriver, elles semblaient évidemment très différentes des pièces de précision, usinées ou fraisées auxquelles nous étions habitués. »
Les défauts tels que la porosité, les piqûres et l’ondulation peuvent tous affecter considérablement et négativement les performances des assemblages de composants. Il est essentiel pour la réussite de l’entreprise de pouvoir identifier ces problèmes sans détruire les pièces, puis de prouver aux clients comment le processus de REM Surface Engineering a eu un effet positif sur la régularité de ces surfaces.
M. Michaud explique que les caractéristiques de surface des pièces fabriquées de manière additive sont très différentes de celles produites par des procédés de fabrication plus traditionnels.
« Il s’agit de surfaces plus complexes que les surfaces usinées », convient Agustin Diaz, Ph.D., Directeur de la fabrication de pointe et de l’innovation chez REM Surface Engineering. « Les pièces fabriquées de façon additive ont des textures de surface très riches. »
Comme des échantillons de ces pièces provenaient des clients pour les tests et les analyses, il est devenu clair qu’il y avait des questions sur l’intégrité près de la surface, en particulier en ce qui concerne la porosité.
« Notre procédé de finition chimique nous permet de toujours nous assurer que nous ne provoquons pas d’oxydation intergranulaire ou par piqûres », explique M. Diaz. « Au milieu du processus, alors que nous réduisions la texture de surface, nous commencions à voir des choses étranges émerger. »
« Je pensais que nous faisions peut-être passer l’échantillon au travers de notre processus, mais il s’est avéré que le problème était les échantillons eux-mêmes, qui avaient tous ces défauts internes que nous ne pouvions pas voir ou caractériser jusqu’à ce que nous fassions une analyse destructive ou un scan CT par rayon X haute résolution. »
Révéler la vérité à l’aide de la tomodensitométrie à rayon X de Nikon
L’expression « haute résolution » est essentielle ici, car, dans certains cas, les clients peuvent avoir effectué leur propre analyse de tomodensitométrie à rayons X sur les pièces, qui n’a montré aucune porosité.
« Je leur demanderais quelle taille de voxel ils ont utilisé pour cette inspection », explique le Dr Diaz. « La plupart du temps, c’est autour de 90 microns. Eh bien, vous n’aurez pas le niveau de détail nécessaire à cette résolution. Ils peuvent croire qu’ils n’avaient aucune porosité, mais lorsque vous commencez à traiter la pièce et que vous retirez 50 ou 130 microns de la surface, vous voyez comment la surface évolue et vous pouvez observer tous ces défauts « cachés » qui ressortent. »
« Lorsque vous avez la tomodensitométrie à rayons X à haute résolution, vous pouvez voir toute la porosité accumulée dans la surface proche de l’échantillon. Donc, cette partie qui était censée être 100 % dense ne l’est pas comme attendu, et la porosité est également très anisotrope. »

Selon Brian Barlow, Responsable national du développement commercial des services d’inspection de tomodensitométrie à rayons X de Nikon, cela met en évidence les avantages des capacités de numérisation haute résolution de Nikon.
« Notre technologie de tomodensitométrie à cible rotative microfoyer nous permet d’obtenir certaines des numérisations de résolution les plus élevées de l’industrie, en particulier sur des échantillons de plus haute densité », explique Barlow. « Ces résultats d’analyse de haute qualité ont été essentiels au succès de nos projets avec REM Surface Engineering.
