In den letzten Jahren hat sich das Augenmerk verstärkt auf die wahrgenommene Qualität gerichtet – das Urteil der Kunden über die allgemeine Verarbeitungsqualität des Fahrzeugs. Dabei geht es in der Regel darum, wie gut die Karosserieteile zusammenpassen, insbesondere um den Spalt und die Bündigkeit zwischen diesen Karosserieteilen.
So ist beispielsweise der Spalt zwischen der Vordertür und der Hintertür nicht nur aus ästhetischen, sondern auch aus funktionalen Gründen sehr wichtig – wenn die Hintertür außerhalb der Vordertür liegt, kann dies zu Windgeräuschen im Innenraum führen. Um den korrekten Einbau der Anbauteile in Bezug auf Verkleidung und Endbearbeitung zu gewährleisten, muss die Rohkarosse in dem Karosseriebau korrekt zusammengebaut werden. Dies beginnt bei der Bauteilaufnahme, in denen die Teile der Unterbaugruppe befestigt und eingespannt werden. Da diese kleineren Teile zu einem Unterboden und schließlich zu einer Karosserie zusammengebaut werden, wirkt sich die Verarbeitungsqualität dieser größeren Baugruppen direkt auf die Passform und die wahrgenommene Qualität des fertigen Autos aus.
Die Löcher und Oberflächen, die die Aufnahmestifte und Klemmflächen verwenden, sind entscheidend für die Bauqualität und die letztendlich wahrgenommene Qualität. Genaue und präzise Daten für diese Merkmale sind unerlässlich, um sicherzustellen, dass die Aufnahmetechnik korrekt ist, und letztlich für die Fertigungsqualität der Rohbaukarosse, da dies direkten Einfluss auf die Passform und die Verarbeitung hat. Viele Karosseriebau-Werke verwenden die Inline-Messung, um den Unterboden und die Rohkarossen-Baugruppen zu messen.
Die meisten für diese Messung verwendeten Technologien sind relative Daten – sie sind nicht absolut genau. Die Daten von relativen Systemen sind nicht absolut genau und können nicht zur Bestimmung der Genauigkeit der Aufnahmetechnik – nach der Messung von Bohrungen und Spannflächen – verwendet werden. Wenn ein relatives System ein Problem feststellt (ein Merkmal, das außerhalb der Toleranz liegt), wird die Baugruppe normalerweise zu einem Referenzmesssystem (KMG) gebracht, um die Ergebnisse des Inline-Messsystems zu bestätigen oder zu widerrufen.
Durch die Verwendung eines absoluten, rückführbaren und genauen Messsystems für die Messung dieser Baugruppen im Karosseriebau können die Daten zur Anpassung der Aufnahmetechnik verwendet werden, um eine verbesserte Fertigungsqualität zu gewährleisten und eine genaue statistische Analyse des Prozesses zu erstellen, da die Daten absolut sind. Das Nikon Laser Radar kann in Produktionsumgebung eine Genauigkeit und Wiederholbarkeit auf „KMG“-Niveau erreichen, das genaue, rückführbare und vertrauenswürdige Daten liefert und es den Automobilherstellern ermöglicht, den Prozess und die Qualität der Baugruppen am Ort der Herstellung zu verbessern. Die Genauigkeit des Nikon Laser Radars kann mit einem unabhängigen Artefakt, z. B. einem Inora-Tetraeder, nachgewiesen werden. Das Laser Radar hat einen mit HA-KMG vergleichbaren MPE. Unten finden Sie Beispiele der Ergebnisse einer Inora-Messung.
