REM Surface Engineering hat sich an Nikon und seine hochauflösenden Röntgentechnologien gewandt, um interne Defekte und Oberflächenrauheit in Bauteilen aufzudecken, die mit anderen Verfahren nicht erkannt werden konnten, wodurch ein zentrales Problem für seine Industriekunden gelöst werden konnte.
Die von Nikon bereitgestellte Röntgen-Computertomographie-Technologie (CT) hat REM Surface Engineering in die Lage versetzt, seine einzigartigen – und äußerst anspruchsvollen – Test- und Prüfanwendungen zu verändern. Das in Connecticut ansässige Unternehmen REM Surface Engineering hat sich durch seine Partnerschaft mit Nikon und dessen hochauflösenden Röntgen-CT-Scansystemen einen entscheidenden Vorteil verschafft. Diese fortschrittlichen Bildgebungslösungen haben REM Surface Engineering in die Lage versetzt, interne Defekte und Oberflächenunebenheiten in den Komponenten ihrer Kunden aufzudecken, die zuvor mit herkömmlichen Verfahren nicht zu erkennen waren.
Das 1965 gegründete Unternehmen REM Surface Engineering hat eine patentierte isotrope Superfinish-Technologie für Metallkomponenten entwickelt. REM Surface Engineering kann eine Vielzahl von Legierungen bearbeiten, darunter auch Bauteile, die entweder mit traditionellen subtraktiven oder neueren additiven Verfahren hergestellt werden. Branchen wie Luft- und Raumfahrt, Automobilindustrie und Verteidigung benötigen Komponenten mit optimierten Oberflächentexturen, um ihre anwendungsspezifischen Leistungsanforderungen zu erfüllen, wie beispielsweise die Erhöhung der Beständigkeit gegen Kontakt- und Biegeermüdung, eine verbesserte Strömung zur Reduzierung von Turbulenzen und Druckabfall und viele anderen Möglichkeiten.
„Wir verfügen über eine rein chemische Poliertechnik“, laut Justin Michaud, Präsident und CEO von REM Surface Engineering. „Es ist wie eine verfeinerte Version des chemischen Fräsens oder chemischen Ätzens, wobei wir bei der Anwendung dieser Produkte sehr viel präziser vorgehen, sowohl von der Formulierung als auch von der Anwendung her, um kontrollieren zu können, wie wir die Oberflächenstruktur verändern. Darüber hinaus verfügen wir über einen kombinierten chemisch-mechanischen Polierprozess, der mit Hilfe von auf die jeweilige Legierung abgestimmten Chemikalien eine sanfte Oberflächenveredelung durch spezielle Massenbearbeitungsmethoden ermöglicht. Diese Technik ist in der Lage, die Geometrien der Komponenten in einem viel höheren Maße beizubehalten als herkömmliche, abrasive Verfahren und kann die Oberflächenstruktur bei Bedarf weiter reduzieren.“
Diese Veränderung der Oberflächentexturen führt zu einer Glätte, die für die Hightech-Kunden von REM Surface Engineering von entscheidender Bedeutung ist, da deren Endprodukte oft eine größtmögliche Reduzierung von Oberflächenrauheit und Verformungen erfordern, wie gering diese auch erscheinen mögen.
„Zahnräder, Tragflächen, Raketentriebwerke und andere Präzisionskomponenten profitieren von glatteren Oberflächen in Bezug auf Kontaktermüdung, Luftströmungseffizienz oder den Umgang mit rauen Betriebsbedingungen“, sagt Michaud.
Validierung durch Nikon-Röntgen-Mikro-CT-Scanning
Viele der Bauteile, die in die fertigen Baugruppen eingesetzt werden, werden derzeit mit Hilfe der additiven Fertigung hergestellt, was anfangs zu einigen Engpässen für das REM Surface Engineering-Team führte.