De nombreux clients de REM Surface Engineering doivent voir l’état initial de la pièce par rapport à la finition après traitement fourni par REM », poursuit M. Barlow. « Le services d’inspection de tomodensitométrie à rayon X de Nikon scanne à la fois la pièce traitée initiale et après traitement une fois la surface post-traitée pour permettre, de manière non destructrive, la mesure précise de ces différences. »
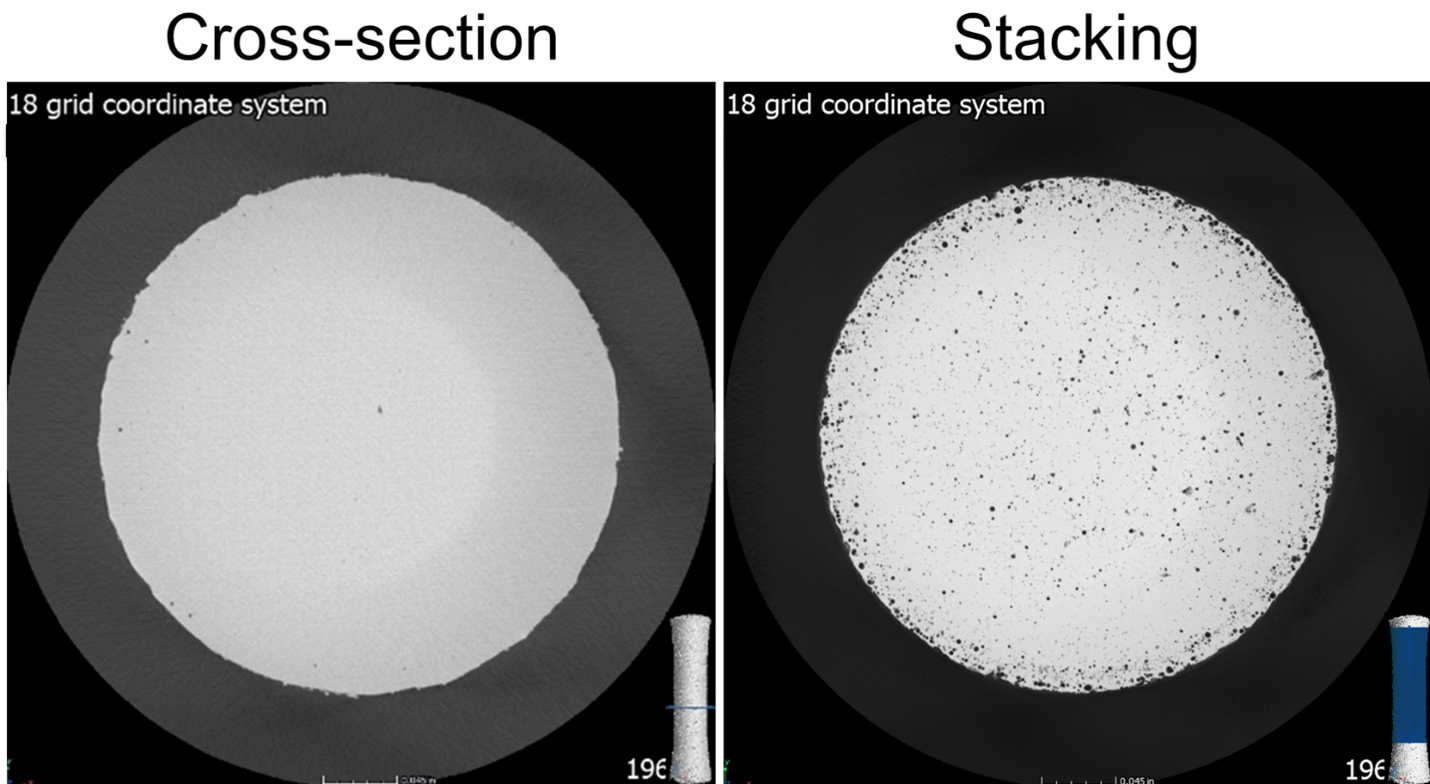
Le partenariat avec Nikon permet à REM Surface Engineering de démontrer la valeur de son processus. Les pièces qui semblent lisses à l’œil nu et qui passent même le contrôle initial aux rayons X présentent des défauts lorsqu’elles sont examinées par le système de rayons X avancé de Nikon. Après le polissage chimique, le second scan révèle une amélioration spectaculaire de la régularité de la surface, ce qui conduit à une performance nettement améliorée pour les produits finaux. La capacité de prouver ces avantages tangibles est la raison pour laquelle les clients reviennent à REM Surface Engineering.
Parler le même language
Le partenariat entre REM Surface Engineering et Nikon Metrology est couronné de succès car les deux sociétés ont une base solide dans les principes d’ingénierie et les fondements scientifiques. Leurs équipes parlent le même langage et peuvent collaborer efficacement pour développer ensemble des solutions innovantes.
« L’équipe Nikon a été très utile pour traiter un large éventail d’alliages », explique M. Michaud. « Nous y sommes parvenus avec des composants en aluminium, des composants en titane, des composants en superalliage de nickel et des composants en cuivre. Ces matériaux sont numérisés différemment, mais ensemble, nos équipes ont pu prendre en charge tous ces besoins et ces applications. »
M. Diaz convient que le solide niveau de prise en charge offert par l’équipe Nikon en ce qui concerne les exigences spécifiques de REM Surface Engineering a largement contribué à la réussite de cette collaboration.
« Ils sont toujours là pour vous aider avec les questions techniques que vous avez en plein milieu d’un projet », explique le Dr Diaz. « Si nous sommes bloqués sur un élément spécifique d’un scan, nous appelons, et cinq minutes plus tard, nous avons une réponse, plus une belle photo à mettre dans un rapport ou à montrer au client. Ce niveau de service client est excellent. »
À mesure que les applications de fabrication deviennent plus complexes et que la mesure des finitions de surface devient plus difficile, les ingénieurs de REM Surface Engineering et de Nikon amélioreront leurs processus pour fournir de meilleures finitions de surface qui répondent aux demandes industrielles croissantes.
Et à mesure que les techniques de fabrication avancées comme l’impression 3D se répandent, il sera essentiel d’assurer des finitions de surface lisses sur les pièces. Les systèmes de tomodensitométrie à rayons X précis de Nikon permettent aux entreprises d’inspecter et de mesurer les caractéristiques de surface sans détruire la pièce. Cette capacité non destructive de test de tomodensitométrie micro est une partie essentielle du flux de travail de fabrication. Cela permet un cycle d’amélioration continue, où les finitions de surface deviennent meilleures, offrant des avantages croissants.
« Nous sommes très heureux de nos relations avec l’équipe Nikon », explique M. Michaud. « Ils sont réactifs, à un prix raisonnable et excellents dans ce qu’ils font. C’est pourquoi nous sommes si fidèles. Nous n’envisagerions même pas une autre option. »