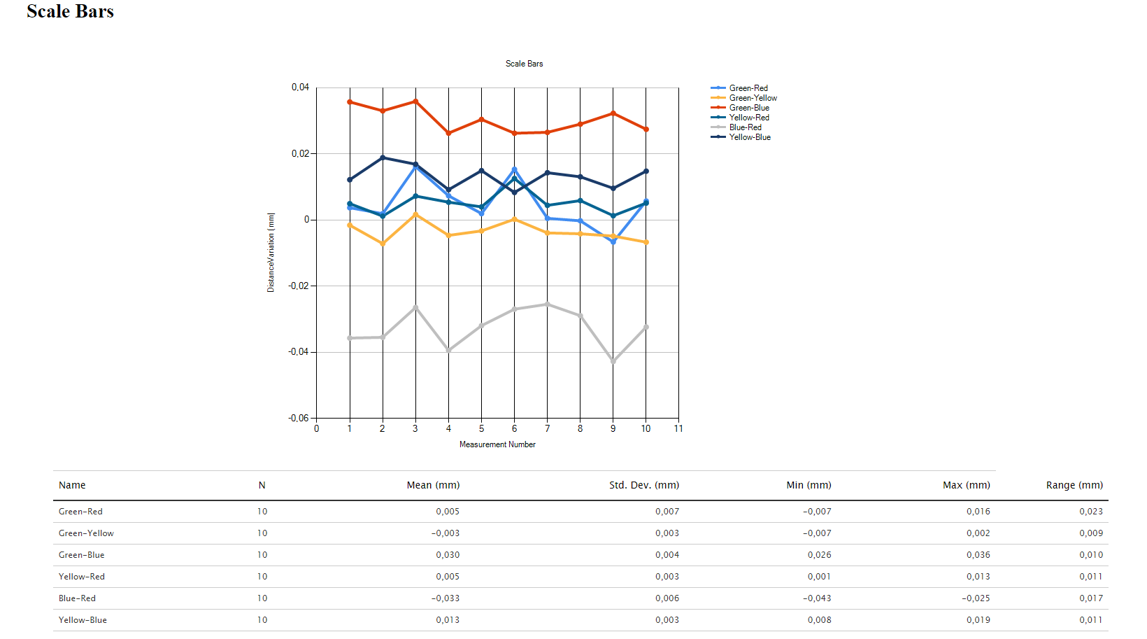
Bei der Vermessung von Teilen und Komponenten erfasst das Nikon Laser Radar mit einem Infrarot-Laserstrahl Scandaten in bestimmten Mustern, die auf das CAD-Modell abgestimmt sind. Bei der Messung von Löchern, Rechtecken, Polygonen und Flächen ist das Nikon Laser Radar in der Lage, die Oberfläche und die Kanten des Objekts zu scannen und dann das korrekte Ergebnis im Vergleich zum CAD-Modell zu extrahieren. Die Abbildung unten zeigt verschiedene Scanmuster, die für das Laser Radar zur Messung dieser wichtigen Merkmale zur Verfügung stehen.
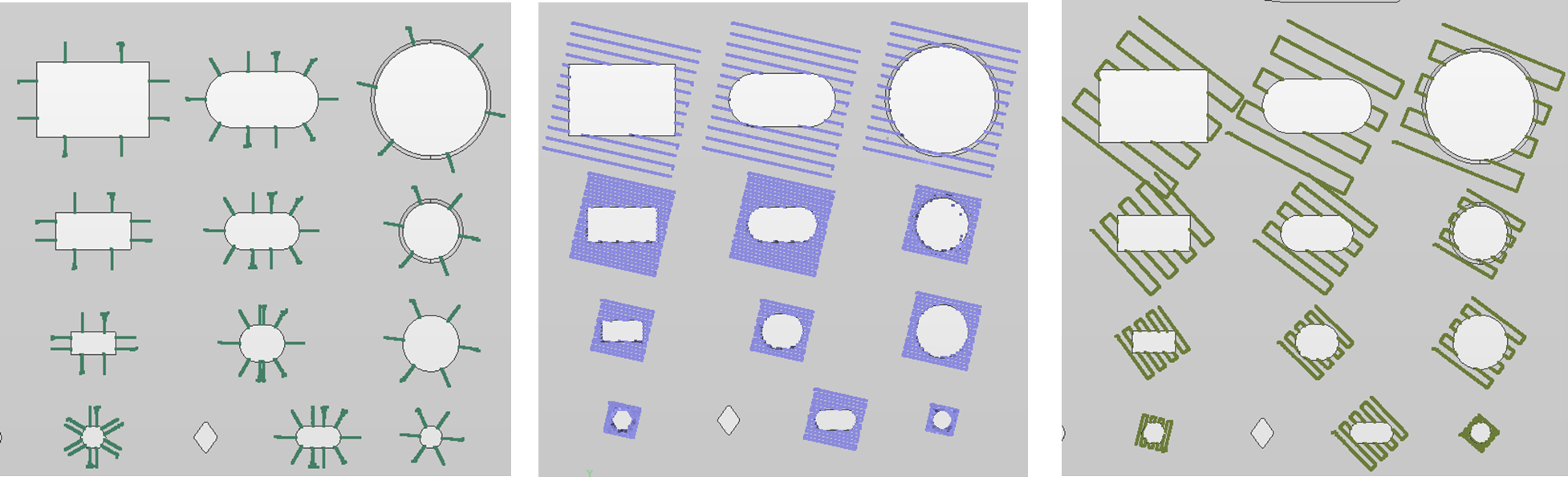
Vor Kurzem hat Nikon mehrere Tests für genau diese Funktionen an einem Testteil durchgeführt. Das Laser Radar hat jedes Merkmal 30 Mal aus verschiedenen Messbereichen und Winkeln gemessen, um die hohe Wiederholgenauigkeit zu demonstrieren. Diese Messungen wurden zwischen 1 und 5 Meter und bis zu einem Einfallswinkel von 60 Grad durchgeführt. Unten sehen Sie eine Abbildung des Aufbaus mit dem Laser Radar in 5 verschiedenen Bereichen des zu messenden Teils. Die folgende Tabelle zeigt den maximalen und durchschnittlichen Messbereich der gemessenen Position für jeden Merkmalstyp über alle Entfernungen und Winkel für das schnelle Sternmuster:
Merkmal | Loch | Langloch | Rechteck | Polygon | Oberfläche |
Durchschnittlicher Messabstand | 0,05 mm | 0,07 mm | 0,06 mm | 0,04 mm | 0,02 mm |
Max. Messabstand | 0,10 mm | 0,15 mm | 0,16 mm | 0,12 mm | 0,05 mm |
Messzeit | 2,6 s | 2,6 s | 2,3 s | 2,7 s | < 0,5 s |