„Vor fast 15 Jahren gehörten die Luft- und Raumfahrtunternehmen, mit denen wir zusammenarbeiteten, zu den ersten Unternehmen, die sich auf dem Gebiet der additiven Fertigung von Metallen engagierten“, sagt Michaud. „Als diese Bauteile eintrafen, sahen sie natürlich ganz anders aus als die präzisen, maschinell bearbeiteten oder gefrästen Komponenten, an die wir gewöhnt waren.“
Mängel wie Porosität, Lochfraß und Welligkeit können die Leistungsfähigkeit von Komponenten erheblich und negativ beeinflussen. Die Fähigkeit, diese Probleme zu erkennen, ohne die Bauteile zu zerstören, und dann den Kunden zu beweisen, wie das REM Surface Engineering-Verfahren die Glätte dieser Oberflächen positiv beeinflusst hat, ist entscheidend für den weiteren Erfolg des Unternehmens.
Michaud erklärt, dass sich die Oberflächeneigenschaften von additiv gefertigten Bauteilen deutlich von denen unterscheiden, die mit herkömmlichen Fertigungsverfahren hergestellt werden.
„Diese sind komplexer als maschinell bearbeitete Oberflächen“, stimmt Agustin Diaz, Ph.D., REM Surface Engineering’s Advanced Manufacturing and Innovation Manager, zu. „Die additiv gefertigten Bauteile verfügen über sehr unterschiedliche Oberflächenstrukturen.“
Als die Kunden Proben dieser Bauteile zur Prüfung und Analyse einreichten, wurde offensichtlich, dass es einige Fragen zur oberflächennahen Integrität, insbesondere zur Porosität, gab.
„Da es sich um einen chemischen Veredelungsprozess handelt, achten wir stets darauf, dass wir keine intergranulare Oxidation oder Lochfraß verursachen“, sagt Dr. Diaz. „In der Mitte des Prozesses, als wir die Oberflächenstruktur reduzierten, kamen einige merkwürdige Dinge zum Vorschein.“
„Ich dachte, dass wir vielleicht die Probe durch unseren Prozess entkernt haben. Es stellte sich jedoch heraus, dass das Problem die Proben selbst waren, die all diese internen Defekte aufwiesen, die wir nicht sehen oder charakterisieren konnten, bis wir entweder eine zerstörungsfreie Analyse oder einen hochauflösenden Röntgen-CT-Scan durchführten.“
Aufdeckung der Wahrheit mit Nikon Röntgen-CT
Der Begriff „hochauflösend“ ist hier entscheidend, denn in einigen Fällen haben die Kunden ihre eigenen Röntgen-CT-Analysen an den Bauteilen durchgeführt, die keine Porosität zeigten.
„Ich würde sie fragen, welche Voxelgröße sie für diese Prüfung verwendet haben“, erklärt Dr. Diaz. „Meistens sind es etwa 90 Mikron. Nun, bei dieser Auflösung werden Sie nicht den erforderlichen Detailgrad erkennen können. Sie glauben vielleicht, dass keine Porosität vorhanden ist, aber wenn man mit der Bearbeitung des Bauteils beginnt und 50 oder 130 Mikron von der Oberfläche entfernt, sieht man, wie sich die Oberfläche entwickelt und all diese ‚versteckten‘ Mängel zum Vorschein kommen.“
„Mit dem hochauflösenden Röntgen-CT-Scan können Sie die gesamte Porosität sehen, die sich in der nahen Oberfläche der Probe angesammelt hat. Das Bauteil, das eigentlich eine Dichte von 100 Prozent aufweisen sollte, ist also gar nicht so dicht – und auch die Porosität ist sehr anisotrop.“

Dies unterstreicht die Vorteile des hochauflösenden Röntgen-CT-Scannens von Nikon, so Brian Barlow, National Business Development Manager von Nikon Röntgen-CT-Prüfdienstleistungen.
„Unsere Rotationstarget-Mikrofokus-CT-Technologie ermöglicht uns Scans mit einer der höchsten Auflösungen in der Branche, insbesondere bei Proben mit höherer Dichte“, sagt Barlow. „Diese hochwertigen Scanergebnisse waren entscheidend für den Erfolg unserer Projekte mit REM Surface Engineering.
Viele Kunden von REM Surface Engineering wollen den Ausgangszustand des Bauteils im Vergleich zur Nachbearbeitung sehen, die REM anbietet“, fährt Barlow fort. „Nikon Röntgen-CT-Prüfdienstleistungen scannt sowohl das ursprünglich bearbeitete Bauteil als auch die nachbearbeitete fertige Oberfläche und ermöglicht die genaue Messung dieser Unterschiede – und das zerstörungsfrei.“
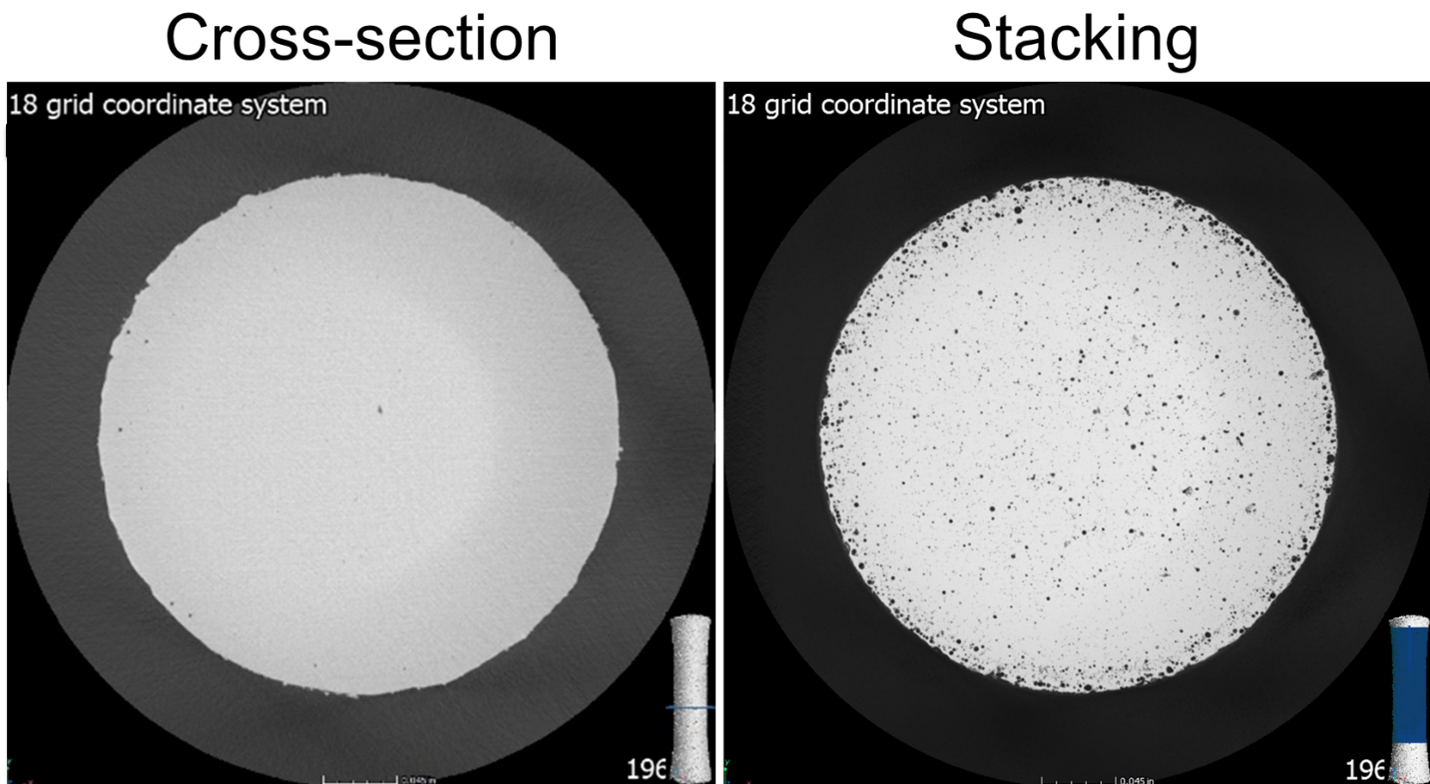
Die Partnerschaft mit Nikon ermöglicht es REM Surface Engineering, den Wert seines Prozesses aufzuzeigen. Bauteile, die mit bloßem Auge glatt erscheinen und sogar einen ersten Röntgenscan bestehen, erweisen sich bei der Untersuchung mit dem fortschrittlichen Röntgensystem von Nikon als fehlerhaft. Nach dem chemischen Polieren zeigt die erneute Abtastung eine erheblich verbesserte Oberflächenglätte, die zu einer deutlich besseren Leistung der Endprodukte führt. Die Fähigkeit, diese greifbaren Vorteile nachzuweisen, ist der Grund, warum Kunden immer wieder zu REM Surface Engineering zurückkehren.