Die Ergebnisse für die Wiederholgenauigkeit bei diesen Merkmalen liegen bei weniger als 160 Mikrometern mit einer durchschnittlichen Streubreite von weniger als 0,1 mm für 30 Messungen zwischen 15 und 60 Grad und von 1 bis 5 m für das Sternscanmuster und die üblichen Extraktionsparameter. Wenn Sie ein detaillierteres Scanmuster wie das oben gezeigte verwenden, kann die Streubreite auf unter 0,12 mm reduziert werden. Die Messung nimmt dann zwar mehr Zeit in Anspruch, ermöglicht aber auch Messungen bei höheren Einfallswinkeln.
Diese Daten verdeutlichen, dass das Laser Radar unempfindlich gegenüber Winkel- und Entfernungskonfigurationen ist. Da das Laser Radar Merkmale aus einer Vielzahl von Winkeln und Entfernungen wiederholbar messen kann, ermöglicht es ein großes Sichtfeld und eine hohe Merkmalsabdeckung. Daher sind nur wenige Positionen für eine Messung erforderlich, selbst über eine ganze Karosserie hinweg.
Die Möglichkeit, wiederholbare, genaue Daten in der Produktionsumgebung zu erhalten, wird den Kunden vertrauenswürdige und umsetzbare Daten liefern und es den Automobilherstellern ermöglichen, die Qualität der Baugruppen am Herstellungsort im Karosseriebau zu verbessern und zu validieren. Mit der Genauigkeit und Wiederholbarkeit des Nikon Laser Radar können wir das KMG in die Produktionsumgebung bringen und so hochwertige, genaue und wiederholbare Daten sicherstellen.
Hier können Sie weitere Informationen direkt von unserem Sales and Application Team in Europa erhalten und in unserem Ressourcenzentrum finden Sie Broschüren und ein Whitepaper.