Die gleiche Sprache sprechen
Die Partnerschaft zwischen REM Surface Engineering und Nikon Metrology ist deshalb so erfolgreich, weil beide Unternehmen über ein solides Fundament an technischen und wissenschaftlichen Grundlagen verfügen. Ihre Teams sprechen die gleiche Sprache und können effektiv zusammenarbeiten, um gemeinsam innovative Lösungen zu entwickeln.
„Das Nikon-Team hat uns bei der Bearbeitung einer Vielzahl von Legierungen sehr geholfen“, sagt Michaud. „Wir haben uns mit Komponenten aus Aluminium, Titan, Nickelsuperlegierungen und Kupfer an Nikon gewandt. Diese Metalle haben verschiedene Merkmale und werden unterschiedlich gescannt, doch gemeinsam waren unsere Teams in der Lage, all diese Anforderungen und Anwendungen zu unterstützen.“
Dr. Diaz stimmt zu, dass das hohe Maß an Unterstützung durch das Nikon-Team in Bezug auf die spezifischen Anforderungen von REM Surface Engineering ein wichtiger Bestandteil der erfolgreichen Zusammenarbeit war.
„Sie stehen immer zur Verfügung, um Ihnen bei technischen Fragen zu helfen, die während eines Projekts auftauchen“, sagt Dr. Diaz. „Wenn wir bei einem bestimmten Element eines Scans nicht weiterkommen, rufen wir einfach an, und fünf Minuten später haben wir eine Antwort – zusammen mit einem schönen Bild, das wir in einen Bericht einfügen oder dem Kunden zeigen können. Dieser Art von Service ist großartig.“
Da Fertigungsanwendungen immer komplexer werden und die Messung der Oberflächengüte immer schwieriger wird, verbessern die Ingenieure von REM Surface Engineering und Nikon ihre Prozesse, um bessere Oberflächengüten zu liefern, die den steigenden Anforderungen in verschiedenen Branchen gerecht werden.
Und mit der zunehmenden Verbreitung fortschrittlicher Fertigungsverfahren wie dem 3D-Druck wird es immer wichtiger, glatte Bauteiloberflächen zu gewährleisten. Mit den präzisen Röntgen-CT-Scansystemen von Nikon können Unternehmen Oberflächenmerkmale prüfen und messen, ohne das Bauteil zu zerstören. Diese zerstörungsfreie Mikro-Computertomographie ist ein wesentlicher Bestandteil des Fertigungsablaufs. Sie ermöglicht ein Konzept der kontinuierlichen Verbesserung, wobei die Oberflächengüte immer besser wird und immer mehr Vorteile bietet.
„Wir sind sehr zufrieden mit dem Team von Nikon“, sagt Michaud. „Sie sind reaktionsschnell, preisgünstig und großartig in dem, was sie tun. Deshalb sind wir ihnen gegenüber auch so loyal. Eine andere Option käme für uns nicht in Frage.“